Imagine an operation in which there are no lost-time accidents, overall equipment effectiveness (OEE) is increasing, and there is a plan to address the skills shortage. These sites do exist, and chances are they’re using procedure-based maintenance.
This type of maintenance simply involves having all maintenance activities documented in a procedure. The procedures are followed step by step when conducting breakdown, corrective and preventive maintenance.
This level of operational excellence comes with discipline, not just discipline that deals with people doing what they should be doing (or not doing), but discipline to the process and eliminating variation.
That is the goal of procedure-based maintenance: to eliminate variation in all aspects of maintenance, including data collection, repairs, calibration and commissioning. Another goal of procedure-based maintenance is to eliminate and reduce the odds of mistakes by maintenance staff.
By ensuring that all activities are performed the same way, organizations can accomplish three key deliverables: build a knowledge library to survive the skills gap, identify key areas of variability and reduce that variability to achieve consistent outcomes from activities, and minimize the odds of a mistake during maintenance activities.
The use of procedures must be thought out well in advance. Without this thought-out approach, the adoption of the procedures will fail. The procedures need to be organized so they can be quickly located.
They must be written in a way so there is no misinterpretation of the task’s meaning and so non-native English speakers can understand. Lastly, they must be utilized by the staff, with feedback captured and used to improve them.
History of Procedures in Maintenance
The use of procedures can be traced back many decades, and the results speak for themselves. Consider the U.S.S. Thresher, which was lost along with 129 lives on April 10, 1963. An investigation into the loss of the submarine concluded that it was the result of flooding most likely caused by the failure of a seawater system component that may have been reinstalled improperly during a shipyard overhaul. There were additional factors, but the primary finding was that the component was reinstalled incorrectly.
The outcome of the investigation led to the U.S. Navy implementing a new program to address submarine safety. This program was known as “SubSafe.” The SubSafe program required detailed written procedures and checklists to be developed and followed to the letter by all personnel engaged in maintenance of specified components of all systems affecting submarine safety.
To date, the Navy has not lost a submarine due to a maintenance mistake under the SubSafe program. This shows the impact that a robust procedure-based maintenance program can have on reliability and safety.
Later in the 1960s, there was a focus on improving the reliability of commercial aircraft. This study, which was published by Nowlan and Heap, brought to light that most failures were not induced by time or wear but were either random or triggered by improper maintenance or installation. Looking at the six failure patterns, it was observed that failure pattern six, which experiences a high level of infant mortality followed by a random, consistent failure rate, was more prevalent at 68 percent.
This indicates that the highest probability of failure is when the equipment is new or just overhauled. So, what led to the spike in the probability of failure? The causes could be related to design, manufacturing defects, installation defects, improper commissioning, improper routine maintenance, and maintenance workmanship.
Considering the causes of the high probability of failure for new or recently overhauled equipment, it was determined that more maintenance was not the answer. The solution was related to controlling the variation in activities. These activities included such things as design reviews, supplier quality and certification programs, and the development of procedures for operating and maintaining equipment.
There was a conscious effort to move away from relying upon on-the-job training, intuition, etc., toward the use of detailed, technical procedures. As a result of these changes, along with the move to condition-based maintenance from time-based maintenance, worldwide aircraft incident rates have fallen from nearly 40 incidents per 1 million takeoffs in the early 1960s to just one or two incidents per 1 million takeoffs in 2016.
Importance of Procedures
Procedure-based maintenance serves to address two key issues when performing maintenance activities. First, it reduces the variation that occurs when many craftspeople are conducting the same work. Consider how many ways there are to rebuild a pump.
How does the disassembly happen? Does the disassembly occur with a precision torch and hammer, or does it take place with the proper tools? Does the rebuild happen in a clean room or in a dirty shop which can contribute to contamination? Are the parts inspected according to a standard or left to the experience of the rebuilder?
Is there a standard list of parts that are replaced, or is it left to the inspection? Is a thread-locking component used during reassembly? Are the clearances checked based on experience or technical specifications? Are fasteners tightened using a torque wrench or the strength of the rebuilder? How is the pump tested before being put back into stock or service?
If you were to ask a group of craftspeople these questions, you likely would get a wide range of answers, and two people would not have the same process for rebuilding and commissioning a pump. This variation makes it virtually impossible to establish a root cause of a premature failure or poor performance of a rebuilt pump. A procedure based on the experience of the staff can capture the collective knowledge and put it into a repeatable and consistent method, eliminating this variation.
Secondly, procedure-based maintenance minimizes the odds of an individual making a mistake. There are various types of factors that can contribute to an error, and it is important to understand these factors to ensure that procedures are written to address them.
