Heat effects are the major cause of failure in mechanical face seals used in pumps, mixers, agitators and wherever a rotating shaft passes through the housing of a machine. Improper design, installation or maintenance of seals can lead to overheating and catastrophic failure of a system, endangering the safety of plant operators and posing an environmental hazard as a result of pollution associated with leakage from seals.
This article covers the effectiveness of steps that can be taken to lower any troublesome seal temperature.
Table 1. Typical Properties for Face Seal Materials6
Elements of Typical Face Seals
Figure 1 illustrates the basic elements of an inside-mounted mechanical face seal, where the primary ring is located inside the machine and rotates with the shaft and the pressure acts externally from the outer diameter to the inner diameter across the seal face. Inside seals are the most common type of single seals because they can withstand high pressures and can accommodate different types of flush plans. The main components consist of a primary ring that rotates with the shaft and the stationary mating ring affixed to the gland. A pusher mechanism (either springs or bellows with associated O-rings) presses against the primary ring to ensure both faces are in contact to avoid leakage. This spring pressure, in addition to the hydraulic force pressing the surfaces against each other, is often called the closing force.
The incoming flush fluid, typically supplied at a flow rate of approximately 1 gpm taken from the process fluid, enters through the inlet port(s) and flows over the rings and in between the faces to create a hydrodynamic pressure as an opening force that promotes separation of the surfaces. Two other elements contribute to this opening force: hydrostatic lift resulting from a fluid pressure difference in the container and ambient, and centrifugal action caused by rotation of the primary ring. As a result, there is a net pressure acting on the surfaces. This is a delicate design parameter. A large closing force tends to cause excessive wear, and a large opening force causes the seal to be susceptible to more leakage.
Table 2. Typical Values for Convective Heat Transfer Coefficient Based on 4-inch seal OD Running at 3,600 rpm1
Seal Face Factors
Materials - When choosing materials, the primary and mating rings are typically selected from dissimilar materials to reduce friction and wear. Also, these primary and mating rings are often selected with materials that have a high modulus of elasticity difference; therefore, the stiffer face can run into the softer one and thereby provide a tighter seal. Another element to consider is the coefficient of friction between the two faces, which is responsible for heat generation and thermal expansion. Table 1 provides useful properties for various seal face materials.6 Typically, the coefficient of friction between the faces is between f = 0.02 and 0.08. The breakaway torque under the dry startup condition is assumed to be three to five times higher.
Flatness and Finish - Most seal faces are lapped and polished to achieve flatness to within two to three helium light bands with a surface finish of four to five µin. Surface finish plays an important role in the film thickness between the seal faces and in the interfacial heat generation.
Temperature - Seal temperature is critical. If it is too high, the face material will crack, blister, heat check and fail. Calculating this temperature involves poorly defined details such as surface roughness profiles and asperity interactions. Example 1 covers the means for estimating the primary factors involved and suggested modifications follow for lowering the temperature for an inside mechanical face seal.
Figure 1. Mechanical Seal
Performance and Thermal Analysis
Example 1 presents simplified routines for evaluating performance factors and their involvement in seal temperature. More detailed analyses are available in the references included in the online version of this article, and seal manufacturers can provide recommendations for seal selection along with operating factors that can be expected in specific applications.
Example 1: The inside mechanical face seal shown in Figure 2 uses a carbon graphite primary ring and tungsten carbide mating ring in a system with P1 = 750 psi water service pressure at 100°F with the shaft rotating at N = 3450 rpm. The rotating primary ring has the following dimensions: Dp = 2.0 in, dp = 1.4 inches, and shaft shoulder diameter B = 1.6. The spring pressure is Psp = 25 psi.
Seal Face Pressure
The seal face pressure can be estimated using the following equation:
where k is the pressure gradient factor, which ranges between 0.5 to 0.8. For water and nonflashing fluids, k = 0.5 and b is the balance ratio defined as the closing area divided by the opening area of the primary element, or as follows:
PV Factor
To determine the pressure-velocity (PV) factor commonly used as a criterion related to power loss, surface temperature increase and wear rate, the mean velocity (Vm) must first be computed.
The PV factor then becomes:
This is above an upper PV limit of 200,000 often used as a guide in applying industrial unbalanced seals.8 Some limiting PV ratings are given for a life of 15,000 hours with specific fluids, seal types and face material combinations. For example, an inside seal using ceramic vs. carbon-graphite faces at 1,750 rpm may have a PV rating of 150,000 psi-ft/min with 150°F water and 205,000 with light hydrocarbon oil. However, these values can range up to and even above a 500,000 limit.
