According to the results of Machinery Lubrication's 2013 salary survey, lubrication professionals are earning more, are more satisfied with their jobs and consider their jobs more secure than a year ago. However, the latest findings also reveal several areas where economic recovery seems to have slowed and optimism appears to have declined since 2012.
The annual survey, which was conducted both online and via mail among lubrication professionals in the United States, included employees from companies such as Boeing, DuPont, Dow Chemical, Alcoa, Holcim, International Paper, Luminant and MillerCoors.
For a second consecutive year, workers in Texas and Ohio provided the most survey results, followed by lubrication professionals in California, Pennsylvania, Indiana, Wisconsin and Illinois. We would like to express our thanks to everyone who participated in this year’s survey.
Demographics
As expected, the overwhelming majority of respondents were male, with men accounting for nearly 99 percent of responses, which was an increase from 96 percent over the past two years. In spite of their small numbers, the few women who completed the survey earned 17 percent more on average than their male counterparts, were younger and were more likely to have received a raise in the past year. Women were also more likely to be satisfied with their jobs and work fewer hours.
The average age of survey participants in 2013 dropped to 49, which was one year less than in 2012. The oldest respondent was 72, and the youngest was 23, three years younger than the youngest respondent in last year’s poll. Those workers 40 years of age and younger took home 7 percent less than their older colleagues but were more likely to have received a raise and a bonus in the past year.
Compensation
Although salary increases were reported by more than 80 percent of survey participants, the increases were smaller than in 2011 and 2012, with 75 percent receiving an increase of only 1 to 5 percent. Less than 3 percent of respondents were given a raise of more than 10 percent, while 15 percent saw their salary unchanged from the previous year.
For a second consecutive year, the average salary among survey participants was $82,000, with $200,000 recorded as the highest salary and $24,500 as the lowest. Lubrication professionals in the Southwest earned the highest salaries, receiving approximately 15 percent more on average than their colleagues in the Midwest, which had the lowest income levels.
Education/Certification
While the majority of survey respondents had completed some college work but did not have a degree, those with at least a bachelor’s degree earned 21 percent more on average than those without a degree. Workers lacking a college degree were also more likely to have seen their salaries decrease over the past year. However, a graduate degree did not appear to make much difference in salary levels in comparison to those with only a bachelor’s degree. Predictably, lubrication professionals with only a high-school diploma received almost $10,000 less per year on average than those who had completed at least some college work.
Almost half of all survey participants had achieved at least one professional certification, which also seemed to affect their pay rates. For example, respondents who had obtained a professional certification were almost twice as likely to have received a raise in the past year. In addition, maintenance and lubrication technicians who had earned a professional certification took home 7 percent more on average than those without any certification.
“It has kind of turned into a requirement for my pay raise and bonus to continue every year,” said one respondent about achieving professional certifications. “We have to do so many hours of training in a reliability-related field every year.”
Maintenance and lubrication technicians were also among the workers most likely to have a professional certification, along with workers in food processing, power generation, mining and paper industries. In addition, men were more likely than women to have earned a professional certification.
The certifications that survey respondents most often listed as being paid more for included the International Council for Machinery Lubrication’s Machine Lubricant Analyst (MLA) Level I, II and III certifications as well as the Machine Lubrication Technician (MLT) Level I and II certifications.
Bonuses/Benefits
Although salaries only increased slightly, more bonuses were handed out in 2013 in comparison to the previous year, with 66 percent receiving some form of bonus.
Respondents in the Northwest and Northeast were more likely to have received a bonus in the past year, as opposed to those in the Midwest and Southwest, and women were more likely than men to have been given a bonus in 2013.
Little change was seen in benefits, with 96 percent of respondents receiving health insurance, 94 percent collecting 401(k) contributions and 40 percent of workers reporting profit sharing from their employer, which were only slightly higher numbers than in previous years.
Job Function/Business Activity
Nearly half of all respondents described their job function as either reliability or maintenance, with those in reliability or engineering taking home the highest salaries, and lubrication technicians earning the least amounts. Reliability engineers also received the largest raises over the past year.
Power generation, food processing, chemicals or petroleum products was listed by the majority of survey participants as their organization’s primary business activity. The average number of employees per facility was reported at just more than 800, with the largest plant having 30,000 workers. Interestingly, lubrication professionals working in facilities with at least 500 people earned 12 percent higher salaries than those in smaller plants with less than 500 workers.
