This isn’t Metropolis, nor is it Gotham City. Tomahawk is about as unlikely a setting as you could find for a supervillain/superhero showdown. Nestled in the northern woods of Wisconsin, a four-hour drive from Milwaukee, this hamlet’s skyline is an amalgam of fishing shacks and supper clubs, not skyscrapers and concrete jungles. Stone gargoyles aren’t the gothic overseers of this town. You will, though, find an 18-foot-tall moose statue.
In Tomahawk, an epic battle of evil vs. good takes place each day at Packaging Corporation of America’s corrugated medium mill. It’s about possession of the heart and soul of this plant – thousands of mechanical assets that churn out nearly three million pounds of high-value product every 24 hours.
On one side, there are the sinister forces of contamination – water, steam, chemicals, coal dust, dirt, wood pulp and chips, and paper stock residue. More than five million gallons of water alone come in contact with the process equipment on a daily basis. These fiends are bent on infiltrating oil and grease and poisoning this lubricating lifeblood of plant equipment. They seek to pry their way into bearings and gears in order to gouge and strip such components into pricey submission.
On the other side, there are mortals who stand up for what is right and good ... for the machines and for PCA. Area lubricators and an oil analyst are among the members of this Justice League (which also includes maintenance, production and corporate management, as well as technicians and operators). Using high-tech tools, innovative products and all-important know-how, they repel the onslaught with voracity and deliver a filtration-based fat lip for good measure.
You’ve heard of Superman, Batman, Spiderman, et al. Well, get to know The First Line of Defense and The Investigator.
The First Line of Defense
Involving production-based employees in machinery lubrication tasks has long been a staple of the PCA mill in Wisconsin. Traditionally, the role of “oiler” was more mild-mannered than superhero. According to mill worker Craig Madlung, “This was a second- or third-tier task. You filled oil jugs a couple of times per day and poured oil in machines when the bearings got hot.”
In recent years, lubrication management has evolved into a high-profile, high-priority position. Today, seven “area lubricators” spend 100 percent of their work week instilling and enforcing acknowledged best practices that enable high levels of reliability, productivity and profitability.
“The area lubricators do not run the equipment,” explains Craig Slonski, the mill’s superintendent of maintenance reliability. “They make sure that proper lubrication is taking place. They make rounds on a daily, weekly or monthly basis based on the criticality of the equipment. They check the oil levels and adjust as needed, grease and oil, take samples, change air breathers, change filters on offline filtering equipment. They clean. They take temperatures. They make sure that equipment is running as expected. They are the hands, eyes and ears of what is going on with those pieces of equipment.”
Batman has Robin. So does The First Line of Defense. In the latter case, it is Robin Gray, the PCA mill’s veteran lubricant analyst.
Maintenance reliability supervisor Keith Weizenicker puts it a simpler way: “These guys are the first line of defense.”
The First Line of Defense consists of:
- Madlung, a 24-year PCA veteran who has 19 years of experience in lubrication roles
- Tim Symonds, a 33-year veteran with 15 years of lubrication experience
- Phil Dahl, a 25-year vet with 12 years of lubrication experience
- Brad Gaedtke, a 25-year vet with two years of lubrication experience
- Larry Dirkx, a 43-year vet with 30 years of lubrication experience
- Dennis Thompson, a 36-year vet with 28 years of lubrication experience
- Michael Fleming, a 31-year vet with 15 years of lubrication experience
Foes aim to avert the heightened senses of these seven linemen.
“Every day, these guys touch the equipment, feel it, smell it,” says Weizenicker. “If we relied purely on the vibration analysts coming around once a month, potential issues could fall through the cracks and eventually become big problems. But these guys are there every day. Those basic care routes and oil routes give you a heads up.”
Each area lubricator works the day shift (from 6:30 a.m. to 2:30 p.m.) and covers a specific, mission-critical area of the plant: the No. 4 papermaking line, the No. 2 papermaking line, the powerhouse, the wood room, the semi-chemical cooking line and the mobile equipment shop.
“From a technical standpoint, they report to maintenance. But on a daily, organization chart basis, they report to production,” says Weizenicker. “They kind of have two supervisors.”
More or less.
“We could have five bosses or zero; it’s all in how you look at it,” says Gaedtke. “We have a lot of autonomy to decide what to do and how to do it. It comes down to accountability and responsibility, which are part of the culture here.”
