Most reliability deployment systems are heavily focused on equipment-related problems. Indeed, this is because most of these initiatives are driven by the maintenance organization. However, in my experience as a consultant and through inquiries I’ve made to the readers of Reliable Plant magazine, I’ve found that typically only 20 to 30 percent of our reliability losses can be directly attributed to equipment problems. Other problems account for the rest. Among the most significant contributors to reliability loss is disruption of the supply chain.
Supply chain problems can wreak havoc on the reliability of your manufacturing system, leading to several significant losses, including the following:
-
Loss of sales when the organization is sold out
-
Late or non-delivery penalty failures (e.g. customer penalties, demerge, etc.)
-
Warranty costs associated with materials defects
-
Marketing costs to replace customers
-
Brand value/market reputation erosion costs
-
Forced suboptimal product mix, which fails to maximize profits
Start With the Numbers
In a 10-year study at the Georgia Institute of Technology, researchers concluded that supply chain disruptions account for a 31 percent decrease in profits, a 1.2 percent decrease in sales and a 1.7 percent increase in costs. Wow! That gets your attention. Imagine recasting a firm’s income statement with an additional 31 percent increase in bottom-line performance. Recovering these losses can profoundly affect an organization’s share price and competitive position in the marketplace. So, what goes wrong?
The effect of supply chain disruptions increases as the variability of offerings decreases (Figure 1). Plants that produce a wide variety of offerings can deal more effectively with supply chain disruptions by producing alternate products. However, this comes at a cost. Reactive changeups to the production schedule, producing a suboptimal product mix and increasing finished goods inventories of replacement products carry costs that erode profits. Supply chain disruptions can be grouped into two broad categories – raw material delivery failure and substandard quality of raw materials, which I will discuss in more detail.
Raw Material Delivery Failure
Let’s deal with the simple one first. Raw material delivery failure is pretty straightforward. In the interest of lean business management, organizations strive to achieve just-in-time inventory management to drive out costs. This makes sense as most organizations attach a 22 percent annualized inventory-carrying cost (give or take a few percentage points). This accounts for the cost of capital, the cost of storage space, handling costs, spoilage losses, obsoletion losses, pilferage losses, etc. So, the idea of reducing inventory is a good one – so long as the distribution system is reliable.
If the raw materials distribution system isn’t reliable, the cost savings associated with reducing inventory can produce a false economy.
If the savings resulting from reduced inventory fail to offset the production reliability losses caused by eliminating the buffer inventory, we need to rethink the strategy and optimize inventory levels accordingly.
Clearly, we’d like to achieve JIT inventory; but if we can’t achieve sufficient distribution reliability, we need to remind ourselves that the true objective is to maximize return on net assets (RONA), assuming a real and objective evaluation of the reliability of our distribution system.
I suggest that you collect data and “dollarize” the effects of stockouts and economically compare the benefits of inventory reduction to the costs of production losses associated with reducing inventory. We need to optimize inventory levels to maximize RONA (Figure 1). Clearly, if we can increase supply chain dependability, we have the opportunity to reduce the optimal inventory level and drive RONA even higher.
Substandard Supply Chain Quality
Less obvious and harder to define is the effect of substandard supply chain quality. W. Edwards Deming, the father of quality and one of the primary forbearers of what we now call lean business management, taught us that quality and reliability are a function of our ability to control variability in our manufacturing processes. Variability in the quality of the supply chain affects all aspects of overall business effectiveness (OBE) – availability, yield (speed) and quality. Its effect on quality is obvious: The product is only as good as the sum of the parts. Substandard material and parts increase the defect and rework rate, which clearly increases production and warranty costs, leading to reduced profits. Less obvious is the effect that poor supply chain quality has on availability and yield. Variable supply chain quality can cause the following problems:
Startup and changeover delays: When there is variability in the supply chain, it becomes necessary to tweak the setup for a startup or changeover. One of the key aspects of the quick changeover – single minute exchange of dies (SMED) in lean lingo – is that the setup activities are, as much as possible, converted to external tasks, which can be completed as prep work. The more variables the operator has to account for, the harder it is to externalize the setup with fixed settings. Naturally, when startup and changeover activities are more variable and less suitable for externalization, it takes more time, producing availability losses.
