A few years ago, a well-known lubricant and services provider conducted a survey of eight large U.S. Gulf Coast oil refineries relating to their oil consumption, mean-time-between-failure (MTBF) and lube application methods. The refineries’ pump bearing protection practices became the subject of closer scrutiny. These refineries had adopted using pure oil mist lubrication on thousands of pumps.
However, although it was assumed that the actual installation details for oil mist technology followed state-of-art practices, this was not always found to be the case. The survey identified important opportunities for cost-effective reliability enhancements.
Figure 1. Old-style (non-API type) oil mist insertion at
midpoint of bearing housing. Note that advanced face-type
bearing protector seals should not be used in conjunction
with this outdated and environmentally unfriendly type of
oil mist application.
This article covers an overview of oil mist lubrication, along with a brief review of past and current best practices in pumps and electric motors. Additionally, the application of cartridge-type API-610 10th (2006) edition-compliant, face-type quasi-hermetic seals in pump and electric motor applications will also be discussed.
Oil Mist Technology
The targeted surveys by the Houston-based provider confirmed that oil mist lubrication is the predominant method of lubricating pumps throughout the refining industry in the United States. Estimates of oil mist usage at 30 refineries in the Beaumont-Port Arthur area ranged from 80 to 90 percent. In this part of Texas, approximately 80 percent of the pumps at each refinery were serviced by the oil mist system. A U.S. West Coast consulting engineer estimated that more than 50 percent of all U.S refineries are using oil mist.
Indeed, oil mist lubrication is recognized as a key part of an API-based maintenance program at many refineries and pump mean time between failures (MTBF) of four to six years are being routinely achieved. MTBFs as high as 10.2 years are now on record at some of the more exceptional refineries.
Oil mist lubrication has been successfully used for pumps and their electric motor drivers in petrochemical plants since the 1960s. The basic process description is as follows: First, no liquid oil is placed in the bearing housing. Instead, an entirely static oil mist generator creates the oil mist in a central module that services all pumps within a radius of approximately 600 to 1,000 feet.
The mist is a mixture of atomized (less than three-micron) oil droplets mixed with air in a ratio of about 1:200,000. The mist, which has the appearance of light smoke, is moved out to the pumps via two-inch or four-inch piping in a low-pressure (less than 1 psi, approximately 5 to 6 kPa), low-velocity (less than 7 ft/s, about 2 m/s) process.
At the pump, the oil mist is inserted into each pump bearing housing through a small-diameter application fitting or reclassifier, which greatly increases the mist velocity, causing the droplets to collide and coalesce into larger, liquid drops of oil.
This air/oil mixture passes into the housing, where some of it contacts and lubricates the bearings, while much of it falls straight through to the bottom of the housing. The coalesced oil finally passes through a hole in the bottom of the housing and is collected for disposal (Figure 1).
The advantages of oil mist lubrication include:
-
Almost completely maintenance-free and self-checking. It is no longer necessary to rely on operators to check and fill housings with oil.
-
Better lubricant properties, because the oil on the bearings is always new.
-
Lower operating temperatures, typically 10°F and often 20°F (approximately 6°C to 12°C).
-
Reduced power requirements, because the bearings operate in a thin film of oil instead of plowing through a pool of oil.
-
Protection of nonrunning (standby) pumps. Maintaining an oil fog environment at all times greatly reduces bearing degradation and the resulting risk of premature failure.
The MTBF benefits of oil mist over oil traditional sump lubrication of rolling element bearings have been well-documented, and the oil mist lubrication option was included beginning with the API-610 Seventh Edition in 1989.
Plant-wide oil mist lubrication evolved at about the same time as rotating labyrinth isolators (1960s and ’70s), and the dependence of earlier oil mist application methods on leaking labyrinth technology can be seen in Figure 1. Quite obviously, as oil mist enters through an application orifice into the much larger bearing housing, its velocity will slow down.
Droplets collide and become larger. They then tend to fall out of suspension to the bottom. It should also be noted that certain bearing cages create “windage”- a fan effect that tends to push the mist away from the rolling elements.