An enormous roll of corrugated medium engulfs a production area.
Maintenance leadership at the mill includes project engineer Mark Micke (left), maintenance reliability supervisor Keith Weizenicker (center) and superintendent of maintenance reliability Craig Slonski.
Mighty Might offline filtration units are found throughout the mill.
Autonomy is also the result of knowledge. PCA’s lubrication program is currently based on best practices defined by Noria Corporation and sanctioned by the International Council for Machinery Lubrication (ICML). Since January 2005, Noria (with instructors such as Jim Fitch, Drew Troyer and Jeremy Wright) has provided 20 days of on-site training to a host of PCA employees, including the seven area lubricators and each of their seven back-ups.
Slonski states: “We needed to understand what good lubrication practices were in greater detail rather than ‘here’s an oil can, now go do it.’ Even though we had some educational opportunities at the local technical college, we needed much more than that. We had to fill the gap. What else is out there? Noria was out there.”
Mill leaders weren’t looking for attendance from the students. They were looking for absorption and application of the training.
“Having the right people with the right educational background is a key,” says Slonski. “We want people who have a drive and passion for this. That drive and passion is shown by taking these classes and passing and understanding and demonstrating.”
“Passing” is exemplified in the fact that 15 employees at the Tomahawk mill have gone on to obtain 19 certifications through ICML. For example, Gaedtke holds Machine Lubrication Technician (MLT) Level I and Level II certificates and is in the process of pursuing a Machine Lubricant Analyst (MLA) certification.
“Understanding and demonstrating” is shown in how area lubricators have applied the teachings.
Gaedtke says, “All of these concepts are introduced in the classes. You see how you can prevent all of this stuff (contamination, water ingress, etc.). Our company has been very supportive in putting this into action. ‘If it is not being done, do it.’ When you have someone saying, ‘Go ahead and do it’, that makes the job easier and more fun.”
Among first steps, area lubricators eliminated milk jugs and makeshift lubricant transfer containers and purchased sealable and reusable containers specially designed for such tasks. Clean, single-use paper funnels replaced metal funnels. Quick-connect couplers were installed on gearboxes and hydraulic units to make it easy to add or drain oil and to enable filtration for contaminants.
Individual projects developed with time. For instance, Dahl has made it his personal mission over the past two years to find and fix every oil leak in his area.
“Where you have a ton of water, you normally can’t see the leaks. You could walk around for a day looking for the leaking oil and not find it,” he says. “But we purchased a five-gallon bucket of leak-detection dye. As soon as you dump that dye in, you can see the leaks. We used to go through a lot of oil because of the leaks. We still go through oil, but not anywhere like we previously did.”
Company: Packaging Corporation of America, a manufacturer of containerboard and corrugated packaging. It has four production mills and 68 converting operations. PCA has annual sales exceeding $2 billion and more than 8,000 employees.
An Arsenal of Weapons
Batman has a cache of crime-fighting gadgets at his disposal, both on his utility belt and in his cave. Iron Man has a high-tech suit that can produce rays, beams, pulse bolts and a defensive energy shield. Every superhero has something. Therefore, it’s no surprise that The First Line of Defense is armed to the hilt for the fight against contamination.
The Tomahawk mill has invested heavily in Mighty Might offline filtration (OLF) units produced by Norman Filter Company. These compact filtration systems transfer and filter water and particle contaminants out of hydraulic, lube and gear oils. The dual-head design of these units enables operation in two stages: the first removes water, the second removes particulate matter. Oils are filtered at a steady flow rate of four gallons per minute to achieve purification down to 3 microns absolute.
“We probably have 100 Mighty Mights,” says Gaedtke. “In-house oil analysis shows you have some dirt or water or metals in a gearbox. I go through, attach a Mighty Might to the quick-connect coupler, and in a matter of seconds, I have an offline filter system on it.”
PCA believes the OLFs are a step above single-pass filtration systems.
“You won’t reach your ISO targets with single-pass, so you end up changing the oil,” says Weizenicker. “If you change the oil, you are going to get 50 percent of the dirt; the other 50 percent is still stuck at the bottom of the box. With the offline filters, you clean it up. You get those multiple passes through there. You clean the whole box, top to bottom. The oil is now good. It might run another two or three years doing it this way. There is no sense in dumping a 30-gallon gearbox. If it’s dirty, clean it up. It’s two years old, so what? A couple of filters and you are good to go.”
