We all know lubrication is the lifeblood of machinery. But how do we know our lubricants are doing their job? Well, that’s where an effective lubrication program steps in. Think of it as your doctor prescribing medications and monitoring vital signs to make sure you’re in top shape. An effective lubrication program is what keeps our machinery healthy, which ultimately leads to operational reliability and equipment longevity. However, numerous challenges and pitfalls plague organizations, preventing them from establishing a successful program – ranging from incorrect lubricants to poor lubrication practices, lack of personnel training, and resistance to culture change. These factors contribute to decreased performance, increased downtime, decreased morale…the list goes on.
This article sheds light on those lubrication challenges, advocating for best practices, raising awareness of potential pitfalls, promoting cultural change, and demonstrating the benefits of embracing a comprehensive lubrication program.
Lubrication Challenges
First, let’s look at the most common challenges associated with machinery lubrication, standing in the way of an effective lubrication program.
- Contamination control – Particles and debris, water ingress, and chemicals lead to problems like abrasion, wear, rust and corrosion, degradation of lubricant quality, and even hazardous chemical reactions.
- Lubricant degradation – Exposure to oxygen and high temperatures causes sludge and varnish to form, and lubricant breakdown, reducing its effectiveness and requiring more frequent changes. Mechanical stress also degrades lubricants, especially greases, thus reducing their ability to protect moving parts.
- Improper lubricant selection – Too often lubricants are chosen based on costs without considering compatibility issues. Mixing incompatible lubricants can lead to chemical reactions, which in turn leads to downtime. It’s also important to consider machinery compatibility since different components can react differently and have different failure modes as a result.
- Operational factors – Frequent equipment starts and stops, as well as varying loads and speeds, can cause fluctuations in lubrication distribution and lead to increased wear.
- Economics – High-performance lubricants can be expensive, and implementing an effective lubrication program can be resource-intensive. However, inadequate lubrication leads to machinery failure and unplanned downtime with mounting repair costs and lost productivity.
- Lack of understanding – When operating conditions, lubrication intervals, and maintenance techniques (such as oil analysis) are not fully understood, over-lubrication or under-lubrication can easily occur leading to component failure.
By addressing these challenges through strategic planning, regular monitoring, and adopting best practices, machinery performance and lifespan can be significantly enhanced.
Six Lubrication Best Practices
So, what are the best practices to incorporate into a lubrication program? In direct response to the above challenges, I recommend these practical solutions:
- Mitigate contamination - Use filters with the proper beta ratio to prevent contaminants from entering the lubrication system; create a labeling standard for lubricant naming and identification to prevent cross-contamination; use quick connects instead of pour spouts to top up equipment; and regularly check and replace filters.
- Prevent lubricant degradation - Monitor operating conditions; perform oil analysis; check on additive/contamination levels; and most importantly, store your oil in a designated place under conditions that will keep it CLEAN, COOL, and DRY for the longest shelf life.
- Ensure proper lubricant selection - Select lubricants designed for specific temperature ranges; use multi-viscosity oils for variable operating conditions; implement pre-lubrication systems for start-up operations; consult machinery manuals and lubrication experts; and consider the application of synthetic lubricants for extreme conditions.
- Optimize lubrication process - Train personnel in proper lubrication techniques, use automated lubrication systems where feasible, and establish a comprehensive lubrication schedule tailored to specific equipment needs.
- Adopt cost-effective economic strategies - Conduct a cost-benefit analysis for purchasing high-quality lubricants, implement predictive maintenance to reduce downtime, and invest in a reliable lubrication system to minimize long-term costs.
- Assign knowledgeable SMEs - Give lubrication duties to only carefully vetted professionals (internal or external) well versed in lubrication practices to maintain the accuracy and integrity of the entire lubrication cycle.
Potential Pitfalls
Whether a lubrication program is already in place, or in the planning stage, be aware of some pitfalls that could potentially compromise an effective program.
Over-lubrication increases fluid friction, generating excessive heat that can cause seal damage, leaks, and contamination ingress, resulting in higher costs and waste of resources. Under-lubrication, on the other hand, increases machinery wear and tear due to overheating and makes equipment components more susceptible to rust and corrosion.
Selecting the incorrect lubricant for temperature or load conditions can impact performance by not providing adequate protection and shortening the life of the lubricant, thus requiring more frequent changes and increasing costs.
