What's the first image that comes to mind when you think about off-road equipment? How about tremendous power to move dirt, gravel or stone; or the ability to haul larger, heavier loads at higher speeds on steeper inclines. Add in longer equipment life, less maintenance and lower overall cost and this is the basis of what owners and fleet managers want their off-road equipment to deliver.
This is quite a change from the off-road equipment available just 20 years ago. As engine power continues to increase with each successive model (typically at least five percent more in horsepower and torque), the result is a greater load on the transmission, differential and final drive. These higher loads and speeds increase the overall power density in the driveline and raise oil sump temperatures. The challenges in developing equipment are being met through major advances in heat treating, surface finishing, geometry and metallurgy. However, sophisticated hardware and manufacturing techniques also need to be matched with advanced fluid technologies to gain maximum benefit from today's advanced final drive components and powershift transmissions.
Lubricating Yesterday's Powershift Transmissions
The original lubricant of choice for many older transmissions was engine oil, which performed multiple functions in the engine and drivetrain. Although convenient, using the same lubricant in both compartments is usually not the best choice. Its use can result in too much compromise, particularly as transmissions become more sophisticated, nonmetallic friction materials are used in clutches and brakes, and major changes have occurred in the composition of engine oils.
For example, compared to specialty oils, engine oils may not perform as well in wear performance because of reduced phosphorus and sulfated ash, or in friction stability due to an imbalance of detergents and dispersants. The dispersants used in new-generation engine oils may interact poorly with seals. Why? Because fundamentally, engine oil technology is driven by the needs of advanced engine designs; and the performance in the transmission or final drive is an afterthought at best. Dedicated off-road driveline lubricants, on the other hand, offer specific design features that are driven by the needs of the transmission and final drive.
If engine oils were used in the transmissions and final drives of today's equipment, the engineered limits would not meet the needed performance levels. Engine oils would likely allow clutch slippage and higher temperatures resulting in pump wear, reduced shift response and increased maintenance. The absence of the needed frictional properties in the fluid could result in vibration and noise in wet brakes. Also the oil might attack nonmetallic components, creating leaky seals, gear wear and damage. For example, the fluid could cause the elastomer materials to turn brittle - an undesirable result.
State-of-the-Art Powershift Transmission Fluids
As it became clear that the use of engine oil in transmissions and final drives in newer equipment was a poor choice, the lubricant industry had to rethink how fluid would interact with powershift transmissions and final drive components. Therefore, dedicated drivetrain oils were developed and the results were dramatic. For instance, these oils allow for rapid, frequent shifting without power loss, resulting in less heat and increased clutch durability. Operator fatigue and maintenance costs were reduced while productivity increased - making the dreams of owners and fleet managers come true.
But this is just the tip of the iceberg. Today's fluids are required to perform a myriad of functions, such as the following:
-
Frictional Stability - Delivering and maintaining desired frictional properties in metallic and nonmetallic materials ensures operating efficiency when moving heavy loads on inclines. The frictional needs of clutches and wet disc brakes are also addressed, eliminating excessive brake noise. Good frictional stability results in longer clutch life, and longer trouble-free equipment life with reduced downtime.
-
Antiwear Protection - Protecting planetary and helical gears, highly loaded final drive gears and bearings against macropitting and metal fatigue.
-
Compatibility - Interacting with elastomers used in rings and seals without producing leaks, and with metals used in bronze alloys and components without producing corrosion and rust.
-
Low-temperature Fluidity - Inhibiting wear in cold weather starting and allowing easier cold weather operability.
-
Oxidation Stability - Ensuring the fluid won't degrade at high temperatures, resulting in longer fluid life, particularly in extreme conditions.
-
Sludge Control - Preventing lubricant passages from being blocked, resulting in longer equipment life.
-
Rust and Corrosion Protection - Extending equipment life and trouble-free operation.
-
Foam Protection - Stopping fluid loss due to foaming (air bubbles do not provide lubrication), reducing wear from metal-to-metal contact and protecting the operator from the fire and safety hazards associated with fluid overflow.