Almost 60 percent of survey participants said they do not supervise any employees. However, those who served as supervisors made almost $10,000 more per year on average and were more likely to have received a bonus in the past year.
Length of Service
On average, lubrication professionals worked longer hours than in previous years, with 79 percent putting in more than 40 hours each week. One-fourth of survey participants claimed to work more than 10 hours each day, while a few even said they worked 70 or more hours a week. These longer hours seemed to boost respondents’ pay rates, as those working more than 40 hours a week earned 22 percent higher salaries and were much more likely to have received a raise than those working only 40 hours each week.
Survey participants reported working 14 years on average for their current employer, with the longest tenure being 42 years. Unlike previous years, experience appeared to have a significant impact on salary, as those workers with less than 10 years of experience in lubrication-related work earned 16 percent less than those with more experience. In addition, those with 20 or more years of experience took home almost $15,000 more per year on average than their less experienced colleagues.
Job Security/Satisfaction
The number of lubrication professionals who believe they are fairly compensated and are satisfied with their jobs increased in 2013 to almost 75 percent. Workers in the chemicals and power generation industries were the most satisfied with their jobs, while those in machinery manufacturing, paper and food processing were among the least satisfied.
The factors most contributing to job satisfaction included challenge and stimulation, work environment/culture, and salary and benefits.
When asked what they disliked most about their jobs, most survey participants cited lack of management support, lack of recognition or the hours and workload.
“Our management does not think about the effect its decisions have on the health of the equipment,” complained one respondent. “They always want to wait to perform the maintenance/PMs until the equipment needs repair instead.”
Workers in the Southwest were the most likely to believe they are fairly compensated, as opposed to those in the Northeast, who were the least likely to feel their compensation was fair.
Eighty-six percent of survey takers considered their jobs secure, which was an increase of 5 percent from 2012. Although less than 10 percent of respondents anticipate lubrication-related jobs being added at their organization in 2014, almost two-thirds do not expect any jobs to be lost.
2014 Forecast
Survey participants were also not quite as optimistic with regards to how they expect their salary to change in the coming year, with only 66 percent anticipating an increase in 2014, which was a 2-percent drop from 2012. Almost one-third of respondents expect their salary to remain the same, while only 3 percent fear a decrease in compensation.
Workers in the Southeast and in the power generation industry were the most optimistic with regards to their salaries in 2014, while those in the Midwest and in the primary metals and manufacturing industries were less optimistic.
Among the greatest concerns lubrication professionals have for the coming year include the aging workforce and the lack of training.
“My greatest concern is whether the company will be able to continue to operate as lean with the small number of craftsmen and be able to maintain all the equipment,” wrote one survey respondent.
“Staffing levels have been reduced the last two years in addition to higher retirement levels due to the older workforce,” added another survey participant. “A lot of experience is gone!”
Others expressed concerns about the economy and far-reaching government regulations.
“I work at a coal-fired facility,” noted one survey taker. “A sluggish economy, uncertain environmental policies and low natural gas prices limit our generation output. This situation may force my company to use me and my co-workers as regional assets. This change would incur a lot of travel between facilities and general uncertainty.”
“Extremist environmentalist groups are forcing their unsubstantiated climate-change agenda on the uninformed and apathetic American energy consumer, along with onerous regulations being forced on energy-producing companies,” remarked another lubrication professional.
Respondents were also worried about the welfare of their companies, with the greatest threats identified as global competition, poor management, lack of innovation, environmental regulations, lack of experienced personnel, and cost and availability of raw materials.
“Not wanting to move into the 21st century,” replied one survey participant when asked about the greatest threat his company faced. “This is the way we have been doing it for 30-plus years.”
“Clients are trending toward lower price rather than toward value-driven lubricants,” said another survey respondent.
“My company just filed bankruptcy, so I don’t know if it will survive,” wrote another worker.
For additional survey results or to participate in the next Machinery Lubrication poll, go to www.MachineryLubrication.com.
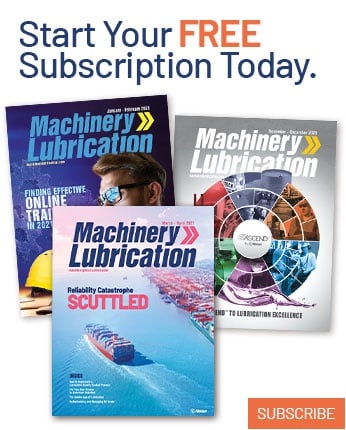