Name: Ricardo Peruchi
Age: 39
Job Title: Reliability Manager
Company: Gerdau
Location: Jacksonville, Florida
Length of Service: 14 years
Lubrication has been a priority for Ricardo Peruchi since 2004 when he began studying why scrap-processing equipment was failing prematurely. Peruchi discovered the main reasons for these failures were basic things like lubrication.
For the past 14 years, he has worked for Gerdau, starting as a management associate at a scrapyard in Brazil. After serving as a reliability engineer for the company’s steel mill in Rio de Janeiro, Peruchi was transferred internationally to another mill in Petersburg, Virginia.
In 2013, he moved to the Gerdau steel mill in Jacksonville, Florida, where he now serves as reliability manager, leading a team of reliability technicians, maintenance planners, fleet managers and mechanics.
Q: What types of training have you taken to get to your current position?
A: I have had both leadership and technical training. My leadership and management training were focused on teamwork, how to approach people, how to deal with and encourage teams, time management and Six Sigma. My technical training covered lubrication, oil analysis, vibration analysis, ultrasound, infrared inspections, hydraulics and transformers.
Q: What professional certifications have you attained?
A: I have Level I Machine Lubrication Technician (MLT I), Certified Reliability Leader (CRL), Category I Vibration Analysis, Level I Ultrasound and Six Sigma certifications.
Q: What’s a normal work day like for you?
A: I would be managing the planning and scheduling process with our maintenance planners, as well as the predictive maintenance program with our predictive technicians and reliability engineer. I also support analysis and manage the mobile equipment fleet.
Q: What is the amount and range of equipment that you help service through lubrication/oil analysis tasks?
A: We service all the rotating equipment for both the melt shop and rolling mill areas along with the critical hydraulic systems, lubrication systems and transformers in the plant. For lubrication based on time, we have more than 300 pieces of equipment, which have more than 20 lubrication points in some cases. In January 2018, we introduced acoustic lubrication in some of the most critical pieces of equipment, as we know it is a more efficient methodology. For fluid analysis, we manage more than 70 pieces of critical equipment each month.
Q: On what lubrication-related projects are you currently working?
A: Currently, I’m working on a project to reduce hydraulic fluid consumption in the rolling mill.
Q: What have been some of the biggest project successes in which you’ve played a part?
A: I’d say the successful implementation of the Gerdau Business System (GBS) at the steel mill in Petersburg, Virginia, as well as the SAP implementation project for Gerdau North America.
Q: How does your company view machinery lubrication in terms of importance and overall business strategy?
A: It’s growing each day. Safety is our No. 1 priority. There is no dirty or oily place that is safe and free of accidents, so we need to improve our equipment reliability and working conditions to reduce the number of accidents. Newer equipment is faster and more precise, but it also has tighter tolerances for mistakes. Therefore, we must have cleaner fluid and precision lubrication. Additionally, environmental laws are stricter, requiring cleaner plants, contingency plans, etc.
Q: What do you see as some of the more important trends taking place in the lubrication and oil analysis field?
A: Online oil analysis monitoring is increasing just like online vibration analysis.
Q: What has made your company decide to put more emphasis on machinery lubrication?
A: Gerdau has placed an emphasis on lubrication in order to achieve a cleaner and sustainable environment, a safer place to work, cost reductions, and equipment availability.
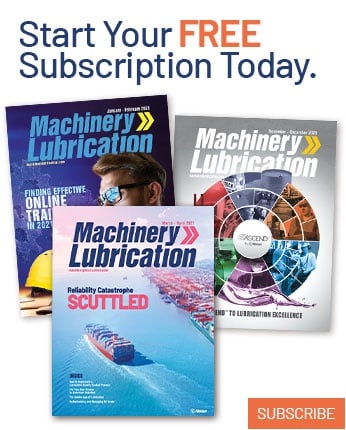