OLF are one reason why the Tomahawk mill has reduced its oil usage 28 percent since 1997 (18,300 gallons vs. 13,200 gallons in 2009).
Area lubricators also bring together multiple tools to vanquish contamination.
They combine a Mighty Might with a desiccant breather kit from Y2K Fluid Power to pre-filter oil drums in lube storage areas. And, they marry an oil heating element to an OLF on filter carts to polish cold oil.
“Cold oil doesn’t clean very well,” says Weizenicker. “So, we took an oil heating element and put it into a tube. We put an offline filter system with it so the oil comes out of the unit, gets heated, goes back in and sits there and flushes. You have 140- to 150-degree oil going through this cavity rather than just cold oil. That gets much more dirt and junk out.”
PCA also wards off water ingress through the use of Inpro/Seal bearing isolators and air seals.
Bearing isolators are non-contact, permanent bearing protection devices that consist of a rotor and a stator. The rotor turns with a rotating shaft while the stator is pressed into a bearing housing. The two components interact to keep contamination out of the bearing enclosure and lubricant in.
“With the air seals, we add 3 cubic feet per minute of air and it pressurizes the gearbox so no water gets in,” says Madlung. “We used to run 1,000 parts per million of water in some of our gearboxes. We used to change that oil out every year. Since putting the air seals on and attaching a filtration system, we change the oil out now once every five years and the water level is consistently below 50 ppm.”
The PCA mill in Tomahawk, Wis., is succeeding because of the health and performance of its production equipment. That is a direct result of the work being done by the plant’s maintenance and production employees. And, that is a direct result of the support given by upper management at the corporation.
Management supports predictive and preventive maintenance projects, both verbally and monetarily. Corporate management regularly visits the Wisconsin mill’s vibration analysis office and oil analysis lab.
“They are a huge supporter of what we are doing,” says maintenance reliability supervisor Keith Weizenicker. “They come to discuss what we do and how we do it. We are fortunate to have people at all levels of our company that understand reliability and what you need to get to the point where you run 56 days without a breakdown. That may be where this company is a little different than other companies.”
The difference is evident in the capital budget set aside for reliability projects at Tomahawk.
“With a capital budget, we don’t have to beg, borrow and barter to get what we need,” says superintendent of maintenance reliability Craig Slonski. “We just need to make decisions on how best to use that budget.”
Such support isn’t lost on mill workers.
“Management has said, ‘These guys are going to save us lots of money. Let’s give them the tools with which to work,’” says area lubricator Brad Gaedtke. “As a result, there is nothing we can’t do and there’s nothing that can’t be improved.”
The Investigator
Batman has Robin. So does The First Line of Defense. In the latter case, it is Robin Gray, the PCA mill’s lubricant analyst. This Robin is no learning-to-fly superhero-in-training. Gray has worked at the plant for 34 years, including 23 years as a lubrication technician. He has spent the past eight as the main sampler and lone analyst of new and in-service lubricants.
“On average, I spend half of my day on the plant floor,” says Gray, who has MLA II and MLT I certifications through ICML, and has received tribology (levels I and II) training through CSI/Emerson and ferrography training through Predict. “I get involved with lubrication-related projects with the area lubricators and the maintenance department. I spearheaded many of the dedicated offline systems. I have to wear a lot of hats.”
The one Gray enjoys most is his inspector hat. Over the course of a five-week interval, he takes close to 300 samples. He then returns to the mill’s oil analysis laboratory and becomes The Investigator.
“I love to investigate things and see what is creating problems,” he says.
Gray has a host of tools at his disposal – a computer, microscopes, beakers and graduated cylinders, a Karl Fischer moisture analyzer, an ultrasonic bath cleaner, scales, a mechanical separator/screener. But his favorite device is the lab’s 5200 Trivector Analyzer from CSI/Emerson.
“It does a comparative analysis on new oil out of the barrel and the used oil that we extract from a piece of equipment,” says Gray. “It tests to determine if the oil is still intact and clean. It tells you what degree of contamination is in there. The first test picks up metals. The second test measures water content. The third test is a laser counter which counts particulate down to a 2-micron level.”
Gray analyzes more than fluids. He frequently performs a postmortem examination on oil filters.
