With literally thousands of uses for heat transfer fluids, it is nearly impossible for any heat transfer fluid manufacturer to recommend an exact oil change interval or maintenance schedule. Each application has its own unique characteristics that can contribute to the degradation of a heat transfer fluid, as well as each heat transfer fluid will react differently in different user environments.
To give an example of the extremes, the same heat transfer fluid used in, for example a PVC extruder may have a life cycle as short as a few months while that same fluid in a larger ‘closed’ system can last upward of 10 to 15 years!
To begin, we should understand the two basic ways in which a heat transfer fluid can become degraded.
Oxidative (Most Common in Open Systems)
The scientific definition of oxidative degradation is the reaction of oxygen (in air) with the fluid by a free radical mechanism to form larger molecules which end up as polymers or solids. These thicken the fluid increasing its viscosity. A more viscous fluid will be more difficult to pump, have poorer heat transfer characteristics as well as an increased chance of coke formation. Oxidation is also accompanied by an increase in the acidity (TAN) of the fluid.
As with most chemical reactions, oxidation occurs more rapidly as the temperature is increased. At room temperature, the reaction rate is hardly measurable. However, at elevated temperatures, the affect is exponential and can impact the fluid life in systems not utilizing oxidation-reducing measures such as nitrogen blanketing the expansion tank.
In layman terms, oxidation occurs when hot fluid comes in contact with air. Signs of fluid oxidation are seen most evident as sludge formation within the system especially in low-flow areas such as reservoirs or expansion tanks.
Thermal
Thermal degradation, or thermal cracking, is the breaking of carbon-carbon bonds in the fluid molecules by heat to form smaller fragments which are free radicals. The reaction may either stop at that point, in which case smaller molecules than previously existed are formed, or the fragments may react with each other to form polymeric molecules larger than previously existed in the fluid. In heat transfer terminology, the two types of degradation products are known as "low boilers" and "high boilers".
If thermal degradation occurs at extremely high temperatures, the effect is not only to break carbon-carbon bonds but to separate hydrogen atoms from carbon atoms and form coke. In this case, fouling of the heat transfer surfaces is very rapid and the system will soon cease to operate.
The effect of the low boilers is to decrease the flash point and viscosity of the fluid as well as to increase its vapor pressure. The effect of the high boilers is to increase the viscosity of the fluid as long as they remain in solution. However, once their solubility limit is exceeded, they begin to form solids which can foul the heat transfer surfaces.
In layman terms, thermal degradation is overheating the oil past its boiling point. As the fluid boils, much like water, it produces a lighter component in the form of vapors. Excessive overheating or cracking can cause reduced viscosity as well as pose safety concerns with the creation of the lighter components which in turn reduces the overall flash point, fire point and auto-ignition temperatures.
Now that we understand how a fluid can break down, we can now break heat transfer systems down into two rudimentary types: open and closed.
Open Systems
An open system will have oil coming in contact with air at some point in the system; this may be at the bulk operating temperature or may be at a lower temperature. However, if the oil temperature at which it contacts air is not well below 200 degrees Fahrenheit, this is considered an open system and susceptible to oxidation. These systems tend to be smaller in nature and used in manufacturing processes in the plastic, die cast and other industries that utilize portable type electrically heated “oil heaters”.
Closed Systems
A closed system will have an inert gas buffer (usually nitrogen) between any point of contact of the oil to the atmosphere. These systems are typically larger in nature and will generally be heated by a gas or oil fueled boiler. This inert buffer will generally eliminate most of the concern for oxidation. Please note, some boiler manufacturers have developed expansion tanks that through proprietary plumbing effectively eliminate hot oil from coming in contact with the atmosphere. For all intents and purposes, these can also be considered closed loop.
Now let’s discuss the maintenance aspect of heat transfer fluids.
