Name: Joseph F. Waterhouse
Age: 60
Job Title: Reliability Technician
Company: Cloud Peak Energy
Location: Gillette, Wyoming
Length of Service: 17 years
Joseph Waterhouse began his career in machinery lubrication while serving in the U.S. Coast Guard aboard a buoy tender. As a maintenance fireman, he was charged with the lubrication of the ship’s propulsion shafts and testing oil and grease for viscosity, fuel and water dilution. Currently at Cloud Peak Energy’s Cordero Rojo Mine, where he has worked for 17 years, Waterhouse has helped to improve the mine’s lubricant handling and lubrication management systems. Before the mine’s new lube building was established, the area where lubricants were stored was dusty with water leaks and poor door seals. Dirty funnels were also in use, which resulted in dirty oil. Now the mine has a clean, organized space and labeled transfer containers so cross-contamination of oils and greases no longer occurs.
Q: What types of training have you taken to get to your current position?
A: Most of my training has been provided by the manufacturer of the equipment or supplier of the machinery used at the site. Some lubricant suppliers and lubrication equipment manufacturers have offered training as well. I also attended Noria’s Industrial Lubrication Fundamentals three-day course.
Q: Are you planning to obtain additional training or achieve higher certifications?
A: My plan is to keep improving my lubrication skills through training and the use of new technologies. The Level I Machine Lubricant Analyst certification is on my list. It’s not enough to just read a sample report; the physical data, metal concentration and additive weight information is valuable for equipment integrity.
Q: What’s a normal work day like for you?
A: A normal day is 10-plus hours of scheduled lubrication tasks. These include critical lube checks, monitoring plant equipment, checking grease levels on automatic lube systems, looking for leaks, replacing injectors, taking equipment bearing temperatures with a temperature gun, pulling oil samples, changing breathers, and changing out gear reducer oil and kidney-loop filters. My lube room duties consist of cleaning, labeling, filtering and disposing of lubricants. I’m also involved in lubrication equipment design, installation and repair, as well as assisting our millwrights.
Q: What is the amount and range of equipment that you help service through lubrication/oil analysis tasks?
A: Seventy-five percent of our plant equipment is supported with oil analysis, beginning with the early stages of the coal-crushing process and ending with the loading and/or stocking of the product.
Q: On what lubrication-related projects are you currently working?
A: I am currently working to design centralized automatic lubrication for the plant’s belt transfer system, upgrading the hydraulic filtration on the train load-out system, and updating the coal-crushing equipment lube systems to reduce overgreasing on drive roll bearings.
Q: What have been some of the biggest project successes in which you’ve played a part?
A: I believe the greatest success is Cloud Peak Energy’s recognition and development of the asset management/plant reliability team, which is the driving force to raise the bar in best practices for plant lubrication.
Q: How does your company view machinery lubrication in terms of importance and overall business strategy?
A: The millwrights, supervisors, planners and managers all support lubrication as a key factor in the maintenance group.
Q: What do you see as some of the more important trends taking place in the lubrication and oil analysis field?
A: Oil analysis and lubrication are assisting the lube tech’s role in plant reliability to precisely diagnose and identify a machine’s integrity. We draw the blood and check the pulse, so to speak.
Q: What has made your company decide to put more emphasis on machinery lubrication?
A: The coal industry has challenges, just as any other energy-producing industry with machinery maintenance requirements. Cloud Peak Energy is a proactive leader in maintenance practices, and lubrication is of the highest priority for our machinery.
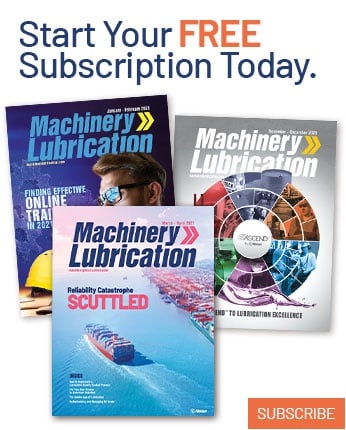