Name: Brandon Lisch
Age: 28
Title: Predictive Maintenance Technician
Years of Service: 2 years
Company: Suncoke Energy
Location: Middletown, Ohio
Throughout his career, Brandon Lisch has held a number of positions, such as industrial cleaner, scaffold erector/inspector, maintenance mechanic and lead lubrication technician. Now as a predictive maintenance (PdM) technician for Suncoke Energy, he is developing a world-class lubrication program. Lisch’s facility in Middletown, Ohio, has been making strides in changing its culture in terms of lubrication best practices. This includes building a lubricant storage facility, training, 5-S principles, equipment modifications, a color-coding system and standard operating procedures. Suncoke is also exploring options for an in-house oil laboratory to complement its lubrication program.
Q: What types of training have you taken to get to your current position?
A: I have had training in precision maintenance, PdM technology, lubrication best practices, root-cause analysis, troubleshooting and precision alignment.
Q: What professional certifications have you attained?
A: In terms of lubrication, I currently hold the following certifications from the International Council for Machinery Lubrication (ICML): Machine Lubrication Technician (MLT) Level I and Machine Lubricant Analyst (MLA) Level I, II and III. I also hold multiple certifications in different predictive maintenance technologies.
Q: Are you planning to obtain additional training or achieve higher certifications?
A: I plan to increase my knowledge in every predictive maintenance technology to the maximum certification level allotted in each field. I feel that doing so will benefit both me and my company, since each technology complements the other in relevance to the P-F curve. Faults or early discrepancies within machinery can be identified, monitored and flagged with better accuracy.
Q: What’s a normal work day like for you?
A: My average work day first consists of performing preventive and predictive maintenance tasks. Once those tasks are finished, I continue to develop the predictive maintenance programs and projects to help increase the reliability of the facility. From time to time, I troubleshoot issues in the field and perform root-cause analysis.
Q: What is the amount and range of equipment that you help service through lubrication/oil analysis tasks?
A: I service all of our facility’s equipment, ranging from our oven machinery to our belt conveyors. I also handle all lubrication tasks that are of a precision nature, including pulling oil samples. We conduct condition-based oil changes, so proper sampling practices must be followed accurately to evaluate the health of our machinery and lubricants. I also perform the lubrication on all of our electric motors and high-speed bearings using airborne ultrasonic technology to apply lubricant with precision.
Q: What have been some of the biggest project successes in which you’ve played a part?
A: The biggest success has been the development of the PdM programs, including the lubrication program here at Suncoke Energy Middletown Operations. The strides the company has made and the full support of reliability are helping make these programs flourish. At the rate of development, it will not be long before Suncoke is named a world-class facility. That is the overall goal for us all.
Q: How does your company view machinery lubrication in terms of importance and overall business strategy?
A: Machinery lubrication is one of the most important, if not the most important, aspect in machine reliability. All other proactive activities performed would be in vain if the lubrication aspect of the machinery is neglected or improperly performed. Lubricants are the lifeblood of a machine. Suncoke fully supports this statement and understands the value of implementing this program to better serve our customer, community and the environment with the reduction of unexpected failures.
Q: What do you see as some of the more important trends taking place in the lubrication and oil analysis field?
A: The most important trend I see is the increase in lubrication knowledge. Industries are steering away from the “grease monkey” persona and beginning to believe in the skilled lubrication professional. It has been proven time after time that a fully developed lubrication program is one of the keys to success when it comes to machine reliability. Strides in these fields are taking the lubrication profession to a new level.
Q: What has made your company decide to put more emphasis on machinery lubrication?
A: In the coke-producing industry, the dust from the process is extremely harmful to our equipment. Coke is a carbon-based product that has a hardness ranking of 10 on the Mohs scale. Intrusion of coke dust or any foreign particle into an asset could be detrimental to our equipment and operation. Proactive measures like the prevention of ingression by following lubrication best practices is more economical than being in a reactive mode and replacing machinery due to an unexpected failure caused by improper lubrication practices.
How You Can Be Featured in the Next "Get to Know" Section
Would you like to be featured in the next "Get to Know" section or someone who should be profiled in an upcoming issue of Machinery Lubrication magazine? Nominate yourself or fellow lubrication professionals by emailing a photo and contact information to editor@noria.com.
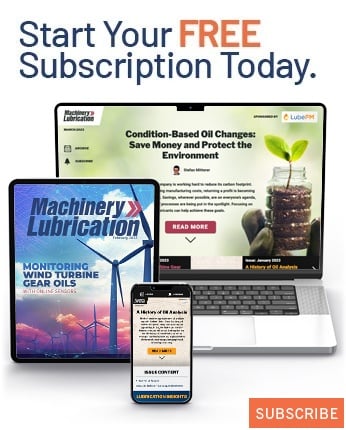