OK, it’s official. We’re in a recession. In reality, we’ve learned that this recession started in December 2007, but the meltdown of the financial markets transformed the recession into what appears to be a full-scale economic train wreck. Nobody seems to know how bad things will get or when we might start to pull out. Unfortunately, the manufacturing sector is being hit very hard. Automotive sales are down 30 to 40 percent for most manufacturers. Even Toyota, the gold standard for lean and our shining star for excellence in manufacturing, is taking a beating, with sales down more than 30 percent vs. a year ago. So, how do we survive? More to the point, how does lean plant reliability management survive?
Most senior managers think that reliability – of which machinery lubrication excellence is an important component – is only valuable when the plant is capacity constrained or in a sold-out position, where having that extra hour of availability gives us the opportunity to make even more profit. No, no, no, no! By the way, did I say no? Lean reliability is not just about maximizing manufacturing system availability. That is the wrong way of thinking. Lean reliability, executed properly, enables you to maximize the profitability of every second of manufacturing time.
It is common for plants to get fat when they possess excess capacity. So what, the line broke down, we’ll just work an extra 15 minutes at the end of the shift to make up production, or schedule one Saturday shift to get caught up. That kind of thinking is the fast track to high-cost-producer status in your industry, which by the way, is the plant or company that closes when the economy recedes. Lean thinking requires that you focus on meeting customer demand while utilizing the fewest manufacturing hours and the least resources possible. Everything else held equal, that approach to business makes you the low-cost producer for your industry, making you the least vulnerable to consolidation and/or closure. So, even at the per widget cost level, you can’t be lean without reliable manufacturing processes. Arguably, reliability is more important when you’re not sold out – when it may become a matter of survival.
In these tough times, managers make some pretty predictable and difficult decisions. These typically include the following:
-
Cut non-critical expenses, like travel, company-sponsored BBQs, etc.
-
Eliminate shifts so as to scale production to meet demand.
-
Arbitrarily cut maintenance costs.
-
Cut or reduce training and education expenses.
OK, I can get on board with items one and two. I hate the fact that cutting shifts reduces return on net assets (RONA), but hey, if our customers don’t want to buy it, we’ll just have to inventory the production we can’t sell. That doesn’t make any sense.
I have some real problems with items three and four. Arbitrary cuts in maintenance are real killers. Forgoing or putting off preventive maintenance activities, not responding to condition-based maintenance activities in a timely fashion, discontinuing or reducing condition monitoring tasks, etc. – these moves to arbitrarily cut maintenance costs, unfortunately, create a reliability cycle of despair.
Let me explain. When things get tough, we cut maintenance costs. We typically don’t feel the effects of these cuts in terms of reduced reliability for 12 to 24 months. Most recessions last for between six and 16 months. So, just when we pull out of the recession, we start to gear up for increased production and, you guessed it, we start to feel the effects of our maintenance cuts in the form of reduced reliability. It usually takes 12 months of reaction to live through that process. When management decides to invest in better maintenance to improve reliability – effectively recreating what it had dissembled two to three years earlier – you’d be surprised how much “corporate amnesia” can occur. Two to four years later, the organization is back where it was before. From the start of the recession to the point at which the reliability management systems are recreated, five to seven years has transpired. Yes, you guessed it – reliability is restored just in time for the next recession! The process starts over.
The root cause of the problem is the mind-set. Management thinks it’s OK to cut maintenance because during the recessionary period, we aren’t sold out – so reliability isn’t important. No, no, no, no! Again, your reliability management system should enable you to produce your widgets at the lowest per item cost possible and deliver the availability during those times when your production is sold out. It has been well researched that organizations with the best equipment asset reliability have the lowest maintenance costs.
The Aberdeen Group conducted a benchmark in 2006 and found that the lower quartile performers on equipment asset reliability spent 55 percent more on maintenance as a percentage of sales than the top performers. Reliability is not about spending more on maintenance. Conversely, it is about spending less but getting more capacity. Make your managers aware of this relationship. Make them aware of the Aberdeen study. Don’t stand still and let the reliability management system you’ve worked so hard to assemble get minced and shredded in the wake of short-term cuts – not without a fight anyway. Or, if you’ve not been able to get management to see the value of deploying a reliability management system, use the recession as a tool to show them a proactive way in which to reduce your manufacturing costs.
As for training cuts, I hate that, too. However, they are frequently tied to cutbacks in travel. We need to keep our people educated and trained. In these tough times, look for training options that don’t incur a lot of expense. Online training, DVDs and other forms of remote training are getting better all the time, and it is getting much easier to access these tools. Avoid skill degradation, which is one of the reasons it takes so long to recreate a reliability management system.
This recession is projected to be a tough one. To survive it without suffering permanent damage, we need to be strategizing now. Your reliability management system can help you survive, but only if it doesn’t become an unfortunate casualty.
If you’d like a copy of the Aberdeen Group’s benchmark study, please e-mail me and I’ll get you a copy. Or, if you’d like some help in making your management team understand why good asset managers are low-cost producers, I’d be happy to participate in a conference call to lend a helping hand. E-mail me to set up the call.
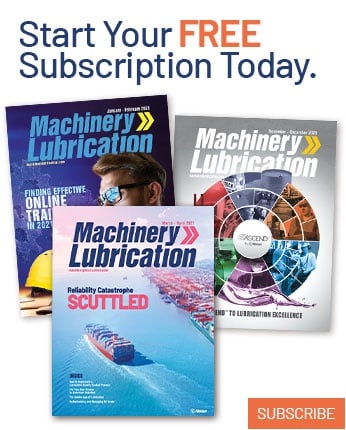