"How frequently should thermographic inspections be performed, and what would be optimal for cost avoidance in maintenance?"
Thermography, oil analysis, vibration and all other predictive maintenance technologies are only as good as the information that is collected, analyzed and then put into action. It begins with the technician taking reliable readings and information, and then a diagnostician evaluating the information and taking action as prescribed by the results. The question then becomes: "How often do we need to gather this information to ensure the machine is operating properly?" The answer is not as simple as the question.
With any maintenance task, there must be a balance between the cost of the task and the machine's criticality. The best way to start is to decide whether the machine merits monitoring. Among the criteria to take into consideration include the machine's safety risks upon failure, mission criticality, repair costs and downtime cost, as well as other factors that may be specific to the process or facility.
Once it has been concluded that the machine is critical enough to warrant the cost of monitoring its condition, the next step is to establish how often it should be inspected. Again, a number of factors should be considered. The more important the machine is and the higher its risk of failure, the greater the inspection frequency. Likewise, if the risk of failure and machine criticality are low, the inspection frequency should be decreased.
It is hard to develop a one-size-fits-all approach to monitoring frequency. To determine how often to perform thermography or other predictive tasks, you must understand how machines fail. For instance, the "bath tub" curve model indicates that machines have a high likelihood of failure when they are initially put into service (infant mortality). The probability then decreases until the machine ages, which could be over several years, before trending upward. Monitoring frequency should be increased during these periods of increased probability.
Another way to determine inspection frequency is by measuring how close the machine is operating to alarm limits. Each technology or measurement technique should have limits associated with it. For instance, with thermography the limits would be based on temperature. For oil analysis, it may be based on particle counts. The closer the machine is to the limit, the more often it should be monitored. If there is a large margin between the limit and the current operating conditions, the inspection frequency can be decreased.
While there is no simple answer to this question, a good inspection frequency can be established by applying some simple principles of machine monitoring. The key for avoiding cost is to first decide whether the monitoring is warranted.
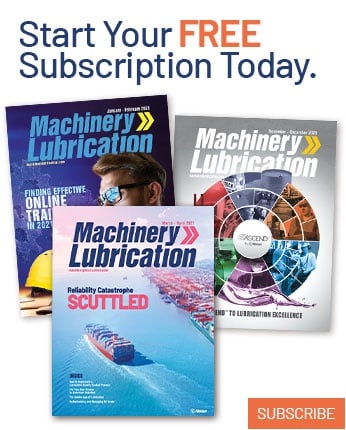