Do you really know how your lubricants become contaminated? Have you taken an inventory of the sources of contamination and the primary points of entry? If not, you are in the majority as sadly, few organizations go to the trouble of performing a contaminant ingression study.
For many machines, the exclusion of contamination is the only way to control contamination. This is because these machines either have no filter or the filter in use is coarse, providing no practical protection in the particle size range of critical oil films.
When particles are not removed by filtration or by settling, a lubricant’s contaminant level equals the machine’s service hours multiplied by the number of particles ingressed per hour (ingression rate). For machines exposed to high ambient dust, particle counts can exceed recommended levels in just a few hours. After days of exposure, an oil can turn into more of a honing compound than a lubricating medium.
A Matter of Mass Balance
Even machines with good filters are faced with ingression challenges. To maintain contaminant levels within targets, the filter must remove particles at a rate equal to the ingression rate (mass balance). The lower the target cleanliness level, the more difficult this becomes. Why? Because in order for a fluid to stay within these high cleanliness targets, by definition, particles are not densely packed in the oil but rather are sparsely distributed - few and far between.
This means that for every gallon of fluid that enters the filter, there are few particles from that gallon that are available to remove. Yet the filter must still remove particles at a rate equal to the ingression rate, otherwise the contaminant level will rise. This places increasing demand on the quality and capture efficiency of the filter (percent particles removed above a certain size).
Also sharply influencing this is the flow rate of the oil entering the filter. The flow provides the necessary conveyance of particles to the filter. If flow rates are low, filters with even 100 percent capture efficiency (beta equal to infinity) cannot remove enough particles to keep up with ingression, causing contaminant levels to exceed targets.
The higher the target cleanliness, the higher the minimum required flow rate for a given filter. After all, a filter can remove only those particles it comes in contact with. Some by-pass and kidney loop (off-line) filters have flow rates that are inadequate for stabilizing target cleanliness levels.
Cost of Excluding Dirt
It is often said that the cost of excluding a gram of dirt is only about 10 percent of what it will cost you once you let it enter the oil. Dirt puts stress on additives, the base oil and machine surfaces. So too, the cost to filter a gram of dirt from the oil is much higher than the cost of filtering a gram of dirt from the air intake/breather. Good maintenance means intelligence maintenance - working smart.
It’s always good advice to stop treating the symptoms and start treating the causes. When we filter dirt from oil, we are treating the symptom. When we exclude its entry, we treat the cause. Let’s work smart.
The word ingression refers to the introduction of particles into lubricants and hydraulic fluids regardless of the source (external and internal). Figure 1 organizes common sources into three subcategories: built-in, ingested and generated. Depending on the nature of the machine, the ingression rate and sources can vary considerably.
For clean-environment indoor equipment, the primary sources can be from process fluids and internal generation (wear, corrosion, etc.).
Machines that operate in outdoor work environments can encounter high levels of ambient dust, representing as much as 95 percent of all particles that enter the oil. Machines that operate close to the ground are prone to higher ingression rates than those that operate high in the air (including aviation) or away from the ground all together (marine).
For outdoor machinery, climate conditions have a marked influence of particle ingestion. For instance, rain and damp soil keep particles from becoming airborne. High winds and dry climates do just the opposite. Don’t forget that particles make particles (wear debris) - affectionately referred to as making babies. This unwanted reproduction won’t occur if particle ingression from the environment is in check.
Controlling Top-End Ingression
For many machines, reducing ingression means reducing top-end ingression; the particles entering through fill ports, vents, breathers, hatches, inspection ports, shaft seals and other headspace openings. There are numerous ways to control top-end ingression in reservoirs, sumps, gearboxes and bearing housings. These include:
Purge Methods
This involves the introduction of a clean gas or aerosol into the headspace of the machine. A slight positive pressure is maintained to prevent the entry of ambient air. Examples include instrument air purge, oil mist purge and nitrogen purge.
Isolation Methods
Expansion chambers, piston/cylinder reservoirs and bladders have been used to isolate headspace air from ambient air to prevent contamination. One disadvantage is that original moisture (humid air) is often unable to escape from the headspace. This also locks moisture into the oil as well. In some cases, users have reported that this has led to heavy corrosion.
Filter Breathers
If reservoirs and sumps can be sealed tightly such that all air exchanged between the atmosphere and the headspace can be directed through a single port, then high quality filter breathers can be used to remove dust from incoming air at that port (vent). The quality of the filter (capture efficiency) should be no less than that of the oil filter in use.
Contaminant Ingression Study
The first step of a contamination control program is to identify a machine’s target cleanliness level. A specific quantifiable number (ISO Code for instance) should be assigned to each machine based on contaminant tolerance, operating environment and motivation for machine reliability. Next, identify the source and entry point of particles. This involves a contaminant ingression study.
Because particles are often internally generated, it’s not simply a matter of doing a walk-down inspection to look for top-end ingression points. For many machines there is a need to examine particles found in used filters, bottom sediment, oil drains and live zone oil samples as a means to determine their origin. This can be done using microscopic methods and by element analysis (testing particles for copper, lead, iron, silicon, etc.).
Multiple oil sampling points in circulating equipment can help isolate ingression to certain components like hydraulic cylinders. Additionally, taking particle counts up and downstream of filters while the machine is in normal service can be helpful in identifying the approximate ingression rate.
Once the source and entry point for particles is found, a strategy can be developed to reduce or stop the ingression. Over the life of a machine, this strategy can deliver considerable benefits and savings to asset owners. These include longer lasting lubricants, seals and filters, negligible flushing requirements at oil drains, and overall improvement in machine reliability. It is important and valuable to discover “from whence dirt comes”.
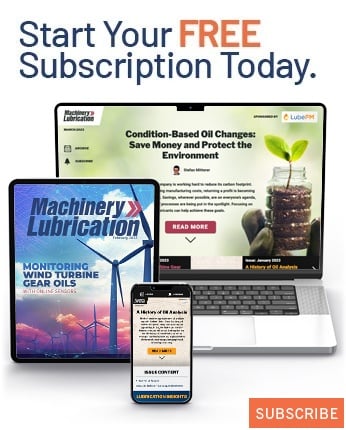