Name: Jan Christensen Age: 60
Title: Lubrication Technician 2
Company: Kennecott Utah Copper
Location: Magna, Utah
Years of Service: 10 years
Jan Christensen began working on heavy equipment as a mechanic in 1973. He started with Fluor Industrial Services working at Kennecott Utah Copper’s smelter in 2002 as a mechanic. He joined the lube team in November 2006 and has worked in several important roles for the lube team, providing valuable input and overseeing key projects since that time.
Q What made Rio Tinto and Kennecott Utah Copper (KUC) decide to put more emphasis on machinery lubrication?
A At the KUC smelter, we implemented changes that led toward improving reliability, including hydrocarbon management in 2001 and 2002. This improvement was aided by Rio Tinto’s corporate drive toward improved reliability and hydrocarbon management during the same timeframe. The rate of improvement increased when Rio Tinto placed additional focus on these areas in 2004.
Q How did you get your start in machinery lubrication?
A I have been working at the KUC smelter since January 2002. Prior to working at the smelter, I worked on heavy equipment for 30 years. I also purchased lubricants and did oil sampling. I came to this job in the lube group in November 2006 under the direction of the reliability group and have been with the group since then.
Q What types of training have you taken or been involved with? What about future training?
A Before working for KUC, I had several hydraulic and electrical training classes on cranes and other heavy equipment. Since coming to KUC, I have had oil analysis level I, II and III and machinery lubrication level I training from Noria, as well as training from suppliers. I have also been involved in several Rio Tinto internal human capital management (HCM) program assessments.
Q What is the range of equipment that you service through lubrication tasks at the smelter?
A We service pumps, fans, conveyor belts, compressors, feeders, agitators, ball-and-roller mills and other smelter-processing equipment.
Q What is a normal work day like for you?
A We have a six-man lube crew that is dedicated to grease and oil-related issues. On any given day, you could find us doing any of the following: oil changes, grease routes, oil routes, oil sample routes and filter cart routes. On these routes, we check automatic lubricators, replacing faulty or empty units as needed, check and maintain oil levels, and inspect desiccant breathers and replace them as needed.
Q What lubrication-related items are you currently working on?
A I am working on installing a head space-management system for our bulk oil totes in an effort to improve our new/bulk oil cleanliness. I am also gathering data to set up electric motor grease routes throughout the plant.
Q How does your company view machinery lubrication in terms of importance, strategy, etc.?
A Our six-man crew works for Fluor Industrial Services, the company KUC contracts to perform maintenance at the smelter. The lube group reports to the reliability group. Both of these groups are highly motivated to make sure the equipment is lubricated properly and with the correct lubricant. Rio Tinto and KUC have high HCM standards, which we are working hard to meet.
Q What have been some of the biggest lubrication project successes in which you have played a part?
A We have installed new poly totes with kidney-loop systems used to store new bulk oils, as well as a lube trailer to be used on some of our remote equipment for oil changes. We have also installed several kidney-loop systems throughout the plant and implemented filter cart routes. I have also been involved with peer review/peer assist HCM assessments at the smelter and other plants within KUC.
Q What do you see as some of the more important trends taking place in the lubrication and oil analysis field?
A We are seeing oil companies being pushed to become more accountable for their products, and we have been getting more on-site oil analysis testing equipment.
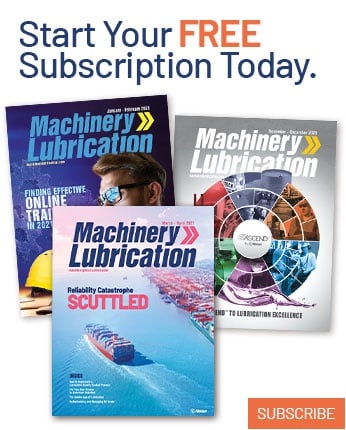