Duhva is an opencast mine operating in the Mpumala District of South Africa. Every year the mine is responsible for delivering 9.8 million tons of crushed coal to a 3600 megawatt power station.
With a new directive to implement a contamination control program, Duhva formed a task group to investigate the source of contaminated oil coming into the company’s new oil supply.
In an environment where you breath more dirt than air, we knew that the odds weren't on our side when we set the cleanliness target of a ISO 17/13 for all oil components. The fact that the new oil (SAE 30 & 10) was arriving at a cleanliness of 22/15 didn't make this task any easier. Analysis of the new oil showed that the majority of the contamination was made up of silicon - our first clue.
Management set up a team, made up primarily of diesel mechanics to investigate why the new oil supply was so dirty and to suggest remedial action. The objective was to make the mechanics aware of the problem and involve the craftsmen with management in setting up a contamination control program. The team appropriately named themselves "Duvha Oil Slick".
Taking samples of the bulk oil confirmed the high contamination level of the oil. The SAE 30 and SAE 10 oils were arriving, as previously stated, at a contaminant level of 22/15. The first step was to determine where the contamination was entering the oil.
Was it already dirty before it left the refinery, or was it contaminated during transport? A trip to the refinery confirmed that the oil was clean (ISO 16/13) before being transfered to the tankers. Our next step was to observe and monitor the oil tankers, which were subcontracted by the oil company. The following observations were noted:
Cleanliness of Bulk Oil Tankers. The team visited the contractor and was lucky enough to find an oil tanker on-site that had just been cleaned before going down to collect its next load. The tanker still had sediment in the bottom and water had been used to clean it out. The team recorded that not all the water had been drained out.
The flaps on top of the tanker were apparently left open on the 600 km trip down, which helped to air dry the inside of the tanker. On arriving at the refinery the tanker was immediately loaded, without prior inspection to ascertain its cleanliness. These findings, in the team's opinion, was one of the major sources of contamination in the new oil.
Filling Up of Bulk Tanks. The team monitored the filling of the mine's bulk tanks from the tanker and the following was observed:
Hoses used between the tanker and pipe connectors were not sealed between usage. These oil-wetted connectors can act like dirt magnets, collecting dirt from air and everything they contact. Also, there was no prior cleaning or flushing of hoses before connecting up and pumping the oil.
Leaking oil from bad fittings on the tanker was collected in a 20 liter drum and poured back into the tanker when pumping was complete. This was another obvious source of contamination.
Measuring of Oil Level in Tank. This task was undertaken by our Stores Clerk, using a dipstick that layed in the open environment between measurements. Both the dipstick and the plug, through which the dipstick was inserted, were not cleaned prior to usage. It was concluded that opening and closing this uncleaned plug was a definite source of contamination which could easily be avoided.
Air Breathers on Tanks. All air breathers on the tanks were inefficient and wrongly installed. The breathers were turned upside-down allowing dust and water to enter. To make matters worse, the main road runs more than 100 meters from the storage tanks, creating a very dusty environment.
To resolve the above mentioned sub standards the following solutions were suggested and implemented:
Dirty Tankers. A directive was issued by the oil supplier that all tankers would be cleaned appropriately by the contractor,
and on arriving at the coast, would first be checked by an independent quality control inspector and issued with a certificate of cleanliness. This certificate was to be handed to the mine, upon delivery of the oil.
Filling up of Bulk Tanks. All leaks from the tankers were to be repaired, eliminating the need for tins to catch leaking oil. All connecting hoses were to be appropriately stored with dust caps. The operators of the tankers were instructed on how to suitably clean the hose connections before coupling up.
Inlet Filters Installed Before and After Tanks. Inlet filters were installed before the tanks by the oil company to clean the oil of any contamination that may have inadvertently entered the tanker. The mine did not specify the filters but only insisted on a cleanliness level of 17/13. The mine installed its own filters after the tanks as a precautionary measure. This decision, which at first looked like a waste of money, has proved to be justified, as on many occasions the oil still arrived above the required cleanliness level.
Measuring of Oil Level in Storage Tanks. An outside sight glass was installed on the end of the tank to allow stores to note the level of oil. This also proved a safety feature as the storeman did not climb the vertical ladder to the top of the tank to take measurements.
Air Breathers on Storage Tanks. Air breathers with an absolute rating of 3 microns, replaced the existing breathers.
The team also highlighted and corrected a number of other practices at the mine (listed below) which were not conducive to a good oil contamination control program:
• Filling nozzles in the workshops were left in a dirty drip tray after use and not cleaned before re-use.
• Hydraulic components were stripped and assembled in a dirty environment.
• Air breathers on the coal haulers were wrongly positioned.
• Makeup oil introduced to some machines was via used dirty containers.
• Bearings and gears were left uncovered between stripping and assembly.
• New bearings and oil filters were left open to the environment in the stores.
Conclusion. At present the oil is arriving at the mine at a cleanliness level of 18/15, which the mine has accepted. Duvha management fully endorsed the participative management approach to contamination control. Committees have now been set up in each section to deal with their own particular problems and to provide the necessary solutions.
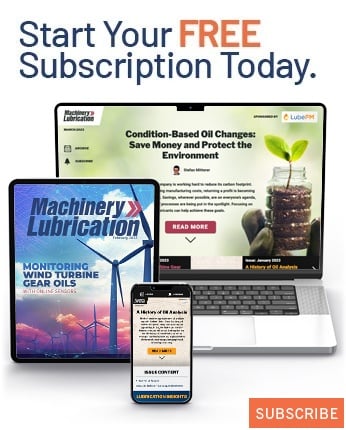