Closed Systems
As noted above, most closed systems if operated properly should not have a major concern for fluid degradation. Typically, the systems are not run above the recommended bulk or skin temperature of the fluid, nor is oxidation of great concern due to the use of an inert gas blanket. However, due to factors beyond one’s control such as power or pump failure or inadvertent changes to a system (partially open or closed valves, decommissioning user loops, etc.), these systems can experience thermal degradation, often unknown to the user on a day-to-day basis.
The first order of maintenance for any system is to consult your fluid vendor and equipment manufacturer before making any changes to your system. A proper system is engineered around the user’s needs and fluid. While most fluids are in the same range with respect to physical properties, changes in a system design or function can negatively impact a fluid.
The second order of maintenance is to follow a recommended fluid analysis program (usually available complimentary or for a nominal fee from your vendor). These analyses allow early detection of any changes to a fluid allowing time for system corrections (to stop the fluid degradation) and often improve the fluids condition.
Fluid changing in closed loop systems is usually infrequent and measured in years. However, there will be a time when changing a systems fluid will be required. This can often involve multiple steps including, in some, cases the use of a cleaning fluid and or flushing fluid. It is always best to understand the condition of your fluid and system prior to changing fluids (either to a different fluid or the same fluid). A fluid analysis is critical at this point as is a general inspection of the system itself, looking for leaks and, if possible, inspecting the inside of the pipes and boiler.
Changing a fluid requires multiple considerations and is best discussed with your fluid vendor prior to change. However, the most important step is the complete (at least 95 percent) removal of all traces of the previous fluid. Degraded fluid will quickly contaminate new fluid!
Open Systems
Open systems tend to run at temperatures well below the maximum recommended bulk temperature of a fluid (usually under 600 F [315 degrees Celsius]). While this usually eliminates the potential for thermal breakdown, open systems are still most susceptible to oxidation.
Severe oxidation can, in extreme situations, shorten a fluid life to a number of hours. It is crucial to understand your system’s design and how it incorporates protection from oxidation. Often, equipment manufacturers use heat exchangers to cool oil prior to its exposure to air, or bypass valves set on timers to help venting at start up but close to reduce oxidation levels after a desired temperature is reached. If these systems fail to operate properly the oil life can, and most likely will, be shortened.
As a fluid oxidizes, it forms an acid. These acids, while generally not at corrosive levels, can build and eventually polymerize (drop out) of the fluid in the form of heavy, grease like sludges. Again, fluid analysis is your best maintenance tool. When first using a heat transfer fluid in an open system, fluids should be monitored regularly to understand how often a particular system requires fluid changes. While manufacturers of equipment can provide guidelines as to the life expectancy of a fluid not all fluids are made equal. Simple differences in operating environments and temperatures can impact oil life. The only way to know how often your fluid should be changed is through analysis.
Once you establish a maintenance schedule, it is important to understand how to efficiently and effectively remove all the spent fluid prior to refilling. A fluid that has degraded contains an acidic compound that when left to mix with new fluid will increase the rate of degradation.
Smaller open-type equipment contain numerous areas where fluid can become trapped. Areas like heat exchangers, filter housings, horizontal piping etc should be examined for residual fluid. Often times, blowing air or nitrogen through lines will help remove old oil. If this is not possible, most fluid manufacturers have a light, economical flushing agent that can be used to flush out residual fluid.
Maintaining your fluid change-out schedule will keep equipment clean and running at peak efficiency. Neglecting maintenance schedules can be problematic and can ultimately cause complete failure.
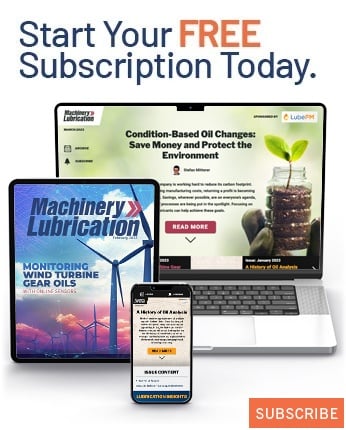