For example, anthropometric factors are those related to the size or strength of the person performing the activity. These are primarily addressed through a redesign or tools and not with procedures.
Human sensory factors are those concerned with the ease in which people can see, hear, feel and even smell what is going on around them. These are also mainly addressed by redesigning or with tools and not through procedures.
Physiological factors refer to environmental stresses, such as high or low temperatures, excess noise, humidity, etc. Once again, these cannot be addressed through procedures.
Psychological factors are related to the causes of which mistakes are made. Psychological errors are divided into two types: unintended errors, which occur when someone does a task incorrectly, and intended errors, which happen when someone deliberately sets out to do something, but what they do is inappropriate.
The intended error can be either a mistake or violation. A mistake is a misapplication of a good rule, an application of a bad rule or an inappropriate response to an abnormal situation. A violation is when someone knowingly and deliberately commits an error. Procedures help to address unintended errors and mistakes but not violations.
By accounting for the different ways activities are performed, the types of mistakes made and utilizing a feedback cycle, procedure-based maintenance takes the knowledge from all the craftspeople and incorporates it into the procedure. The result is the safest, most efficient and reliable way to complete the task.
How Procedures Impact Reliability
Once procedure-based maintenance is in place, the operation will see noticeable improvements in five key areas: safety, reliability, start-up failures, mean time to repair and knowledge management.
Safety will improve as tasks are well planned out with the risks identified. This allows the development of effective risk-reduction activities. Also, the procedures can be used in the event of a failure, which can lower the risks associated with unplanned work.
Reliability will increase as tasks are completed consistently with proper technical specifications. This reduces premature failures. In the event a failure occurs, it can be analyzed to determine the root cause, since the procedures and activities are defined and consistent.
Start-up failures will decrease, as procedures will ensure that all bolts are tightened properly, the area is inspected, all foreign objects are removed, and proper commissioning activities are performed.
The mean time to repair will be reduced, as a procedure is available that will decrease the time to repair and all the required information is readily available.
Knowledge management is another benefit of procedure-based maintenance. With this approach, the experience and knowledge of veteran craftsmen can be captured in procedures and transferred to junior craftsmen.
Getting Started in Procedure-based Maintenance
Procedure-based maintenance is used by many industries that require high uptime, such as nuclear power, nuclear navy and aviation, to name a few. But just because these industries use it doesn’t mean you can’t. Here is what you need to get started in procedure-based maintenance:
Start by documenting the steps to complete preventive maintenance (PM) tasks. Walk through every task and document each step of the procedure, including any specific technical specifications. Once the procedure has been developed, review it and make sure it represents the best practice in completing the task. This may take many revisions or reviews. The procedure may be developed by a senior craftsperson, a planner or by having recent retirees come back to provide the information.
Create a checklist that can be used when completing the procedure. Checklists are employed in all major industries as a way to make certain that nothing is missed. There may be pushback in utilizing a checklist, as craftspeople may say they are skilled. However, doctors and pilots use them to ensure nothing is missed, so why shouldn’t craftspeople?
Define a training and certification program for the new procedures that will require craftspeople to be trained on the task and procedure-based maintenance before being allowed to perform critical activities. This training should be performed by the individual(s) responsible for developing the procedure.
Once the craftspeople have been trained, reinforce the use of the procedures. Conduct audits to verify that they are followed and that only trained personnel are using them. Try to reward those who embrace procedure-based maintenance.
Also, utilize the feedback provided on the procedures. This does not mean taking all feedback as absolute truth. Instead, it means reviewing, evaluating and either using the feedback or providing explanations as to why the feedback will not be used. This type of approach will help guarantee that feedback is provided.
As more maintenance tasks are converted to procedures, develop and use a single template. This will foster consistency across an organization, making procedure-based maintenance easier to put in place and sustain.
One caution when using craftspeople to write procedures is to first train them on the process. Procedures need to be specific and actionable without any unnecessary information. Another approach is to have a craftsperson write the procedure and then have it edited by a technical writer. Both approaches have their pros and cons, so be sure to choose the right one for your organization.
Writing Usable Procedures
Writing procedures is not an easy task. Many people have different opinions on the sequence, specifications, etc. Once this is sorted out, the procedure should be written in a way so it can be followed by all craftspeople, including non-native English speakers. Thankfully, with English being the universal language of aviation, we can continue to learn from the aviation industry. This industry has developed simplified, technical English.
Simplified, technical English is a controlled version of English that is designed to help the users of English-language maintenance documentation understand what they read. Technical writing can be complex and difficult to understand, even for native English speakers. Simplified, technical English makes procedures easy to understand and follow, eliminating language issues and reducing premature and maintenance-induced failures.
