Randy Hall, a predictive maintenance technician at Temple-Inland’s wallboard plant in Cumberland City, Tenn., is one of the subjects of this issue’s “Get to Know ...” feature. He has worked 11 years for this company after spending 20 years performing aviation maintenance for the U.S. Navy. Let’s learn more about Randy.
What types of training have you taken to get you to your current position?: The training and experience I received in the military have been invaluable. I use many of the ideas, principles and practices learned in the aviation field on a daily basis in my current position. Also, I went to several Noria seminars and vibration classes, and spent a lot of time reading books on industrial lubrication and predictive maintenance. Attending conferences and talking with other people doing the same type of work also have been very helpful.
What certifications do you hold?: I am a Machine Lubrication Technician Level II and a Machine Lubricant Analyst Level III through ICML, a Certified Lubrication Specialist through STLE, and a Category III Vibration Analyst through the Vibration Institute.
When did you get your start in machinery lubrication, and how did it happen?: If you can count changing the oil in your own vehicles, I started around 15 when I changed the oil in my dad’s car for the first time. In the Navy, I had to change oil and filters in aircraft engines, gearboxes and hydraulic systems, and took oil samples on engines and gearboxes. Additionally, I took oil samples on the hydraulic systems and ran patch tests on them. At the time, I didn’t realize the significance of what I was doing. After becoming a Class A mechanic at Temple-Inland in 2000, I was asked by the mechanical supervisor if I’d be interested in helping the mechanic that was tasked with starting the vibration program. I had been involved with a little vibration in the service and liked it, so I said yes. Later that year, the maintenance superintendent called us both into his office and told us that the plant was going to start a lubrication program. He said that since the other mechanic had more experience in vibration, he would continue to do that, and I would start the lubrication program. I’m glad he did because I really enjoy working in this field.
What’s a normal work day like for you?: Since we have a small maintenance department, I might be assigned to do lubrication PMs, take and process oil samples, work on rolling stock, collect and analyze vibration data, review PMs, help with a root cause analysis, or help with upset conditions on the production line. It’s always something new, which is one of the things I love about my job.
What is the amount and range of equipment that you help service through lubrication/oil analysis tasks?: There are approximately 900 pieces of equipment at the plant, consisting of gearboxes with half-gallon oil sumps to ones with 14-gallon oil sumps, hydraulic power units, fans with 1-inch-diameter to 4-inch-diameter shafts, electric motors ranging from 1 to 300 horsepower, and various sizes of valves and pumps. I routinely take and analyze oil samples on 100 pieces of critical equipment and 36 pieces of essential equipment.
What lubrication-related projects are you currently working on?: One ongoing project is to increase the cleanliness in bulk and operating oils. Also, I’ve been experimenting with ultrasonics and using high-frequency vibration data to fine-tune the amount of grease needed to relubricate fan and motor bearings. We also are going through all of the lubrication PMs to make sure they are up to date.
What have been some of the biggest project successes for which you’ve played a part?: I am most proud of the changes I made to the lube storage areas. That includes the addition of air-powered pumps with filtration, desiccant breathers, quick-disconnects and sample points, and setting up the pumps to kidney-loop the oil in the drum.
How does your company view machinery lubrication in terms of importance, strategy, etc.?: Management has been very supportive of all the changes that I have made. Without them, it would have been almost impossible to do the things I have done.
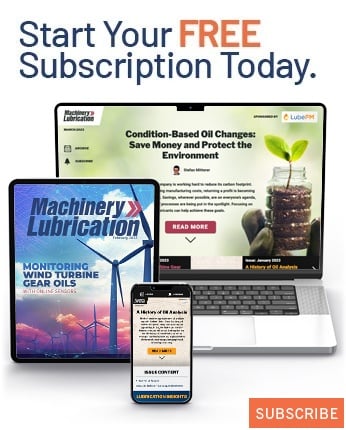