It can be quite a challenge to determine when to flush a turbine lube oil system. If there are no apparent issues with the turbine’s lubrication, an oil flush will often be postponed. But lubrication experts will tell you: just because no problems are apparent doesn’t mean they don’t exist. In fact, unless you’re specifically testing for them, many of the problems that can be solved with high velocity oil flushing go unnoticed until a catastrophic failure occurs.
Turbine Oil Flushing
While some problems have to be identified through oil analysis, there are other times when oil flushing is performed as a matter of routine or best practices, including:
- Before a new machine is commissioned.
- Before restarting a machine that has been laid up for a while.
- If a filter is bypassed or collapses.
- If there is a component failure/replacement.
- When the lubrication is replaced by a different type of oil.
As mentioned, some oil analysis results will reveal the need for a high velocity oil flush. Oil oxidation and contamination can cause many issues that require remediation, which usually involves an oil change. Before new oil is added, an oil flush should be performed to irradicate:
- Varnish
- Sludge
- Rust
- Scale build-up
- Other particle contamination
The Need for Turbine Cleaning
Turbine oil flushing is performed because the things that contaminate and degrade oil can be left behind in a machine even after the oil is removed and changed. These left-behind contaminants then contaminate the new oil, which accelerates lubricant and component degradation and cripples machine efficiency. Early identification of potential problems is one of the tools that can be used to forecast and ward off catastrophic failures; a known problem should be addressed at the earliest opportunity.
When a high velocity oil flush is performed, its success should be measured through testing. Screen inspections and patch testing are two simple ways to ensure that an oil flush was effective.
Screen inspections involve the use of slip screens that are placed between two flanges through which oil flows. If particle contamination is present, particles will build up on the screen, providing a visual indication that the oil is still dirty.
Patch testing quickly determines whether or not particles are present in oil by pulling an oil sample (using a manual or electric pump) through a membrane filter patch. The structure of the membrane’s pores causes the patch to retain particles above a certain size, revealing the presence of particles and allowing for particle inspection.
Get the Job Done Right
When considering a turbine flush, it is important to plan and get the job done correctly. The complex nature of performing a high velocity oil flush makes it a job best suited for experienced professionals. There are many things that can go wrong, and flushing incorrectly can lead to component damage and the continued presence of particle contamination. To avoid an unsuccessful oil flush, consider finding and partnering with a high velocity oil flushing expert.
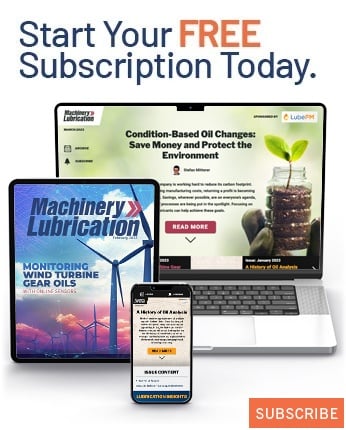