In the world of lubrication, there are many myths that surround certain practices or concepts that may be costing your organization hundreds or thousands of dollars. Some of the top myths are that OEM hardware accessories are satisfactory, filtering new incoming or stored lubricants and periodic decontamination are wastes of time, and the more grease the better (overgreasing). These seemingly harmless misconceptions could be holding your organization back from achieving a world-class lubrication and maintenance strategy and environment.
Myth #1: OEM Hardware is Satisfactory
OEM hardware accessories, including small vent-plug breathers, dipsticks and non-metallic drain plugs, are doing your equipment more harm than good. When in pursuit of lubrication excellence and world-class maintenance, you should consider removing these devices and outfitting your equipment with proper contamination control devices such as desiccant or hybrid breathers, minimess sampling valves, magnetic drain plugs, quick connectors, vented sight glasses, bottom sediment and water bowls (BS&W), etc.
Modifying your equipment to exclude contaminants is more than half the battle. The best way to do this is to make sure you can perform your lubrication tasks without opening up the equipment and exposing the interior atmosphere to exterior atmospheric contaminants. Performing routine inspections, top-ups and sampling should not be invasive to the equipment and should be easy to perform.
Keeping OEM hardware installed on your equipment could be costing your organization thousands of dollars in maintenance costs due to repairs caused by contamination. It is far more cost-effective to spend the money upfront for proper contamination control hardware than it is to keep repairing equipment after it breaks.
Myth #2: The More Grease The Better
This is a costly mistake. Overgreasing can have many of the same negative side effects as undergreasing, plus the added cost of high lubricant consumption. Greasing can be thought of as a purging or filtering of contaminants from the bearing, but you should not exceed a calculated amount of grease when performing greasing activities.
The calculated quantity of grease for a bearing is based on its geometry and dimensions, which provide the ideal amount for re-lubrication. The misconception is to apply more grease than needed to purge out contaminants. The right approach is to apply a fraction of the calculated quantity at a shorter time interval. This helps eliminate overgreasing at a given interval but still supplies the benefit of purging contaminants out of the bearing, just like automatic grease systems.
One of the most common ways to overgrease is to use an automatic grease system without proper calibration, maintenance and greasing quantity and interval calculations. The premise and benefits of automatic grease systems are to provide a small amount of grease very often to promote a more continuous grease application. In order for this to work and be beneficial, the technician must know how much grease to add at the right time and calibrate the automatic grease system accordingly. If it is not calibrated correctly, it is likely that too much grease will be supplied too often, which can result in a bearing failure and high grease-consumption costs.
Myth #3: Filtering Incoming Lubricants and Periodic Decontamination are a Waste of Time
One of the biggest misconceptions is that new oil is clean oil. In many case studies, it has been shown that new incoming oil is dirtier than equipment-developed target particle and moisture cleanliness targets. Filtering incoming oil is far cheaper than removing contaminants once they are inside your equipment. Depending on how tight you set your targets, the quantity and quality of filtration are direct reflections of time and cost.
Imagine setting your target goals for a hydraulic system at 12/10, and your new oil is coming in at 16/14. Taking the time to lower the new oil cleanliness to your target level once the new oil is added to your equipment could cost hundreds or thousands of dollars in labor, repair, operations, etc.
It is best to filter new incoming oil before it enters the storage area, periodically decontaminate the new oil while it is in storage and filter the new oil when dispensing into top-up containers. The best and most efficient way to filter new incoming and stored oil is with a rack-mounted storage system that has integrated filtration and pumping equipment. Having the option to run the storage tank in an incoming circulation and dispensing mode makes decontamination while receiving, storing and dispensing easy and hassle-free.
