"Can you explain the difference between anti-wear (AW) and extreme-pressure (EP) additives?"
Additives are selected based on their ability to perform certain roles alongside a base oil in an application. By nature, additives either enhance new properties, suppress undesirable properties or impart completely new properties to the base oil. Additive packages typically make up to 30 percent of the formulated oil volume depending on the application.
Wear and friction control additives are among the most commonly utilized packages and generally come in the form of either anti-wear (AW) or extreme-pressure (EP) additives. These packages form large, chemically reactive groups that work to shield metal surfaces during mixed-film and boundary-film lubrication. If full-fluid-film lubrication is maintained, they may not be activated.
However, once crowning surface asperities begin to initiate contact, they become sacrificial in nature, providing the sought-after protection for the active surfaces. This occurs until they become exhausted, at which point surface degradation begins to transpire.
While anti-wear and extreme-pressure additives are often grouped under the same friction and wear control umbrella, there are noteworthy differences between the two functioning packages.
Anti-wear additives are used to protect against wear and the loss of metal surfaces during mixed-film and boundary-film lubrication. This package is triggered by temperature or elevated loads at the contact surfaces. It works to form a protective film to minimize wear.
During this transaction, the additives chemically react with the metal surfaces to protect the surfaces from wear, corrosive acids and oxidation of the base oil. The chemical composition of these additives is typically based from zinc and phosphorus compounds, often in the form of zinc dialkyldithiophosphate (ZDDP).
These additives are usually employed in hydraulic oils, engine oils, gear oils, automatic transmission fluids and some greases.
Extreme-pressure additives normally are stronger and more chemically aggressive than anti-wear additives. They are employed by the adsorption of surface-active materials. This additive package is activated through high loads but can also be temperature and non-temperature related.
Temperature-related additives include boron, chlorine, phosphorus and sulfur elements, while non-temperature-related additives fall into the overbased sulfates category.
There are even a few solid-suspension films that act as EP additives. These generally come in the form of graphite or molybdenum disulfide. This type of additive is most frequently present in the form of sulfur phosphorus, which is utilized in gear oils, excluding worm gears.
In conclusion, the main differences to note between AW and EP additives would include how they are activated and the type of application in which they are utilized.
While anti-wear additives chemically react with the surface to form a low-shear-strength film, extreme-pressure additives adsorb to the surface of the material. In addition, anti-wear additives are almost always formed from a temperature increase created due to load.
On the other hand, extreme-pressure additives can often be activated through non-temperature-related processes. Anti-wear packages are also much more common across different types of oil applications.
However, you normally would only find extreme-pressure additives in transmission fluids and gear oils, specifically non-worm gear oils due to their aggressive nature toward yellow metals.
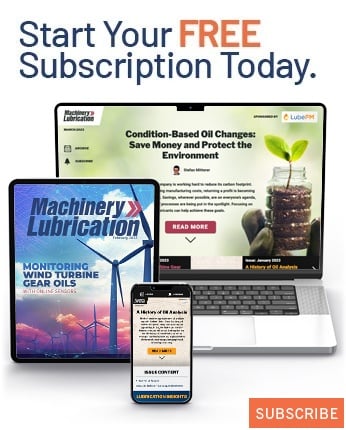