-
Thermal Stability - Providing consis- tent performance under a variety of temperatures.
-
Hydraulic Pump Performance - Protecting high-pressure hydraulic systems.
-
Lubrication - Covering clutch, wet brake, vane pump, planetary gear sets, final drive gears and bearings (metal-to-metal).
-
Sustained Film Thickness - Promoting protection of highly loaded gears and long-term antiwear protection.
-
Shear Stability - Maintaining the viscosity grade over the life of the lubricant and providing wear protection, resulting in no loss of applied pressure that could result in slippage and equipment failure.
Choosing the Right Fluid
Today's off-road equipment owners and fleet managers can select from two basic types of dedicated fluids:
-
Single Grade - Requires fluid change depending on the season. For example, SAE 30 or SAE 50 is used in the spring and summer. In the fall and winter, if the temperature drops below 20°F, SAE 10 is used. Using the incorrect grade can be costly. Cold starts in equipment using SAE 30 can result in blown transmission seals. Overall, maintenance costs may be higher and productivity lower compared to using multigrade.
-
Multigrade - These oils, which operate properly in all climates, have been available to the public since 1999. A single fluid can span the equipment's entire operation range, eliminating the need to stock two different grades of fluid or change fluid depending on the climate. They offer better efficiency than straight grades over an expanded temperature range. Hydraulics benefit from multigrades as well, from cold starts to high-temperature operations. Because multigrades impose lower parasitic (fluid friction) losses in the transmission, the equipment is able to perform the work using less fuel, thus lowering the cost of operation. Multigrade oils with outstanding shear stability are the wave of the future.
Viscosity is a critical parameter in ensuring proper operability of today's powershift transmissions. Newer transmissions with advanced electronic controls require the low-temperature performance of SAE 10W, while final drive gears need the film thickness of an SAE 30. The film thickness is critical in ensuring adequate gear and bearing life, while low-temperature fluidity is critical for pumpability and optimal shift quality at low temperatures.
Industry Standards for Powershift Transmission Fluids
Unlike engine oils, there are no industry-wide standards for powershift transmission fluids. Instead, performance is OEM driven, and owners and fleet managers must follow the recommendations of their equipment manufacturer, usually in the form of a fluid specification such as Caterpillar TO-4. In addition to the general specifications OEMs also indicate the maintenance intervals, viscosity grade requirements and filter replacement intervals.
What's Next?
Several changes are on the horizon. Tier IV engines, debuting in 2010, will incorporate even tougher emissions control in off-road equipment. The likely result will be increased component temperatures and the consequent need for cooling. Because this new equipment is expected to run hotter, some of the heat will likely impact transmissions. New fluids may need to be developed for increasing temperatures. There may also be a desire to recover efficiency loss from the new Tier IV engines, which is estimated to be about five percent. Lubricants for powershift transmissions may help overcome some efficiency loss.
Developing countries such as China and India are beginning to use high-performance lubricants. This will require increased global availability to meet these new demands. Owners and fleet operators in these countries will need to become familiar with these lubricants and how they can improve the operation and life of their equipment.
No single lubricant solution is available for all off-road equipment applications. With the ever-increasing costs for equipment, lubricants should be carefully chosen to enhance and maximize equipment performance, life and profitability. After all, more power allows the equipment to do more work. Don't forget, it's all about the power.
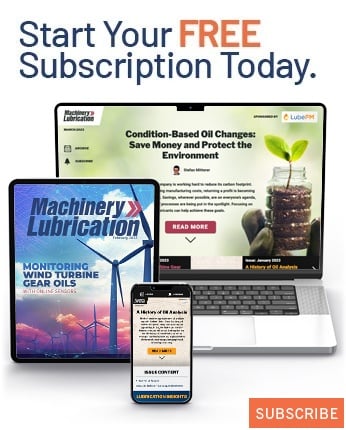