In
a world of fierce competition, individuality and unique ideas bring fresh solutions
to solving age-old industry issues.
Millar Western, a family owned pulp and paper mill, was able to take rising economic prices and capitalize on market conditions by further reducing scheduled maintenance using proactive maintenance strategies.
Introduction
In 1988, Millar Western constructed its first chemi-thermal mechanical pulp
(CTMP) mill in Whitecourt, Alberta, Canada. They completed a sister mill in
1992 at Meadow Lake, Saskatchewan, Canada. Within the Whitecourt plant, there
is a forest products pulp division that uses two state-of-the-art CTMP facilities.
The sister mill at Meadow Lake was the first successful zero-effluent pulp mill
in the world. Both plants produce flash dried chemi-thermal mechanical baled
pulp used in such products as fine finishing paper and opaque cereal bag liners.
From
1988-1994, the Whitecourt Plant had been successfully practicing preventive
maintenance. In 1995, management decided to use increasing pulp prices as a
catalyst to invest in the company’s further growth. The preventive maintenance
program in place at that time consisted of two major shut downs each year in
addition to regular maintenance practices.
This prompted the mechanical
maintenance group and management to re-evaluate their current maintenance practices.
They agreed that the preventive maintenance program had been successful, but
a more aggressive program would help Millar Western remain competitive in the
long run. The group implemented a mill-wide lifestyle change to push the limits
of maintenance into a new realm
of reliability.
Defining
the Goals
Management and maintenance agreed to refocus their efforts on condition monitoring
activities during normal mill operation to uncover those defects or deficiencies
requiring action. Management wanted to reduce downtime and increase production,
thus producing greater profits. Maintenance wanted to take that one step further.
They wanted to have empty storage shelves, meaning they’re functioning
proactively. They wanted to routinely monitor the equipment so when testing
shows something awry, downtime can be scheduled and supplies ordered “just-in-time,”
before failure occurs.
They established six goals for their program (see sidebar). These goals would be reached by implementing vibration analysis and oil analysis.
Predictive
Maintenance Program
The team started with vibration analysis, which proved to be a challenge for
them, from recording the data to learning to interpret the results. Within two
years, the team was able to bring vibration analysis online and merge it into
the computerized maintenance management system (CMMS) they already had in place.
Once
vibration analysis was up and running, the team focused on implementing oil
analysis at the mill. Basic oil testing had been performed on larger, more expensive
equipment since the mill’s opening. Their lube oil supplier primarily provided
elemental spectrography. They also collect Direct Reading (DR) and analytical
ferrography readings when necessary.
In 1996, Millar Western purchased an onsite particle counter along with oil analysis software. The software merged onsite oil analysis data with the data generated by the outside laboratory. And, the software interfaced with the existing CMMS software. This software allowed them to manage the data collected by the tests (regardless of where the sample was collected) and integrate the data into the existing CMMS. Oil sampling routes were consistent with already established vibration routes. According to Mr. Trodd, oil analysis seemed to get in line faster than the complex vibration analysis.
Once the software was in place, it became easier to expand the program to other equipment. Eventually, the new program encompassed all of the mill’s equipment. They drastically reduced turn around test times on spectrography testing by enabling an electronic data transfer of the data directly into the onsite software program. They were also able to import all historical DR and ferrography test data. Initially, ISO codes were not a concern until the actual machine levels were inspected.
Condition-based monitoring
of their machines, which included vibration analysis and “maintenance in
a bottle,” as the team refers to oil analysis, rather than turning wrenches,
has impacted all of the mill management goals. Keeping the technologies simple
at the grass roots level has not only produced a “silent filter” phenomenon
but also has created the birth of the “invisible wrench.” This means
many more people take part in the program because they know the results are
important.
The development of the oil
analysis program has been by far the most proactive maintenance tool introduced
at the plant says Mr. Trodd. Millar Western’s qualified tradesmen responsible
for mill equipment have been involved since the programs inception. Commitment
and hard work have pushed Millar Western to where they
are today.
