While assisting many different organizations in implementing lubrication and oil analysis best practices, Noria has identified a few common approaches for companies aiming to achieve a world-class lube program. This article will share some of the insights that have been learned through the years to help you select the best strategy for your plant.
Short-Term Initiative
The first approach is when top management has been convinced that there is value in implementing a reliability initiative with lubrication and oil analysis as key elements. Previously, lubrication tasks may have been considered dirty or less important work, but now they have become more valued in both operational and financial terms, and for that reason deserve attention. It also is understood that investments in equipment reliability will pay back the organization in a relatively short period of time, so it will be beneficial to allocate a budget and invest in the initiative.
The program generally begins with an assessment to determine where the company is in terms of its current practices compared to best practices along with the goals. A financial assessment may be included to offer a better idea of the gains the organization is seeking. This type of assessment reports the current situation with a holistic perspective while making it clear that a lubrication program involves multiple organizational levels. Success will depend on the combined work of the team or department involved in the financial decisions and operations, as well as the execution of the maintenance and reliability programs.
The chosen team, which is formed from different levels of the organization, should establish the plan, goals and milestones, and allocate resources. They should know that at times many initiatives will be happening at the same time and that unexpected situations may arise, but they must focus on the goal and understand its relevance.
The second step consists of defining the technical parameters to be followed, such as designing a program for lubricant selection, preventing lubricant contamination, selecting training programs for team members, creating new procedures, identifying key performance indicators (KPIs), and establishing a rewards program.
Key connections may be made across the program. For example, machine modifications can help improve visual inspections and consequently contamination control and lubrication practices. Better oil sampling procedures may enhance the quality of oil analysis and machine condition diagnosis. Machine modifications may be supported by better written procedures and training, which also contribute to improved team performance, increased machine reliability and a reduced failure rate.
The next step is to implement everything that has been carefully planned and designed. This includes installing machine modifications, improving lubricant management across the facility, providing the necessary training, employing and reporting KPIs to observe improvements in machine reliability, etc.
One element that should not be overlooked is defining a specific mechanism for managing change in the organization. This will help to ensure everyone involved in the program contributes to sustainable changes.
Periodic reviews can show the progress of the initiative. The results may be expressed in different ways, such as a reduction in operational costs, fewer unexpected shutdowns, lower component/machine replacement rates, decreased labor costs, optimized lubricant purchases and stock control. As long as the project continues, more involvement by the team should be expected along with greater satisfaction from the work.
Successful implementation of best practices will consider the technological, organizational and human factors related to the project. These principles apply not only to lubrication programs but also to other maintenance strategies as well. This type of approach demands top management support, allocation of resources, teamwork, focus and persistence. While it may take several months or longer, eventually the rewards will come.
This illustration depicts the different paths of a
long-term (blue line) and short-term (orange line)
approach to achieving lubrication excellence.
Long-Term Improvement
Although the short-term approach sounds great, some plants may not have the necessary resources available. In these situations, the reliability/maintenance group might choose a different strategy, one that isn’t as demanding on resources but still feasible for implementing best or better practices. This would involve allocating fewer resources in terms of time, labor and money, and would not require much support from upper management. Described as a continuous improvement initiative, it will take a longer time to achieve the desired conditions, but it may be perceived as the best option for attaining lubrication excellence.
In this scenario, top management may not provide formal support of the initiative or even be fully aware of the plan. The authorized budget for the lubrication program might be limited. Due to the restricted resources, a full assessment of the program may not be conducted. Consequently, there likely is not a holistic vision of the improvement opportunities and their potential impact. Instead, the focus is on more tangible or evident conditions, which can result in important program elements being missed.
Solutions often are deployed randomly based on the available resources or ease of implementation, with the steps not necessarily completed in the ideal sequence or timeframe. For example, improvements might include acquiring filter carts, installing high-quality breathers or providing formal training for a few team members. Other changes are made according to the available resources (time, money, machine availability, etc.).
The success of the initiative primarily will depend on the involvement and persistence of one or a few members of the reliability/maintenance team. Since a long-term path has not been defined, only short-term steps are taken. Achievements are celebrated when a step is completed.
With this approach, it will be difficult to estimate the amount of time required to achieve lubrication excellence, as it will be contingent on the available resources. Also causing a blurry vision of the future is that the lubrication program may not be viewed as a system of interconnected factors that produce equipment reliability benefits. This can dilute the impact of the efforts taken. While benefits will be seen, they may take longer to be realized.
Milestones and time-based goals may be incomplete or non-existent, as there likely is no formal metric system. If less favorable conditions are present, the length of time for the implementation could be indefinite. Even after years of work, the results tend to be limited. While this risk exists with any project, the longer it takes for change to be made, the more chances it has to be diluted over time unless there is a culture of formal support.
Although a long-term improvement initiative generally is full of good intentions and hard work, the benefits are more difficult to achieve and typically take longer. Eventually, the team may become frustrated. As with any long-term project, persistence will be key. With all things considered, this may not be the best approach to reach the desired goal.
The illustration above shows the path of both approaches. The orange line represents a short-term project with focus, vision of future goals, milestones and support from upper management. The blue line characterizes a long-term continuous improvement initiative with an unclear vision of the goals and future status of the program, which typically requires more energy and time to reach the desired destination.
If you find that your program is somewhere in between these two approaches, keep in mind that the more attributes it has of the short-term approach, the more chances it will have to make an impact on your plant’s equipment reliability.
Suggestions for a Successful Implementation
Following are suggestions for successfully implementing lubrication excellence, particularly if your current program is more like the long-term approach. Start with quality training for both those responsible to make the improvements and for the team that will support the initiative. This will open eyes and create awareness of the possibilities and benefits. Remember, training is fundamental to ensure appropriate attitudes, behaviors and reliable work.
Next, make a list of improvement actions to be completed and their potential benefits. Involve management as much as possible by sharing case studies, presenting your plans and needed resources, and providing evidence of good work performed.
Develop a plan and communicate the potential value, which is the justification for your actions. Do not allow changes to just be verbally implemented. Make every effort to guarantee that the initiative will prevail by modifying procedures, work orders, etc.
Recognize and reward the contributions of others when a better idea is executed or implemented. Finally, do not stop. Be persistent and communicate the results.
3 Key Factors for Lubrication Excellence
To achieve lubrication excellence, you must take into account three key factors: training, infrastructure/tools and methodology. Training creates awareness of the proper work to be completed, while the infrastructure and tools involve the physical resources that provide the environment and hardware to perform the job. The methodology is the procedural element that must be executed in a consistent, effective and ergonomic manner. If only one or two of these three factors are implemented, some improvements may occur, but the chances of overall program success are low. For instance, new procedures may be written and distributed, but if poor or no training is made available to personnel and no new tools or hardware are provided, the result will be a less than desirable outcome.
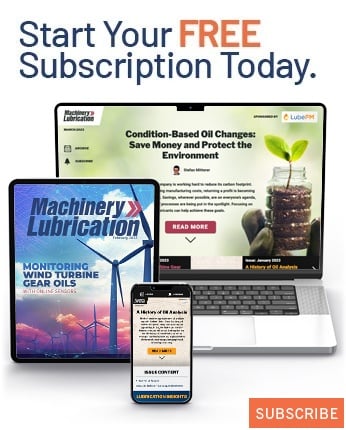