The mistaken belief that dirty oil is bad oil needs to be changed. When oil is just dirty from contamination, you can clean it up by using many different types of filtration methods, depending on the type of contaminant you want to remove. For particle and moisture contaminants, a filter cart equipped with particulate and moisture-stripping filters is an ideal choice. A filter cart allows for periodic decontamination to occur while the equipment is still in operation by using quick connectors to safely and easily hook up the filter cart and letting it run for 30 or 40 minutes.
The option for unattended filtration while the equipment is still in operation allows the technician to spend his time performing other tasks that may require his attention in a nearby area. It is true that certain contaminants will increase the rate of degradation of the base stock, but quick removal can extend your drain intervals substantially, resulting in a cost savings in lubricant consumption and disposal.
Myth #4: Lubricant Storage is not That Important
Improper lubricant storage and handling likely are costing you a great deal of money. In most cases, lubricant storage and handling are at the bottom of the priority list when they should be at the top. Why spend countless hours and expense designing and implementing a lubrication program for production equipment, setting target and moisture cleanliness goals, performing all equipment modifications required to create a closed-loop contaminant-free system, installing expensive filtration units, etc., just to re-contaminate the in-service oil with dirty oil from improper storage and handling equipment and techniques?
You must be able to get the lubricant from the lube room to the machine without jeopardizing its cleanliness and quality. To do that, you must equip your storage facilities to meet the cleanliness demands of the equipment. Remember, it will cost you 10 percent more to remove a gram of dirt than to exclude it.
This is why it is so valuable to use resources for designing, implementing and outfitting an adequate lubricant storage facility, as well as to use proper top-up containers and transfer devices to perform lubrication tasks.
In addition to being humidity-controlled and pressure-controlled, a proper lube room should have limited access for vital personnel only, adequate new oil storage in pods for periodic de-contamination and dispensing, proper transferring and receiving procedures, sealable and reusable top-up container storage, etc.
The use of filter carts for transferring, draining and periodic decontamination of in-service and stored lubricants is highly recommended. Filter carts make these types of tasks very efficient, safe and contaminant-free, and will yield large gains in equipment reliability and life.
Myth #5: Always Drain and Fill
There are times when drain and fill makes perfect economic sense, but that is not the case for every oil-lubricated asset. It is best practice to only use a drain-and-fill strategy on small sump sizes where the cost of modifying the equipment with quick connects for periodic decontamination with a filter cart is more cost-prohibitive than the lubricant replacement cost.
This table shows the costs associated with various lubrication activities. Note the dramatic savings per year with the on-condition drain and fill in comparison to the standard drain and fill.
Conversely, large sump volumes of oil should not be on a calendar cycle for a yearly drain and fill. Instead, these applications should be on an “on-condition” drain and fill. An on-condition drain and fill is performed based on the condition of the lubricant from oil analysis. This enables the oil to tell you when it needs to be changed from the oil analysis trending results of its physical and chemical properties. Oftentimes, you lose a tremendous amount of a lubricant’s remaining useful life by changing the oil too soon or frequently. Many times oil is changed because of factors you can control, such as contamination.
For really large volumes of oil, such as turbine lube oil systems, the best strategy to employ is the “bleed-and-feed” method. This method reduces the volume of the system by 75 to 80 percent and introduces new oil back into the system. This process will help decrease the amount of existing contaminants by draining them, reduce their concentration with the addition of new clean oil and bring in fresh additives with the addition of the new oil. Many in-service turbine oils will have more than 10 years of life, but by adding 6 to 8 percent makeup oil per year, the life can be infinite.
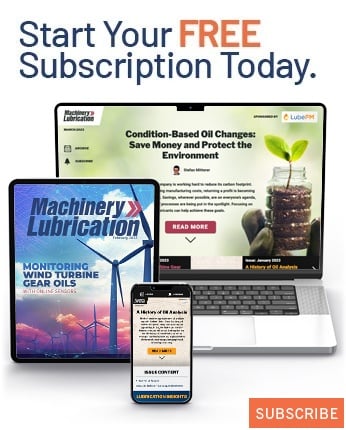