Startup and changeover stabilization problems: In addition to delays in completing the startup or changeover of a manufacturing system, material variability in the supply chain increases the time it takes for the production line to stabilize. In reality, the changeover is not officially complete until the production line is producing quality product at specified yield (speed) rates. When the material supply is variable, production stabilization losses increase. Moreover, operators are forced to adjust settings on the fly. Unfortunately, adjustments intended to fix an apparent problem often wind up creating problems in another part of the process. The compounding effect of multiple adjustments leads to availability losses due to stoppages, yield (speed) losses when the line must be slowed down to achieve stability and, in some cases, the need to shut down and reinitiate the startup or changeover process.
Minor stoppages: In some manufacturing processes, variability of the material feed creates stoppages due to binding and jamming. For example, in a bottling operation, dimensional variability in the bottle supply can cause jamming, which temporarily stops the line until the blockage is cleared. In rolling applications (e.g. paper, fabrics, etc.), variability in thickness or tensile strength of the rolled materials can lead to jamming and/or breaks, again producing unavailability. Often, the disruptions are minor and fly under the radar screen. Cumulatively, however, the effect on profits can be quite significant.
Yield (speed) derating: When the input material is variable, production managers are often forced to operate at speeds below the best demonstrated rate. The reason is simple: The machines can’t run without availability disruptions when the setup is based upon the 50th percentile for materials. The speed rate must be adjusted assuming the fifth or 10th percentile.
Root of the Problems
Several organizational business processes lay at the root of these problems, which in turn lead to OBE losses in quality, availability and yield. These include:
Engineering-induced losses: Suppliers deliver goods according to the specifications defined by product engineers. Occasionally, product engineers fail to provide adequate specificity with respect to dimensional tolerances. Moreover, product engineers frequently fail to consider the sensitivity of the manufacturing systems or their flexibility with respect to setup. Conversely, manufacturing process and equipment engineers occasionally fail to consider the degree to which the variability of supplied materials can be controlled. When the equipment is designed with unrealistic assumptions about the dimensional variability of input materials, problems in the plant are inevitable.
Procurement-induced losses: Procurement specialists are encouraged and rewarded to save the organization money by reducing raw materials costs. In doing so, they can unknowingly create production problems in the plant. With the best of intentions, contracts for materials are awarded to the low bidder, which can result in the de facto acceptance of increased material variability that leads to availability, yield and/or quality losses. Likewise, when materials are supplied by a number of different providers, small variations occur. While each supplier may deliver materials that are “in spec”, the small variations increase the number of setup variables that the operations team must control. Also, dissatisfaction and frustration with the quality of supply consumes management time and can lead to frequent supplier changes, further compounding the problem.
Supplier variability-induced losses: In some instances, suppliers fail to effectively control the variability in their respective processes. We need to provide clear evidence in the form of collected process failure data to enable effective communication with suppliers. Proactive communication helps them understand how material variability is affecting the reliability of our manufacturing processes. By putting our heads together, we can arrive at modifications to their process and ours that will stabilize our production processes.
Make it a Priority
Yes, we need to continue to pay attention to equipment reliability issues in the plant. But, we can’t lose sight of the fact that many factors influence the overall reliability of our manufacturing processes. Managing the dependability and quality of our supply chain must be high on our list of priorities.
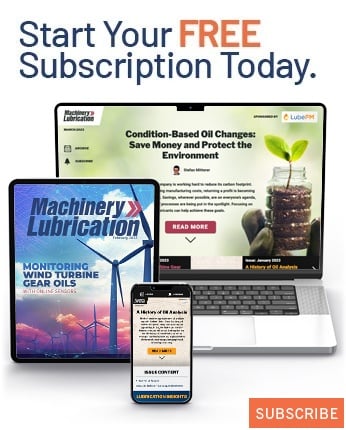