Many companies thrive on financial performance metrics. Share price, earnings per share and return on net assets are taught religiously in every business school. This information is used to assess an organization’s financial health and drive current and future decisions. Even if you are not a CEO or investor, you probably are familiar with these metrics.
Just as important are the metrics for safety coordinators, production managers and site managers. Unfortunately, few people understand lubrication and reliability metrics, much less use them. These metrics are not typically taught in engineering or management schools. This leads to a serious failure in recognizing the impact that lubrication has on a plant’s production, profit and safety.
For many plants, lubrication remains a challenge even to this day. According to numerous case studies, when a machine fails, the likelihood that the failure was in some way related to lubrication is greater than 70 percent. Lubrication key performance indicators (KPIs) can go a long way to help identify not only these issues but also others that affect production, profit and safety. They are all related and integral to a facility’s overall success.
Why have maintenance KPIs failed to become mainstream? Is it because they are not being taught? When was the last time you read about lubrication KPIs in a textbook or worked for a company that used them? As part of my role with Noria, I travel around the world and help companies get their lubrication programs on the right track. One observation that I have made over the years is that if your company is using lubrication metrics, you are in the top 2.5 percent of the industrial world.
The foundation for lubrication KPIs starts with a few simple questions. Have you analyzed your mission as a company or group? Write down your three main objectives. The KPIs will need to relate to this mission in some way.
Have you identified the stakeholders? When you complete your mission, who benefits? These are the people or companies that would be most interested in the results of your KPIs.
Have you defined your goals? The majority of KPIs should be tied directly to achieving your goals.
Next, let’s set a few ground rules for these KPIs. No single KPI can adequately measure all aspects of a lubrication program. This means you must have multiple KPIs to make sure the data is reinforced.
Each area of interest should have a limited number of KPIs (maximum of four to six) that will drive the desired behavior. If too many are selected, you may get lost in the data and data collection and lose sight of your objectives.
KPIs must be relevant and specific to the particular program aspect they are designed to measure and preferably prepared from data that is available from existing systems. This makes the data collection much easier.
KPIs should also have an associated target figure or finite goal. This could be dollars, a percentage, cleanliness level, etc., but it must be measurable in some way.
Finally, the KPI must be presented in a clear, summarized format that shows present and historical performance, targets, benchmarks, etc.
Now that you have a foundation and some ground rules, I’d like to offer a few examples of KPIs that can help you achieve your lubrication program objectives. There are five categories for these key indicators.
Oil Analysis KPIs
Oil analysis KPIs are meant to verify the quality of the lubrication being applied to equipment by monitoring relevant machine condition indicators. For oil analysis data to be used as a meaningful KPI, it is vital that targeted alarms and limits are set appropriately.
While loose limits may result in compliance with lube condition and contamination targets, their meaning may diminish to such an extent that they become irrelevant as a KPI. When setting targets, don’t consider where the plant is today but rather what targets need to be established to attain the plant’s stated reliability goals.
Once appropriate targets have been set, logging exception results becomes relatively easy given the availability of commercial oil analysis software packages.
New oil deliveries can be treated in much the same way as assets in the field. They should be tested for cleanliness, dryness and fluid properties.
You can also use oil analysis data to get an idea of machine health, lubricant health and contamination levels.
Work Management KPIs
These KPIs are required to evaluate the efficiency and effectiveness of routine and ad-hoc lubrication task planning, scheduling, execution and review. While a number of lubrication KPIs can be generated using data from a computerized maintenance management system (CMMS) or other generalized predictive and preventive maintenance management tools, some of the most valuable KPIs require data gathered at individual lubrication points.
The lubrication task completion KPI gives managers a clear picture of the overall efficiency of lubrication practices at the task level. It is a measure of the total number of completed lubrication tasks divided by the total number of scheduled lubrication tasks over a certain timeframe. A low number may reveal inefficiencies in areas such as lubrication routes, workload balancing, resource allocation or equipment access.
The lubrication tasks overdue KPI reflects the total number of lubrication tasks not yet completed versus the total number scheduled. A high number here reveals similar concerns as a low task completion score. More importantly, this KPI, along with the lubrication task completion KPI, tells maintenance organizations how often and to what degree lubrication goals are being met.
Storage and Handling KPIs
Storage and handling of lubricants and associated consumables in the appropriate types, amounts and condition is an important enabling factor in the provision of quality lubrication.
Health, Safety and Environmental KPIs
These metrics and targets should reflect the overall site health, safety and environmental system with a particular focus on lubrication. They provide valuable insight to help engineers and technicians rapidly spot potential problems and trends.
The waste oil collection rate KPI can be a broad measure of the amount of lubricant used over time across different facilities or a more tightly focused view of lubricant consumption within a given department or area of the plant. Irregular levels of consumption may indicate leakage, poor lubrication practices, issues with lubricant quality or other concerns.
Macro Level KPIs
Some high-level lubrication KPIs provide a snapshot across entire operations. These are indicative of overall equipment condition. One of these is overall asset health, which is a useful gauge of plant readiness. It shows the percentage of all equipment in a facility with no known issues or defects.
Another helpful KPI is lubrication-related failures, which is often a simple calculation of the monetary cost, number of incidents or other measures of equipment failures that can be traced to lubrication over a given period of time.
Keep in mind that achieving lubrication success is difficult, and all but the best will struggle. Setting goals and putting procedures into place to guarantee that proper lubrication practices are followed will greatly increase the likelihood of program success.
Only then should KPIs be established for continued improvement. After all, what use is it to spend time, money and energy to measure something that you already know needs improvement, other than to look back and remind yourself how far you have come? As always, if you need assistance or someone to point you in the right direction, I’d love to help.
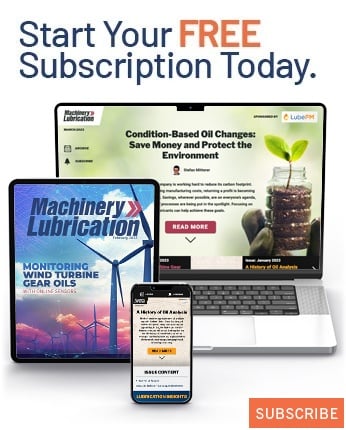