“We are in the process of trying to achieve a world-class lubrication program. What are the training requirements for this type of program?”
Every training program should be focused on providing the knowledge and skills to perform the required tasks properly, safely and in an ergonomic manner. The training requirements must be identified for all levels of the organization but especially for those individuals whose roles impact the lubrication program’s effectiveness and continuous improvement.
These requirements can be mapped out horizontally based on the various functions and processes in the facility as well as vertically according to the different organizational levels. The “horizontal” requirements should cover all necessary tasks for effective management of the program, from the time the lubricant is received until the end of its use and disposal. This would include both lubricant selection and consolidation to guarantee the correct product, quality and number of lubricants are used in the facility.
To help preserve cleanliness and integrity, lubricant reception and storage must be considered, along with lubricant identification, stock control, personnel safety and environmental protection. Other key training elements will involve transferring lubricant to the machine, in-service lubricant administration, and monitoring both the machine and lubricant.
In addition, do not overlook the management of lubrication routes and tasks or the design and execution of the oil analysis program, which should identify the training requirements for oil sampling, oil analysis report interpretation and failure investigation.
Training should also encompass lubricant decontamination, reuse and disposal, as well as the appropriate corrective and proactive actions to take whenever an abnormality is observed, such as a machine failure, an uncompleted lubrication task, a missing lubricant, etc.
To include all levels of the organization, “vertical” training requirements must also be specified. These should consist of awareness training for higher level executives in the organization so they can make the best decisions and provide resources for the program’s implementation and continuous improvement.
The program manager and reliability leaders should also have advanced knowledge to administrate the program effectively and be able to offer the necessary technical expertise when required. For personnel who perform the daily lubrication routines, task-based training should help to enable the proper execution of all tasks.
Finally, when designing and implementing a formal training program, be sure specific learning expectations are addressed for every individual involved in the program.
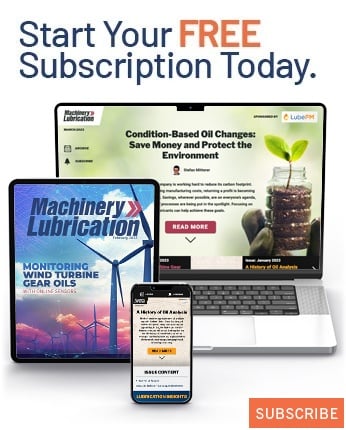