In my travels over the last decade designing lubrication programs, I’ve seen a shift in the profile of lubrication experts. I can remember walking into plants where lubrication was viewed as a menial task that could be delegated to the lowest skilled employees with little to no training. Visits to these types of facilities are few and far between these days.
There has been a massive change in most companies’ approach to maintenance, reliability and lubrication. Perhaps it was spurred by the economic challenges of the last few years, or maybe it was just time for a change. Regardless, organizations are having to do more with less and are finding that being proactive with maintenance and reducing their upfront operational costs can have a huge effect on the bottom line.
Today, there are many different lubrication roles. A simple search on a job-posting site will reveal a number of companies looking to fill the void in their programs which has resulted from years of undertrained, undervalued and underutilized people as well as a culture that fostered the decay of the position.
Thankfully, this is now a thing of the past, as organizations are waking up to the reality that having the right person for the job could potentially save millions of dollars in lost production, machinery downtime, safety, etc. This is great news for those who are well-versed in lubrication and oil analysis. You are now a wanted, needed commodity with a limited quantity, and in business that means money in your pocket.
Let’s take a closer look at these voids in the lubrication field, including some of the current positions that are available at major manufacturing facilities.
Lubrication Technicians
The frontline defense against machinery wear and failure, lubrication technicians know the best practices and perform them routinely. They are not oilers. This position makes the oiler extinct. A lube tech is a thinking worker who has mastered the skills needed to perform at an extremely high level.
The benefits of having a technician who is “in tune” with the equipment and knows what it should look, sound, feel and even smell like are enormous. If these individuals can also troubleshoot issues while they are still in the proactive domain of the failure curve, they are worth their weight in gold.
Lubricant Analysts
A lubricant analyst is a condition-monitoring professional. This person is literate in the language of oil analysis and knows how to routinely extract critical reliability information from lubricants by asking a series of precise questions. The answers will relate to the health of the machine, the oil and the contaminants it contains.
Lube analysts interface with others in the lubrication field as well as analysts in vibration, thermography, acoustics, etc. Often this individual is skilled in many of the other condition-monitoring technologies, further leveraging the synergy these trades have when combined.
Machinery Lubrication and Reliability Engineers
Lubrication engineers are the mentors to lubrication technicians. They have a desk job but spend the majority of their time trying to translate what is written in engineering textbooks to what works well on the plant floor. They are a technical resource for others who need specific lubrication information.
While the lube tech is out in the field practicing world-class maintenance and lubrication, the lubrication engineer is responsible for identifying the optimum reference state for equipment, documenting the procedures and training the staff so everyone is operating with the same expectations.
Lubrication Management Professionals
In the past, this role would have been part of a maintenance manager’s duties, but today it requires an individual’s full-time, undivided attention. Unlike the positions mentioned previously, which are technical careers, the lubrication management professional advances along a management path.
Those who are cut out for management with lubrication training have a real opportunity at large plants, mills and fleet organizations as companies increasingly pull lubrication into the forefront of maintenance and operations.
In less than 10 years, the lubrication field has gone from oilers to professional careers focused on the intricacies of lubrication and oil analysis. What do the next 10 years have in store? Will being the “lube guy” require a stint at the local university to learn the knowledge necessary to bring value to the company?
Obviously, technology will advance. When will the lubrication technician carry a pocket-sized oil analyzer that can rival today’s offsite laboratories? Those days are coming, and with the realization of the value that these seemingly simple tasks can bring to an organization, they are coming at an exponential rate.
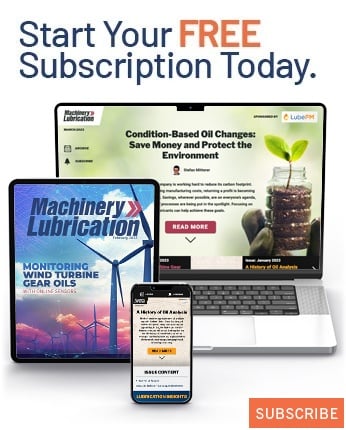