Lubricant procurement is not the largest expenditure in a typical maintenance budget. However, it is viewed as a real, tangible expense that is frequently targeted for cost reduction. When it comes to lubricants, it is unwise to pretend to save money by “buying cheap.”
Lubricants are the lifeblood of your machinery. Your machines’ life expectancy depends largely on the quality and state of these lubricants to bathe heavily loaded frictional surfaces. This also goes for investing in quality technologies and tools used in your lubrication program (such as routing software or automated lubricators) to promote efficiency. Optimum reliability and lubrication must go hand in hand.
Now that you are aware of the perils of poor-quality lubricants and lubrication, let’s take a look at the many opportunities to reduce lubricant spending without compromising reliability. Start by writing a simple lubricant specification for each machine.
Don’t rely solely on the recommendations of the equipment supplier or service manual. Instead, be bold and challenge generic or generalized statements relating to viscosity and lubricant formulation.
Once again, there is a need for caution. I’m not suggesting willy-nilly lubricant changes in an effort to enhance reliability by trial and error. There is always risk associated with changing lubricants. Smart practices, though, can quickly overcome these dangers. Risk should be respected but not feared.
The lubricant specification should be aligned with the optimum reference state for machine reliability. In constructing this specification, you should understand machine failure modes and overall machine criticality as a foundation to defining a machine’s precise lubricant needs.
There is a vast number of lubricant types available from both major and independent suppliers. Navigating the maze of options can be daunting but often very worth the effort. Find help if needed.
Reducing lubricant spending requires change and initiative. For many organizations, the low-hanging fruit is obvious. Below are five effective strategies for reducing your annual lubricant spending.
1. Precision Optimum-life Lubricant Selection
Optimum means optimum. Don’t overspend and most definitely don’t underspend – it’s important to resist the lure of cheap oil. Attempting to save money by buying economy-formulated lubricants for the wrong application is hazardous.
Likewise, don’t be trapped by the false promise of forgiveness. It is equally hazardous to attempt to remedy bad lubrication practices by buying expensive premium lubricants.
42% | of lubrication professionals say performance specifications are the factor that most influences their lubricant purchases, according to a recent survey at MachineryLubrication.com |
Beware of small differences. Selecting an optimum lubricant for a machine application is an engineering process. Small differences in lubricant performance can translate into huge differences in machine reliability and lubricant cost. Don’t choose just any lubricant – seek the optimum.
Be conservative with the number of lubricants in your plant, though. Reduce the number of lubricants in your storeroom to a comfortable and efficient few. The number and range of lubricants you need will depend heavily on the types of machines and their operating environment.
Long-life lubricants in the right application make a lot of sense. They extend drain intervals and lower the cost and risk of premature lubricant failure. Selecting a long-life lubricant can reduce oil consumption in many cases by more than 50 percent.
Still, it is important to be prudent. Don’t invest in long-life lubricants for an application where they have to be changed frequently for other reasons (e.g., contamination) or where excessive leakage can’t be controlled.
2. Proactive Lubricant Life Extension
In normal service, lubricants age over time in a linear fashion. Eventually, they die due to additive depletion or other causes. However, life expectancy is not only related to the quality of the lubricant but also to the type and extent of in-service exposures.
The most destructive exposures are contaminants such as heat, air, moisture, and water. This has been discussed extensively in the pages of Machinery Lubrication. Most users dismiss the opportunity to make practical exposure changes and enhance machine reliability and lubricant life.
This is a pity because contamination control often constitutes the easiest and most certain savings opportunities. Go with what works.
Exposures also relate to topping up a machine that contains remnants of an aged lubricant with a new lubricant. When new lubricants are mixed with oxidized, degraded oils, they quickly degrade. You could say old, damaged lubricants are infested with diseases that can rapidly infect the new incoming lubricants.
In many cases, additives in an aged lubricant should be reconstructed. Rather than disposing of all the oil and then replacing it, a far more economical approach would be to only replace the offending degraded additive. Although this practice may bring criticism from lubricant marketers, there are reputable companies that can help make good science-based decisions.
SKF is one such organization increasing the overall life expectancy of lubricating oils while reducing the total lubrication cost for the company. Developed by an expert team of chemists and processing engineers, the SKF RecondOil program uses a specialized chemical booster to attract dirt and separate it from the oil, effectively regenerating the oil for further use. By revitalizing and reusing quality lubricants, companies can begin to see a reduction in the overall amount being spent on their oil.
3. Optimizing the Relube Interval
Don’t change a lubricant too soon or too late. Many lubricants are changed using regimented practices or simple guesswork. This is usually the case with automotive oil and filter changes. It is also true with the vast majority of industrial lubricant applications. Frequently, lubricant sumps are purged and recharged far too soon.
Use oil analysis as your metric to optimize the interval and avoid premature disposal of an expensive commodity. For instance, if the oil is analyzed at the end of a typical service interval and the remaining useful life (RUL) is found to be 75 percent, extend the interval for the next drain and charge. Keep fine-tuning the interval until an optimum interval is established with reasonable margin for error.
Many machines should not be subject to interval-based oil changes at all. Instead, their lubes should be changed “on condition” and only when there is a true need. Let the oil tell you when it needs to be changed, not the calendar. Condition-based oil changes make the most sense for large sumps of expensive lubricants and/or those requiring periodic top-ups.
In certain applications, grease lubrication can also be optimized from the standpoint of the relube frequency and amount. This can be done using grease analysis (with proper sampling) but also by inspecting used grease in bearing and motor rebuilds.
The amount and condition of the grease in these bearings can offer insightful information for optimizing the relube interval and volume.
4. Reducing Package Waste
Many lubricants sold in drums and packages fail to get fully consumed. Frequently, unused lubricant is left behind in the package. Various strategies can help to minimize waste oil, including using smaller packages or bulk oil. These tactics should be optimized for the machine or group of machines in which the lubricant is used.
Another culprit of waste is the top-up container. These small containers that are carried to the point of lubricant application are often partially full when they are set aside. The oil left in the container is later questioned regarding its type and condition.
This doubt commonly leads to the oil being dispensed into a waste oil container. To prevent this from occurring, make it a practice to label the condition and grade of top-up residuals.
5. Reducing Leakage
Leakage control makes good sense for a number of reasons. Not only are there lubricant consumption savings but also reliability and safety benefits. Don’t turn a blind eye to leakage; address it early. Avoid Band-Aid fixes, and instead seek permanent and complete solutions.
The table above offers a hypothetical example of the potential for reducing lubricant consumption and overall annual lubricant spending. The opportunities vary considerably depending on the current amount of waste and inefficiency in your plant.
If you are uncertain of your potential for savings, hire a specialist to perform an assessment that benchmarks your current practices to the optimum reference state (best practice).
As previously stated, it’s not necessarily about buying cheaper lubricants but rather the optimum selection of lubricants and a proactive strategy for reducing lubricant consumption. Once these efficiencies are put in place, the savings you gain will recur each year, resulting in a nice annuity with minimal effort and investment..
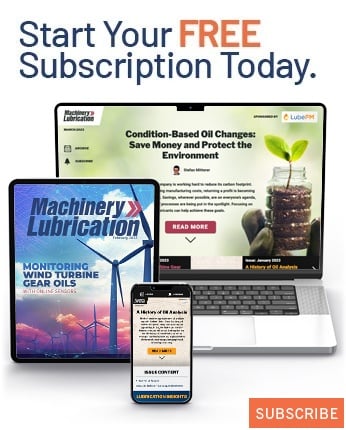