Yet for oil mist to reach the bearings, atomized oil droplets admitted at a single point near the center of the bearing housing must turn and travel horizontally. In these earlier oil mist applications, horizontal mist flow is accomplished by using either straight labyrinths or a rotating labyrinth isolator. Either labyrinth style allows continuous mist leakage, thus creating a flow path for the air/oil mixture through the bearings and out into the atmosphere.
Recall, however, that with much of the oil mist having taken the path of least resistance and collecting at the bottom of the housing, more oil mist must be supplied. To compensate for this bypass loss and to properly lubricate highly loaded back-to-back thrust bearings, refineries often overmist by a factor of at least four times to ensure that sufficient oil passes through the bearings.
It should be of interest that Environmental Protection Agency (EPA) regulations tightly control the release of volatile organic compounds (VOC), such as gasoline, benzene and others. However, the oil mist that is escaping is not volatile; it is present as small atomized droplets of liquid oil which do not evaporate.
Most of the droplets fall to the ground near the pump. As such, the EPA-mandated VOC monitors do not detect the oil mist emissions (stray oil mist) and there is presently no official regulatory pressure to stop the emissions.
Figure 2. Advanced, cartridge-type dual-face,
magnetically energized bearing isolator. This isolator
provides a quasi-hermetic seal for the bearing
housing. (Source: AESSEAL, Inc., MagTecta II®)
It is important to understand that the oil mist insertion and flow path methods shown in Figure 1 and advocated in the superseded API-610 Seventh Edition will not allow the use of advanced magnetic bearing housing seals. Advanced double-face magnetic bearing protector seals of the type shown in Figure 2 create a virtually hermetic seal.
Because quasi-hermetic seals will not permit air and/or oil to leak to the atmosphere, using these seals while applying oil mist as shown in Figure 1 would restrict the flow of oil over the bearings. Therefore, a better way was devised to apply oil mist, and this method is reflected in the eighth and later editions of API-610.
Advances in Oil Mist Application Technology
Recent industry guidelines (including API-610 10th Edition) no longer show the older practice of injecting oil mist into the center of a bearing housing. In fact, since the release of API-610’s Eighth Edition in 2000, API has recommended that the oil mist be dual-injected into the region between the bearings and the isolators.
Figure 3 shows this up-to-date practice on an electric motor; however, it is now also widely used on centrifugal pump bearing housings at best-practices plants. Because many U.S. Gulf Coast refineries are not presently in compliance with current API-610 best practices, this upgrading would represent a valuable enhancement opportunity.
Figure 3. API-compliant dual-point oil mist injection, at
locations between the bearings and the isolators in an
electric motor. (Source: AESSEAL Inc., UK and Knoxville, Tenn.)
In addition, it may be possible to reduce the overall quantity of oil used in oil mist systems by factors as much as four, simply by converting from a center-injection to a dual-injection plan, thus creating a 75 percent savings in the cost of lubricating oil. This is due to the fact that all of the oil must travel through the bearings, and none can travel straight down the center of the housing.
Although not presently mandated by the EPA, there are certainly other strong reasons to discontinue continual oil mist leakage into the atmosphere around every pump. From the viewpoint of being a good neighbor, most refineries will be interested in creating as few oil emissions into the environment as possible.
From a wastewater (or API separator) processing perspective, the more waste oil on the ground that washes down the oily-water sewer, the more money it costs to extract that oil before discharging the wastewater to a stream or to the municipal sewer. From a housekeeping perspective, it is clearly advantageous to not have a ring of oil spillage on the ground.
Closed-loop Oil Mist Systems
Although closed-loop oil mist systems have been used indoors on certain textile machinery since the early 1960s, it took until the early 1990s for closed systems to be used refinery-wide. The most recent systems apply API-610-compliant, dual-point injection and, by virtue of their closed-loop design, recover up to 99 percent of the lube oil.