“If you suspect something, you take Robin a filter,” says Gaedtke. “He cuts the pleats apart and sees what is going on inside. Using the tools in his lab, he can identify if there is wear debris and, if so, what type of metal it is – brass, steel.”
The Investigator recounts an ongoing filter case.
“We have a situation in the boiler house right now,” he says. “The oil light on an OLF was changing. Something had altered it. So, I cut the pleats of a used filter apart to see what was in the oil. Something in the system has changed. There are some indicators. My job is to find out the equipment issue or issues and why this is occurring. If I can’t find the answers here, I will talk to the equipment manufacturer and the oil vendor. It’s a crime scene investigation going on.”
Saving the day is a tough job, but someone’s got to do it.
“You have to love this stuff,” he says. “It has to be in your blood.”
Swampy on the Outside, Clean on the Inside: How PCA Defeats the Goo Monster on Paper Machine No. 4
The environment in the Packaging Corporation of America plant in Tomahawk, Wis., is tough on equipment. With the presence of raw material residue and 5.5 million gallons of water flowing through plant processes on a daily basis, conditions can get downright swampy. What follows is maintenance reliability leader Craig Slonski’s observations on the two plant-floor snapshots in this sidebar.
Maintenance (especially lubrication) can be a challenge in an environment like this.
Showing Off Super Speed
Look, up in the sky! It’s a bird. It’s a plane. No, it’s the maintenance and production metrics at the Tomahawk mill. Thanks to The First Line of Defense, The Investigator and the rest of the Justice League, contamination doesn’t conquer. Chaos is getting KO’d. Check out the comments by the good guys.
“We are running faster than ever, longer than ever. We are running speeds that were unheard of in the past,” says Gray.
“I have a machine that is designed to run 500 feet per minute, and it’s averaging 1,600 feet per minute,” says Madlung.
“We have pushed oil life in some machines to three or four years because of filtration and oil analysis, and I only changed the oil because we were getting into uncharted territory,” says Symonds. “I don’t know how long this stuff will last.”
“Upper management looks at the bottom line. Six, seven or eight years ago, the bottom line for lubrication improvements wasn’t that great or noticeable,” says Gaedtke. “They look at it now and it is much better. They are aware and they are interested. They want to see more from us.”
“We have 500 or so pumps in the mill. A dozen years ago, the rack in our pump rebuild shop was full as a result of lubrication, contamination and other issues, and we were working overtime to get those rebuilt,” says Weizenicker. “If you look at the rebuild rack right now, there are probably only one or two pumps, and we only have one person doing the rebuilds.”
“Unscheduled downtime on Paper Machine No. 4 has dropped 37 percent since 1999 (from 3.50 percent to 2.21 percent in 2009) and it has dropped 62 percent on Paper Machine No. 2 during that timeframe (4.08 in ’99 vs. 1.56 in ’09),” says Slonski.
In this battle of right vs. wrong, good vs. evil, cleanliness vs. contamination, the superheroes are winning.
It seems as if you can’t walk 50 feet at the PCA mill in Tomahawk without seeing a desiccant breather. Area lubricators at the site religiously use breather products to remove dissolved, emulsified and free moisture from oil drums, gearboxes, hydraulic systems, feed pumps and turbines.
“I put breathers on virtually every piece of my equipment,” says area lubricator Brad Gaedtke. “That has made a huge difference.”
The hygroscopic agent inside the breather starts off as a particular color. As moisture is absorbed, the gel pellets change color. That is a signal to a lubricator to replace the breather with a spare and plug the “wet” breather into an air dryer.
Overnight, the pellets revert to their original color. This breather is marked with a paint pen (signifying the recharging date and the number of times it has been recharged). It eventually is put back into rotation on the plant floor. A breather is used and recycled up to five times before it is discarded.
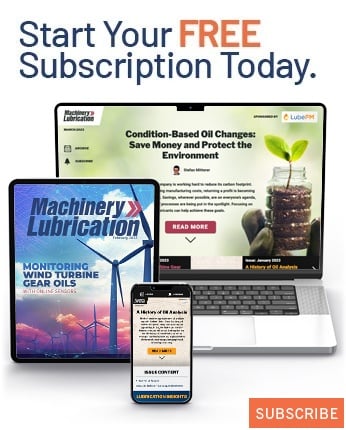