Many organizations have been profiling the role of project manager in the same way for many years with little success. Traditionally, the individual who knew the most about the subject matter, the process or the technology being applied was erroneously selected as the project manager. At best, this method would yield marginal results for project success. Project success is typically defined by a project manager’s ability to effectively manage the triple constraint – that is to say, managing a project to scope, within set time and cost parameters, with the notion to deliver a quality product or result. Highly technical and complex reliability projects often require a level of subject matter expertise not found in your typical project management office. Conversely, many individuals who possess highly technical or complex subject matter expertise may not necessarily possess the skills necessary to manage a project to success.
Engineering projects such as reliability and lubrication projects can be very difficult to profile for a project manager. Unlike large construction or software development projects, reliability and lubrication projects are much smaller. These projects will typically have a shorter duration, involve fewer functional groups or services, and likely require less effort days than their large-project counterparts. Inevitably, this means that the project manager will have fewer subject matter experts to rely on for technical expertise. Therefore, project managers of these highly technical, though relatively small, engineering projects must be able to essentially do more with less.
In addition to being able to manage a project to scope, within set time and cost parameters and deliver a quality product, engineering project managers must be able to excel in other areas as well. Critical thinking, the cognitive process used to analyze and evaluate information to make decisions, is a key skill that engineering project managers must possess. Often, in highly technical reliability and lubrication projects, direction for future tasks comes from the results of a previous task or work package. For example, reliability groups often use a technique called failure modes and effects analysis (FMEA) to help identify and rank chronic failures on industrial equipment. The identification and rank will then lead to addressing the root cause of the individual failure mode. Addressing the failure root cause will often lead to equipment modifications or redesign.
Along with critical thinking, these highly technical and complex engineering projects often require the project manager to use their integrative thinking skills. Roger Martin coined the term “integrative thinking” in his book, “The Opposable Mind”.
Martin describes integrative thinking as: “the ability to constructively face the tensions of opposing models, and instead of choosing one at the expense of the other, generating a creative resolution of the tension in the form of a new model that contains elements of the individual models, but is superior to each.”
This statement always makes me consider the age-old struggle between maintenance and production. Production departments want unlimited access to their equipment to produce products, and they want the equipment to be reliable and consistent. Maintenance departments, on the other hand, require periodic access to the equipment in an offline state to be able to maintain and service it. Here we have two opposing models, where traditionally the approach is an either/or solution. Integrative thinking would offer a much different solution. Martin suggests: “Integrative thinking shows us a way past the binary limits of either/or. It shows us that there’s a way to integrate the advantages of one solution without cancelling out the advantages of an alternative solution.”
Martin goes on to explain that we all possess an opposable mind capable of integrative thinking. Although we may all possess an opposable mind, the opposable mind requires cultivation and practice for the individual to be an effective integrative thinker. Those who have mastered integrative thinking have a distinct advantage. Says Martin: “In this information-saturated age, where each new bit of data complicates a picture that is already staggeringly complex, integrative thinking may be a necessity if we are to find our way past the multiple binds in which we find ourselves.”
Consider again the production vs. maintenance dilemma. Production is responsible for getting product out the door. But if the equipment is unreliable, product cannot be made. This situation is all too common, and the result is that equipment is ill-maintained and often run to failure to satisfy the needs of production. In such a global economy, it seems the only advantage one manufacturer has over another is how reliable that company’s production equipment is and how this reliability relates to its throughput.
Now contemplate a facility that has all the benefits of reliable equipment and 24/7 production. If the facility in question has systematically determined the appropriate lubrication (type, interval and quantity) and contamination control (exclusion, control and removal) requirements and hardware modifications to support these requirements for each asset, it has effectively used integrative thinking to find a way to integrate the needs of both production and maintenance.
Systematic determination of reliability requirements for each piece of equipment will lead to modifying the equipment for maintainability and reliability, allowing maintenance to do most of its proactive maintenance work while the equipment is online producing products. A project manager needs to be able to use integrative thinking to ensure these highly technical and complex are successful.
There is no easy way to profile and select a project manager for your reliability project. Reliability projects can cover a vast landscape of technologies, concepts and strategies. The project manager for any initiative in reliability needs to possess not only critical and integrative thinking skills to find unique and superior solutions to the either/or dilemma, but they also need to have the soft skills required to manage people.
In addition to these specialized skills, the project manager most certainly needs to possess some subject matter expertise and be able to rally the team and motivate them to success.
References:
1. Roger Martin, “The Opposable Mind”, Harvard Business School Press, 2007
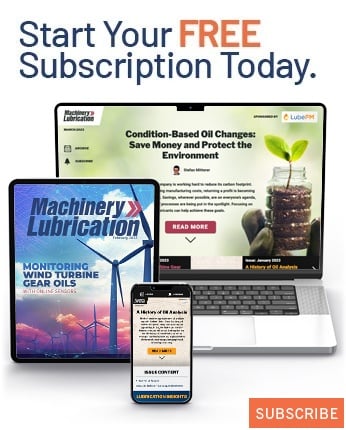