Simplified, technical English provides a set of writing rules and a dictionary of controlled vocabulary. The rules cover grammar and style. The dictionary specifies the words that can be used and those that can’t. For the words selected, there is only one word for one meaning, and one part of speech for one word.
Some of the benefits of simplified, technical English include reducing ambiguity, enhancing the clarity of technical writing, improving comprehension for people whose first language is not English, and increasing equipment reliability by lowering the probability of defects being introduced during maintenance and assembly.
The simplified, technical English specification is not easy to learn, but training and software are available. Even without becoming an expert, you can still make your procedures more readable and drive reliability. Begin with some basic writing guidelines and by reviewing the procedures before they are issued. Some of the best practices for writing procedures include the following:
- Use short sentences. The recommended maximum limit is 20 words in a procedural sentence and 25 words in a descriptive sentence.
- Restrict noun clusters to less than three nouns.
- Restrict paragraphs to less than six sentences.
- Avoid slang or jargon.
- Avoid the passive voice.
- Be as specific as possible.
- Use articles such as “a/an” and “the” wherever possible.
- Use simple verb tenses (past, present and future).
- Write sequential steps as separate sentences.
- Put commands first in warnings and cautions, with the exception of certain conditions.
- Use the word “that” after subordinate clauses that use verbs such as “make sure” and “show.”
- Introduce a list item with a dash (hyphen).
- Use graphics where needed to clarify meaning. A picture is worth a thousand words.
- Use the word "warning" to protect against harm to personnel but the word "caution" to protect against equipment damage.
Once the procedure is written, review and delete any information that is not relevant (i.e., instead of synthetic lubricating oil, use only oil). Well-written procedures should help to eliminate any misinterpretation and drive clarity to the craftsperson performing the activity. Here is an example of how the wording of a procedural step could be open to interpretation. The task “replace the filter” could mean either to put back the filter that you took out or to install a new filter.
Now you can see how one person might perform a task and how another would perform it differently. Once the task is clear, a technical specification should be added so the task can be performed to a standard, such as “Tighten to 15 foot-pounds.” The result of making the task clear and adding a specification would be, “Install a new filter and tighten to 15 foot-pounds.” This task is simple, clear, easy to understand and can be performed in a consistent and repeatable manner.
If an organization decides not to follow simplified, technical English, there at least should be a standard in place for writing procedures so everyone is doing it the same way. Although it may sound crazy to have a procedure for writing a procedure, it is vital for consistency and repeatability.
Having Staff Use Procedures
One of the most difficult parts of implementing procedure-based maintenance is the change it brings to an organization. Indeed, there will be a change in the way maintenance is performed for all levels of the maintenance department. For example, craftspeople must follow procedures and specifications and rely less on personal experience and intuition.
Maintenance supervisors are now focused on ensuring the procedures are used and updated. Planners become more determined to update the procedures so they are readily available for use.
Helping an organization through this change is not easy. It will require a well-thought-out approach. I personally like to use the awareness, desire, knowledge, ability and reinforcement (ADKAR) framework. This method enables organizations to plan and manage the change being implemented as well as bring people along with the change.
Each step in the framework provides specific actions that should be taken, such as awareness of the need for change, desire to participate and support the change, knowledge of how to change, ability to implement required skills and behaviors, and reinforcement to sustain the change.
The whole purpose of using a framework like ADKAR is to identify any concerns associated with the change, address those concerns, express how the change will benefit the staff, provide the knowledge and training, and finally demonstrate that the change is not a flavor of the month. The more time spent planning and managing the change, the more likely the change will be adopted and sustained.
Procedure-based maintenance has the opportunity to drive significant improvements in safety, reliability and operations. But before an organization can jump into procedure-based maintenance, there must be a plan for how it will be implemented, who will write the procedures, to what standard the procedures will be written and how the staff will be trained on the new procedures.
With procedure-based maintenance having been adopted by the U.S. Navy, aviation and nuclear power industries, the results have been proven. If these types of organizations are using procedure-based maintenance, what is preventing your organization from using it?
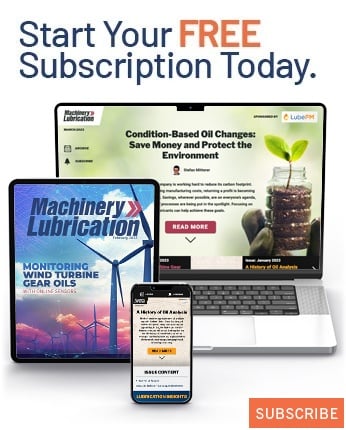