These days an increasing number of companies are trying to achieve a state of lubrication called “lubrication excellence.” Others might call this “world-class” lubrication. Most understand the reliability benefit gained when excellence in lubrication is attained, yet even those who are professionals in reliability and maintenance too often have vague ideas of what defines lubrication excellence.
We all know that machines used in plant production processes are designed and built to engineering specifications intended to achieve a desired level of performance, efficiency and productivity. Using this same concept, it is reasonable to write an engineering specification for machine reliability and lubrication excellence. In the specification would be an itemized list of critical attributes needed to achieve the desired state of reliability. It should be noted that only part of the specification relates to the design and modification of the machine.
In the past, these critical attributes have sometimes been called “best practice” or the “rights of lubrication,” but what exactly defines best practice and these so-called rights? A true engineering specification must be precisely defined and purposeful. It needs to not only permit the desired level of reliability to be achieved but also be within reach of most reliability and lubrication teams.
I would like to introduce a new term called the Optimum Reference State related to the integrated and collective use of these critical attributes. Let me define this important term:
“The Optimum Reference State (ORS) is the prescribed state of machine configuration, operating conditions and maintenance activities required to achieve and sustain specific reliability objectives.”
Note the definition for the ORS does not state a requirement to “maximize” reliability. This is because a point can be reached where the incremental cost of reliability exceeds the incremental benefit (point of diminishing return). Such overspending on lubrication is seen, for example, when synthetics are used in marginal applications or when lubricants are changed too frequently. Like many things in engineering and reliability, there is a “precision” component to good decisions.
Defining Lubrication Excellence
Only after we establish the Optimum Reference State do we have a way to define the meaning of lubrication excellence:
“Lubrication excellence is achieved when the current state of lubrication approaches that of the Optimum Reference State.”
Noria often uses a spider diagram to benchmark a plant’s current lubrication state across 11 categories relative to the Optimum Reference State (represented by the outer perimeter of the diagram). Each spoke of the diagram is a cumulative measure of lubrication performance against critical attributes within that category. The diagram gives a convenient snapshot of lubrication quality at a plant as well as the opportunity for improvement.
The ORS is a state of preparedness and condition readiness that enables lubrication excellence. It gives the machine and its work environment “reliability DNA” as it relates to lubrication. Let’s take a look at some of these enabling attributes of the ORS:
- People Preparedness. People are trained to modern lubrication skill standards and have certified competencies.
- Machine Preparedness. Machines have the necessary design and accouterments for quality inspection, lubrication, contamination control, oil sampling, etc.
- Precision Lubricants. Lubricants are correctly selected across key physical, chemical and performance properties, including base oil, viscosity, additives, film strength, oxidation stability, etc.
- Precision Lubrication. Lubrication procedures, frequencies, amounts, locations, etc., are precisely designed to achieve the reliability objectives.
- Oil Analysis. This includes optimal selection of the oil analysis lab, test slate, sampling frequency, alarm limits, troubleshooting rationale, etc.
66% | of lubrication professionals say their plant has not yet achieved lubrication excellence, based on survey results at www.machinerylubrication.com |
Critical attributes are the building blocks of the Optimum Reference State. These can be broken down into primary and secondary attributes. A primary attribute directly enables a desired level of machine reliability (e.g., the lubricant contaminant level will not exceed ISO 16/13/10). A secondary attribute supports or indirectly enables a primary attribute (e.g., a machine with a high-performance filter). The sum total of all lubrication ORS attributes in a plant is an engineering specification for lubrication excellence.
Moving toward the Optimum Reference State is nearly always a process of modification and transformation. For many plants, this may require more of an intervention. Sometimes the best time for transformation is immediately after a crisis, such as after a costly business interruption from a machine failure.
The modifications needed to enable the ORS can be numerous depending on the type and size of the plant. These include modifying people, machines, procedures, PMs and inspections, as well as condition-based maintenance activities.
Plants approaching the Optimum Reference State might see asset utilization numbers increase from 5 to 10 percent and maintenance cost reductions as high as 10 to 50 percent. Of course, this depends on industry and many operating conditions.
Over the years, Noria has monitored and observed top performers worldwide in the lubrication field. We’ve looked for unique traits that set these companies apart. We’ve found differences that are measurable, verifiable and controllable. These constitute the Optimum Reference State. The benefits are real, and so too are the opportunities to achieve them.
4 Features of ORS Critical Attributes
Critical attributes of the Optimum Reference State (ORS) are similar to dynamic balance and precision alignment in rotating equipment. These necessary precursors to reliability are selected and measured by scientific and engineering methods. Each attribute must be:
- Precise and definable (e.g., a specific lubricant sump level),
- Measurable (e.g., a specific viscosity) or verifiable (e.g., a sample port location),
- Controllable (by modification) and sustainable (by program continuity),
- Able to achieve the desired reliability objectives related to the financial benefit, safety and machine readiness.
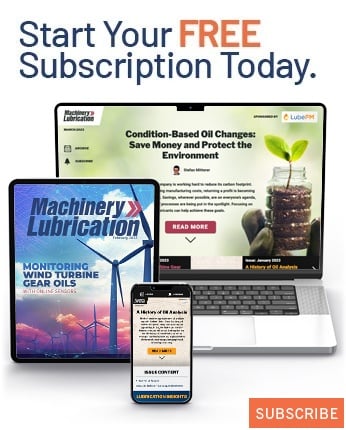