Action is taken to find and eliminate the root cause of the problem and, if possible, bring the lubricant back to an acceptable operating condition. When high particle counts are detected, area tradesmen use either portable filtration and/or an oil change, depending on the circumstances. Additionally, they can send the abnormal samples out for further testing. If a problem with the oil’s condition is suspected, detailed oil analysis including viscosity, total acid number, elemental spectroscopy and sediment testing are conducted. If component wear is suspect the sample is sent to a lab for ferrography testing.
A survey of the 65 ground floor process pumps revealed ISO cleanliness codes of 18/15 and higher. Also, high levels of water were detected. The team scheduled multiple oil changes in an attempt to eliminate the problem. However, particle levels remained high and more than 50% of the pumps had excessive water contamination.
Because multiple oil changes yielded little benefit, the team decided to deploy portable off-line filtration. This measure significantly reduced particle contamination levels.
The next group of samples on the pumps indicated that only 18% of the machines exceeded the ISO 17/14 target cleanliness level. With the particle contamination problem under control, the team had a clear direction in which to focus; seal-up the power end units to reduce water contamination. Upon further investigation, the team discovered that of the 18% non-conforming results, only 3% were due to high particle count; 15% were due to excessive water contamination. Currently the team is testing a variety of pump sealing combinations to address the water contamination issue on a mill-wide scale.
Once the ground floor was under control they moved through the plant area-by-area cleaning up all the process gearboxes in the same manner, all done during production. Millar Western no longer utilizes any unscheduled down time for oil changes on any of the pumps within the plant, and cleanliness targets of ISO 16/13 are consistently met or exceeded. Throughout the plant, the results are three times cleaner than when the program was initially started. They discovered that once the results reach an ISO code of 14/11 or 15/12 on a pump it normally stays there for very long periods of time, which means the chain of wear generation has been eliminated, or there is “no wear” being generated once you reach a certain level of cleanliness.
Hydraulic systems were one of the last machine groups brought into the program. The filtration standards on new equipment were good and component reliability had also been very good since the mill’s startup. The oil analysis program proved to be most beneficial to the plant in identifying key system component failures, dramatically reducing maintenance costs.
The Results
Presently,
Millar Western monitors 450 sample points, 300 of which are performed on a monthly
basis. If a deviation from an expected trend is reported, then area tradesmen
immediately take corrective action on the machine. Machinery availability goals
are set at greater than 97.5% so there is very little room for error. For example,
in the past if a large hydraulic motor developed a shaft seal leak it was totally
rebuilt at an average cost of $21,000 per event. The goal is to run the component
until it starts to fail then pull it from service for a total rebuild, maximizing
its life cycle, pushing maintenance costs to a point where it is justified to
be spent on the component.
Over the last five years their program has been exceeding goals with staggering results, largely due to advancements in the predictive maintenance program. In five years Millar Western has reduced lubrication costs by 12% or $10,000. During this time, they reduced solid grease consumption from 2000 kg to 1000 kg; and reduced liquid lubricant consumption from 57,000 liters in 1997 to 32,000 liters in 1999 (beating their goal by 2,000 liters).
Perhaps the most significant result of the program is the new level of ownership the tradesman take in achieving machine reliability. They take pride in their work and feel responsible for the equipment. The level of commitment and satisfaction the tradesman have for their job has also had a profound impact on reducing absenteeism.
“Everyday we push the parameters of the program. It sounds scary, but with over 300 years maintenance experience within the group, failures are rare. “Over the last 5 years it has been a treat to be involved with such a group of professionals committed to the predictive maintenance technologies discussed and their continued improvement, plus their mindset on not accepting the ‘norm’ as being acceptable within today’s business of maintenance,” concluded Mr. Trodd.
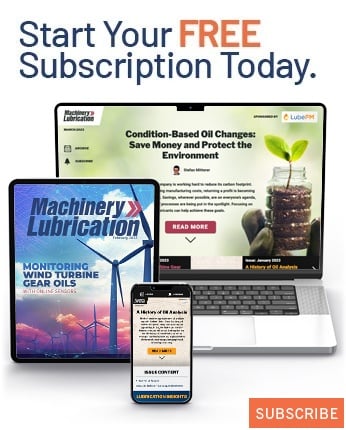