Cross-contamination from mixing different lubricants can cause chemical reactions that reduce effectiveness and increase wear. The metal particles from wear and tear then circulate in the lubricant, causing further damage.
Poor lubrication practices stemming from inadequate application techniques, ignoring manufacturer recommendations, or a lack of training can potentially introduce errors into the lubrication process.
Neglecting regular maintenance, such as a failure to regularly monitor lubricant condition, replace filters when necessary, or the prolonged use of degraded lubricants can lead to significant machinery damage.
Environmental factors can cause harm, including temperature variations that alter lubricant viscosity, humidity and moisture that cause lubricant emulsification and corrosion, and dust and particulates in harsh environments that contaminate the lubricant.
Then, there are economic constraints that can lead to setbacks and poor outcomes. For example, cost-cutting may dictate the use of lower-quality lubricants or longer lubrication intervals, as well as postponing the purchase/use of advanced monitoring tools (such as ultrasound equipment, thermography, vibration, or oil analysis kits).
Finally, lubrication programs can face technological limitations, e.g. outdated systems that do not provide consistent or adequate lubrication, and legacy monitoring methods that do not provide real-time data on lubricant condition and machinery performance.
Culture Change: Overcoming Resistance
For a lubrication program to succeed, organizations need to create a culture that values and prioritizes proper lubrication practices at all levels. A shift in mindset based on the following principles will help overcome the usual resistance to such a widespread culture change:
- Leadership commitment – management leading by example, committed to the lubrication program by actively participating and promoting best practices, along with a clear vision and goals.
- Effective communication – awareness campaigns to highlight the value of lubrication and feedback channels for employees to make suggestions in a collaborative environment.
- Education & training – programs for all relevant personnel, e.g. maintenance staff, operators, and engineers, focusing on lubrication best practices, the importance of proper lubrication, and the consequences of neglect.
- Standardization & documentation – lubrication procedures and schedules tailored to each piece of equipment, supported by checklists and detailed recordkeeping to track compliance and identify areas of improvement.
- Monitoring & metrics – defined KPIs (for equipment uptime, maintenance costs, and lubricant consumption), as well as regular audits and inspections to ensure Lubrication Program effectiveness.
- Advanced technologies & tools – software solutions to manage and track lubrication activities, as well as condition monitoring tools (e.g. oil and vibration analysis) to assess the health of lubricants and machinery in real time.
- Incentives & accountability – assignment of roles and responsibilities for lubrication tasks, as well as recognition and reward of employees who follow best practices and contribute to the success of the program.
- Continuous improvement – periodic reviews and updates of lubrication procedures to reflect feedback, audit results, and technological advancements, as well as root cause analysis to investigate lubrication failures or issues so they do not recur.
- Benchmarking & consulting with experts – stay competitive and innovative by comparing lubrication practices with industry standards and best practices, as well as leveraging the knowledge and perspectives of external lubrication expertise.
Incorporating these cultural changes into the company’s core values and operational philosophy will bring machinery lubrication to the same level of concern as safety and quality standards.
Lubrication Program Benefits
A well-designed, well-organized lubrication program formalizes processes and procedures, bringing consistency and accuracy for more efficient, reliable, and cost-effective operations. When the above best practices and culture changes are adopted, and the pitfalls are taken into account, businesses achieve substantial benefits, including:
- Extended equipment life
- Improved equipment reliability
- Enhanced performance and efficiency
- Cost savings
- Improved safety
- Reduced waste / lower hazardous emissions
- Streamlined maintenance processes
- Regulatory compliance
- Quality assurance
- Boost in plant morale
Conclusion
The importance of an effective lubrication program cannot be denied. It is the key driver for optimal performance and longevity of industrial equipment. Proper lubrication reduces friction, wear, and heat, which can significantly extend the life of mechanical components and improve overall efficiency. Therefore, the health of your machinery is reflected in your bottom line.
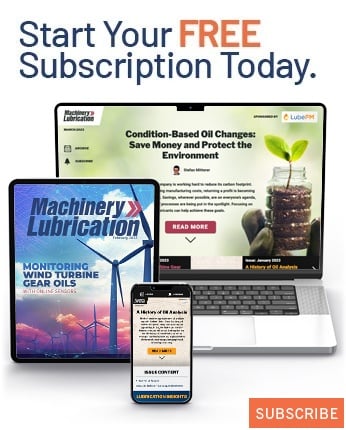