Name: Bob Chenevey
Age: 61
Job Title: Mechanical Systems Manager
Company: Upper Occoquan Service Authority
Location: Centreville, Virginia
Length of Service: 4 years
Bob Chenevey is the manager of mechanical systems for the Upper Occoquan Service Authority (UOSA), a municipal water-reclamation plant in northern Virginia that processes 54 million gallons of water per day. Before Chenevey’s arrival, the plant had been utilizing oil analysis and reducing its number of oils. However, over the past four years, Chenevey has been part of expanding these efforts through training, improving the lube room and consolidating lubricants. The plant now uses desiccant breathers on machinery and has installed shelving and a bulk storage system with individual filters and pumps. It has also changed its sampling techniques to allow for better, more representative oil samples.
Q: What types of training have you taken to get to your current position?
A: I have taken countless hours of communication and management courses to learn how to work with many different personalities. I’ve also taken writing, project management and finance courses, all of which are needed to be a manager today. However, some of the most critical training came from the U.S. Department of State when I went through five months of culture management, leasing, construction and procurement training. This was designed to acclimate me to a life of working with Foreign Service National employees and contractors at overseas embassies. It was a “mandatory pass” set of courses and tests to ensure that I would be successful working in those different cultures.
Q: What professional certifications have you attained?
A: I used to hold steam engineers licenses, but I’ve let those lapse because I simply don’t need them. I still carry a Facilities Management Administrator and Systems Maintenance Administrator certification with Building Operation and Maintenance Institute (BOMI) International. That said, I am surrounded by loads of talent. Here at UOSA, we have many technicians who are driven to get certifications, which is something I respect immensely. We have a lead mechanic with an Association of Boards Certification (ABC) Plant Maintenance Technologists Level I and II certification, and a lead mechanic who holds a Level I Machinery Lubrication Technician certification from the International Council for Machinery Lubrication. Other shops have electrical masters and journeyman licenses as well as infrared certifications.
Q: Are you planning to obtain additional training or achieve higher certifications?
A: I am not personally. However, the shop base will continue working to gain further certifications. Although it is not a requirement for our mechanics and electricians to hold certifications, UOSA has taken the stand to support our mechanics, electricians, techs and operators with bonus awards whenever certain certifications are obtained.
Q: What’s a normal work day like for you?
A: I’m pretty much a 40-hour-work week person. We have a good computerized maintenance management system (CMMS) that I look at frequently. We have two lead mechanics who perform all the mechanical functions, working primarily with the mechanics, work orders and repairs to keep the plant in good condition. I do the other stuff such as working with the guys trying to figure out their training needs, working with budgets, writing scopes of work, working with upper and lateral management, and coordinating between engineering, maintenance and our treatment process folks who handle the plant operation on a daily basis. We also contract out much of our heavy maintenance items, and between the leads and myself, we provide a great deal of support to our contractors. Over the past year or so, I’ve been involved with asset management, looking into the future and identifying plant needs on critical equipment through our capital improvements program. Operations, maintenance and engineering work well together here at UOSA, and we are successful because of that.
Q: What is the amount and range of equipment that you help service through lubrication/oil analysis tasks?
A: When I came here, I made the decision to test only equipment that had more than 1 gallon of oil. For equipment with 1 gallon and less, it made sense to change the oil rather than test it. This left more than 300 pieces of equipment for oil analysis, ranging from air compressors and blowers to large engines and a wide variety of high-viscosity gearboxes. We have large centrifuges, two bio-solids dryers, filter presses, a cogeneration plant, digesters, bio-reactor equipment, a granular activated carbon (GAC) regeneration system, emergency generators, 37 clarifiers and countless pumps. Within that, there is plenty of mechanical equipment for us to maintain.
Q: On what lubrication-related projects are you currently working?
A: We just bought a bulk storage system with individual pumps and filters. We’re not expanding, just continuing to consolidate our lubricants. This year we committed to using a filter cart for high-viscosity oils. Since we have 37 clarifiers with unfiltered oil, it makes sense to perform an annual cleaning. Each of these clarifiers holds as much as 18 gallons of oil. That’s an expensive endeavor when an analysis comes back as “marginal.” We know we can clean it and get it back to normal using the filter cart. We are looking at a payback of a single year in oil savings and extending the life of the oil by at least two years. Once our mechanics start seeing the benefits of cleaning vs. replacement, we’ll work toward smaller carts to perform cleaning on some of our other smaller gearboxes and drives.
Q: What have been some of the biggest project successes in which you’ve played a part?
A: Within UOSA, I think our cogeneration plant is certainly the most lucrative. We use bio-gas produced from our digesters to generate 845 kilowatts 24 hours a day, seven days a week with an uptime of more than 90 percent in the past year. It’s a small plant, but it’s about 20 percent of our overall power demand. Over the course of a year, that’s a substantial savings. Since I’ve been here, we’ve started a new GAC regeneration furnace, a new centrifuge and a new bio-solids dryer. For me, it was a matter of sitting through design and review meetings so that as a team, UOSA could ensure a good end product.
Q: How does your company view machinery lubrication in terms of importance and overall business strategy?
A: On a scale of 1 to 10, probably in the 3 to 4 range, but not because they don’t care. It’s because they’ve delegated it to our level. Lubrication is a function of the mechanics and technicians understanding the importance of good practices and knowledge. My manager knows that it’s important, and he is completely supportive of anything we do, encouraging us to continue, move forward and strive for lubrication perfection.
Q: What do you see as some of the more important trends taking place in the lubrication and oil analysis field?
A: I think filtering is key to a good program. I believe emphasis needs to be placed on filtering before changing the oil. At least then you can get all you can out of the oil until it no longer has the physical and chemical properties to reliably lubricate.
Q: What has made your company decide to put more emphasis on machinery lubrication?
A: Many of us have attended conferences where best practices and proper lubrication have been the focal point. We all know that good, clean oil helps make bearings and wear surfaces happy. It’s been a long haul though. Some of this can get expensive, between sampling, sampling equipment, filtration and training. I think you have to first figure out the real need. How many failures have you had due to improper lubrication, or is it a matter of increasing the life of your oil? This is how we are rationalizing it. If a plant is having a lot of failures, then there is something wrong with the maintenance program in general. For us, we want to simply extend the life.
Be Featured in the Next ‘Get to Know’ Section
Would you like to be featured in the next “Get to Know” section or know someone who should be profiled in an upcoming issue of Machinery Lubrication magazine? Nominate yourself or fellow lubrication professionals by emailing a photo and contact information to editor@noria.com.
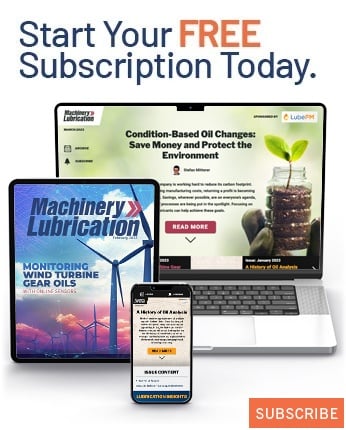