Power Loss
To determine the power loss, the face area must be calculated. The basic area equation is A = ∏r2.
The friction coefficient for carbon graphite-tungsten carbide friction pair is estimated to be f = 0.07. The power loss is:
Flush Rate
Typically for applications involving water as the flush fluid, it is recommended the temperature increase be kept below ∆T = 15°F. The flush flow rate is:
Therefore, only 0.32 gpm should be sufficient for this application. This implies that for the water temperature in the seal chamber to remain around 100°F in the vicinity of the seal rings, the water should be injected into the seal at 92.5°F and exit at 107.5°F, to satisfy the 15°F temperature increase described in Table 2.
Average Face Temperature
To estimate the face temperature, the heat convection coefficient (hconv) must be known; refer to Table 2. Using an expression recommended by Buck1, the face temperature is:
where kp and km are average thermal conductivities of 8.6 and 58 Btu/hr.ft °F from Table 1 for the carbon and tungsten carbide mating rings, respectively. The seal width, w, can be taken as the difference between the OD and ID of the nose primary ring (2.6 to 2.0 inches) divided by two and Dm taken in feet. Tsf represents the temperature of the flush fluid surrounding the rings. Note that this average temperature is below the boiling temperature of water and flashing across the face should not be a concern.
This is a simplified analysis. Seal faces come in a variety of shapes, sizes and configurations. An analysis that uses shape for various seal ring geometries, with partitioning of heat flow between seal rings, has been presented by Luan and Khonsari (full reference included in the online version).
Wear and Seal Life
Some seals last indefinitely while others have only a short life span, therefore little life and wear data is available. When machinery operators encounter early cases of high leakage or other indication of wear, consideration should be made to lower the PV factor at the seal face, use a more wear-resistant material combination and eliminate contamination.
Wear rate generally varies with the PV factor at the seal face in a pattern similar to power loss: the higher the face contact pressure P and surface velocity V, the higher the wear rate. With higher hardness of the seal material, the wear rate is expected to be proportionately less.
Reducing Seal Temperatures
By following specifics for analyzing thermal details, reduction is often possible in seal face temperature with corresponding improvements in reliability, life and efficiency. The following points are certain items to be considered for lowering seal temperature:
-
Reduce face pressure: lower spring closing force to be closer to the hydraulic opening forces.
-
Provide a high modulus of elasticity difference between the primary and mating rings for the stiffer face to run into the softer face to provide a tighter seal.
-
Use a material combination with a lower friction coefficient.
-
Explore a more appropriate flush plan as specified by the American Petroleum Institute in its standard (API 682) for pump sealing systems.
References
G. Buck. “Estimating Heat Generation, Face Temperature and Flush Rate for Mechanical Seals.” Proceedings of Pump Users Expo ’99, p. 167-172.
-
G. Buck. “Materials for Seal Faces.” Pumps and Systems, p. 22-26. 2001.
-
R. Johnson and K. Schoenerr. “Seal Wear.” Wear Control Handbook. M. Peterson and W. Winer (editors). ASME Publication, New York, NY, 1980.
-
M. Khonsari and E. Booser. Bearing Design and Lubrication, 2nd Edition. John Wiley & Son, Inc., New York, NY, 2008.
-
A. Lebeck. Principles and Design of Mechanical Face Seals. John Wiley & Son, Inc., NY, 1991.
-
A. Lebeck. “Dynamic Seals, Tribology Data Handbook. E.R. Booser (editor). CRC Press, Boca Raton, FL, p.734-780. 1997.
-
Z. Luan and M. Khonsari. “Heat Transfer Analysis in Mechanical Seals Using Fin Theory.” IMeChE Journal of Engineering Tribology, Series, J., V. 221, p. 717-725. 2007.
- W. Stair. “Dynamic Seals.” Handbook of Lubrication, Vol. 2. E.R.Booser (editor), CRC Press, Boca Raton, FL, p. 581-622. 1984.
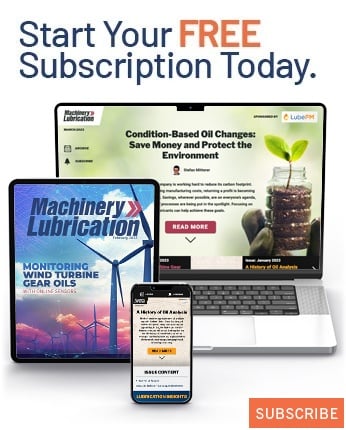