It has been observed that various power stations throughout Duke Energy have CE Bowl Mill gearboxes for pulverizing coal that are chronically producing excessive amounts of wear metals.
To reduce the wear metals, the following actions were pursued. Oil filtration was added to remove the wear particles along with any ingressed particles (for example, dirt, coal dust, fly ash, etc.).
Gearbox rebuilds were also performed to reduce wear particle generation. Both of these attempts temporarily reduced wear, but ultimately, abnormal wear rates returned. The next feasible solution was to test lubricants to see if an alternative lubricant would provide better protection.
Wear Metal Problem
Wear metals in the oil sample test results from the gearboxes had remained high at several locations despite the addition of oil filtration and gearbox rebuilds. It was decided to pursue alternative lubricants.
The current lubricant recommended by Alstom, the original equipment manufacture (OEM), is Exxon Spartan EP 320. This lubricant is an ISO VG 320 oil with extreme pressure (EP) additives. It was decided to test an ISO VG 460 instead. It is believed that the ISO VG 460 would provide better film strength and reduce the formation of wear metals.
Field Testing Lubricants
The first power stations to test alternative lubricants were Allen, Cliffside, Marshall and Riverbend. As stated previously, the alternative lubricants tested were ISO VG 460, which is one ISO viscosity grade higher than the OEM recommendation.
Allen’s mill gearboxes were changed to Exxon Cylesstic TK 460 compounded worm gear oil. Cliffside’s mill No.5 gearbox was changed to Spartan EP 460. This oil contains the same additive package as Spartan EP 320. Marshall’s mill gearboxes, Cliffside’s mills Nos. 1 through 4 gearboxes, and Riverbend’s mill gearboxes all changed to a Mobil SHC 634. This lubricant uses a polyalphaolefin synthetic base oil.
The Exxon Cylesstic oil used at Allen (AS) and the Mobil SHC oil used at Riverbend (RB) provided similar improvements in copper wear debris generation. The copper content generated in these gearboxes on average dropped from 200 ppm to 25 ppm (Figures 1 and 2).
Figure 1. Trend of Mill Gear Wear
Changed Oil from Spartan EP 320 to Cylesstic TK 460
Figure 2. Trend of Mill Gear Wear
Changed Oil from Spartan EP 460 to Mobil SHC 634
Notice that after the oil change, the copper content remained low. The copper level for Marshall’s (MS) mill gearboxes that were changed to Mobil SHC were reduced from an average of 60 ppm to 5 ppm (Figure 3).
The gearbox MS 1B at Marshall’s mill has a defective bearing, the average copper content was reduced from 37 ppm to 2 ppm. The Spartan EP 460 oil was used only on Cliffside Station’s Unit 5 mills. After the oil change, the copper ppm was low, but it returned to 25 ppm to 35 ppm within six to twelve months (Figure 4). ExxonMobil attributed the increase in copper content to the EP additives in Spartan EP.
It concluded that a chemical reaction between the EP additive and the bronze gear is occurring due to the locally high temperatures at the gear contact points.
Figure 3. Trend of Mill Gear Wear
Changed Oil from Spartan EP 320 to Mobil SHC 634
Figure 4. Trend of Mill Gear Wear
Changed Oil from Spartan EP 320 to Spartan EP 460
The tests performed on these gearboxes indicate that the wear metal concentration has been reduced in most of the gearboxes due to the change in lubricant type. Successive tests have shown that the wear metals remained lower with the change of an ISO VG 460 than with a regular oil change using an ISO VG 320.
Continuous filtration may also be employed to achieve the lowest wear metal concentration economically feasible. Continuous filtration has been installed on the following mills: Allen’s mills units 1 through 5, Cliffside’s unit No. 5, Marshall’s units 1 through 4 and Riverbend’s mill 7B.
Cost Analysis Solutions
The initial purchase price and the service life of the oil affect the overall lifecycle cost of the lubricant. Exxon Spartan EP oil may exceed five years of service with continuous filtration and no water contamination. The life span of Exxon Cylesstic TK 460 is expected to be between two to five years depending on the gearbox temperatures.
Exxon Cylesstic TK 460 is a cylinder oil, and cylinder oils are more susceptible to oxidation than other oils. Spartan EP mixes well with water, so a cooler leak will result in lubricant degradation unless a vacuum dehydrator is used to remove the water. Of the lubricants considered for the gearboxes, Mobil SHC 634 has the longest expected service life of 10 years with continuous filtration.
Contamination is more likely to shorten the service life of Mobil SHC 634 than oil degradation. Mobil SHC 634 does not mix well with water. If a cooler leak does occur, it is generally sufficient to just drain the free water from the reservoir.
The different oils being tested made significant reductions in gearbox wear. All of the ISO VG 460 oils perform better than the ISO VG 320 oil, therefore a lubricant selected from the ISO VG 460 oils should be based upon the lifecycle cost.
The ratio of each alterative lubricant cost to the original lubricant cost is used to compare the lubricants. Spartan EP 460 is the least expensive oil with the same cost as Spartan EP 320. Exxon Cylesstic TK 460 is 1.29 times the cost of Spartan EP.
It is currently being phased out by Mobil 600W Super Cylinder Oil that is 1.52 times the cost of Spartan EP. Mobil 600W Super Cylinder oil will be used in the place of Exxon Cylesstic TK460 for the continuation of this case study. Mobil SHC 634 at 5.42 times the cost of Spartan EP has the highest initial purchase cost. Table 1 summarizes the cost and the life span of the lubricants.
Table 1. Lubricant Lifecycle Cost Comparison
Recommendations
Spartan EP 460 performs better than Spartan EP 320. However, it is not recommended because the EP additive reacts with copper alloys. Mobil 600W Super Cylinder Oil has the lowest initial cost of the two lubricants that performed well in the test.
If a service life of three to five years can be achieved, this may be the most economical choice. The labor involved in changing the oil and the used oil disposal costs have been assumed negligible, but if they were considered, the higher priced Mobil SHC 634 with a life span of 10 years may be the best choice. Mobil SHC 634’s service life of 10 years is susceptible to contamination without effective continuous filtration.
The life of this lubricant may be dramatically reduced without proper filtration. In this situation, Mobil 600W Super Cylinder Oil is recommended because the cost of replacing the contaminated oil is lower.
References
- Mobil Cylinder Oils Product Data Sheet. Jan. 2006. ExxonMobil Lubricants and Specialties. June 1, 2006.
- SPARTAN EP Product Data Sheet. April 2005. ExxonMobil Lubricants and Specialties. June 1, 2006.
- Exxon Cylesstic Product Data Sheet. April 2005. ExxonMobil Lubricants and Specialties. June 1, 2006.
- Mobil SHC 600 Series Product Data Sheet. April 2006. ExxonMobil Lubricants and Specialties. June 1, 2006.
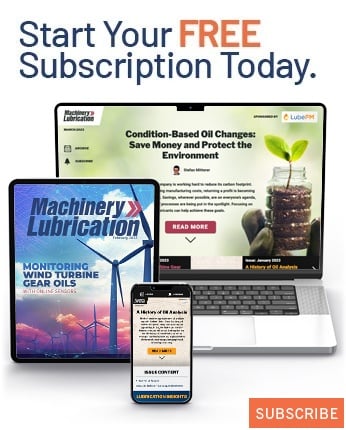