Closed oil mist systems require a near-perfect seal (such as the one shown in Figure 2) just outboard of the bearing, in order to contain all the lubricants in the system. Closed systems do not allow stray mist to escape into the environment which is clearly advantageous.
As mentioned earlier, the application of pure oil mist is not restricted to refinery pumps alone. Most refineries have found oil mist highly successful in extending MTBF for their electric motors as well and have used pure oil mist on electric motor drivers in the 15 hp and larger sizes. In Baytown, Texas and Baton Rouge, Louisiana, hundreds of electric motor oil mist conversions and new installations date back to the early 1970s.
Before magnetic bearing isolators were used in electric motors, a small weep hole (0.06 to 0.13-inch diameter) was provided in a drain plug located at the bottom of the various electric motor casings to drain accumulated moisture condensation and to allow condensed oil mist to escape. It is important to note that this weep hole did not affect the rating of explosion-proof motors.
Traditionally, most electric motors have been configured for grease lubrication. If oil mist is injected into the motor bearings, it becomes important to isolate the bearings from the windings to prevent oil buildup on the windings, which is shown on the drive end of the electric motor in Figure 3. Although clean oil alone is an insulator and might not cause electrical problems, oil tends to hold on to dust and dirt, which can degrade motor performance.
Neither lip seals nor straight or rotating labyrinth isolators can seal out oil mist; only face seals are effective hermetic seals. With available axial space limited, magnetically energized bearing isolators will fit where spring-activated face seals could not be accommodated. Several refineries in Southeast Texas are presently planning similar electric motor conversions.
In summary, the following three areas are considered by experts to make a compelling case for advanced face-type magnetic bearing seals in the refining and petrochemical industries:
1. API 610, Eighth and Later Edition Pumps
(Dual injection of oil mist.) All of the industry-leading refineries are moving toward this approach. Dual-injection oil mist has been proven to be a superior lubrication method, but is not well-known in some refineries, especially among smaller refineries.
With the use of advanced cartridge-mounted face-type magnetic bearing isolators, the reuse of the collected oil is now both feasible and economical. This makes it relatively easy to cost-justify premium priced, superior-quality synthetic lubricants, which appears to be the direction in which technology is heading.
2. Electric Motors
As pump MTBF at most refineries approaches six to seven years, electric motors are being identified as the machine component with the greatest repair cost. Oil mist lubrication is a proven method of increasing MTBF on motors as well as pumps. On electric motors, however, it is often advantageous to use face-type protector seals to fully isolate the windings from the oil mist lubricant.
3. Housekeeping/environmental
Oil mist on the ground is not in anyone’s best interest. Systems which allow leaking oil mist into the atmosphere through labyrinth seals are no longer acceptable to image-conscious users and users who pride themselves in applying the best available technology. Moreover, containment and full capture/recovery of the lube oil makes economic sense. Again, this points to the merits of using face-type magnetic seal technology.
Editor’s Note
The service provider who conducted the study of refineries has asked to keep its name and the names of participating refineries confidential.
Recommended Reading
1. Bloch, Heinz P. and Shamim, Abdus. Oil Mist Lubrication: Practical Applications. Fairmont Publishing Company, ISBN 0-88173-256-7, 1998.
2. Bloch, Heinz P. Practical Lubrication for Industrial Facilities. Fairmont Publishing Company, ISBN 0-88173-296-6, 2000.
3. Bloch, Heinz P. and Budris, Allan. Pump User’s Handbook: Life Extension. Fairmont Publishing Company, ISBN 0-88176-517-5.
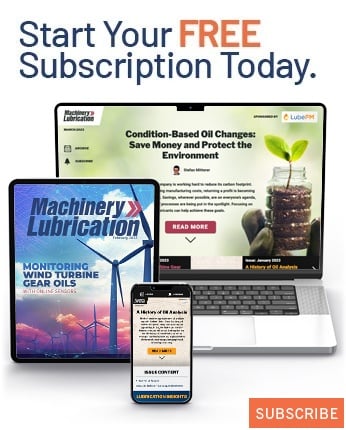