“What could changes in the oil level indicate?”
The oil level is one of the most basic inspections. If a low oil level persists, friction, heat and boundary conditions may result. On the other hand, if the level is too high, it might cause fluid friction, excess heat and oxidation. Following are a few key factors that could lead to an increasing or decreasing oil level in a sump or reservoir.
Leaks
Leaks generally are the primary concern with fluctuating oil levels. An oil leak often becomes evident during an inspection through a decrease in the oil level or pressure. If the level gauge, sight glass or pressure gauge reveals a decrease in the oil level, immediate action should be taken to identify not only the location of the leak but also its size and severity. If a long-term fix is required, the best time to address a leak in a lubrication system may be during a turnaround or outage.
Leaks often recur on the same equipment repeatedly over time and can be easily spotted by the presence of saturated mats placed below the source of the leak. If this sounds like your site, it may be time to address the issue. Individuals who perform oil level inspections should understand which assets are prone to leaks, which machines have recently been worked on and how critical a leak is.
Vaporization
Another less likely cause for concern with a decrease in the oil level may be vaporization. This process can occur in high-temperature applications where less-dense hydrocarbons disperse, resulting in a change in the viscosity and oil level. If this issue is noted through laboratory or in-field oil analysis, good communication will be essential between the individuals performing the inspections and those reviewing the oil analysis reports, especially during shift turnovers, lubrication meetings and work order documentation.
Improper Filling Practices
While a low oil level is the main worry with sumps and reservoirs, a level that is too high can be concerning as well. Improper refilling practices can lead to excess lubricant in the system and fluid friction. If this is not addressed, it may result in oxidation over time. Poor filling practices can also cause boundary conditions if the oil level is too low. Therefore, it is important to review and understand the practices being used at your facility. Have all level indicators been properly marked? Is there a preventive maintenance task or work order to check their status on a yearly basis? Is there documentation for in-field refilling practices? If the filling practices at your site are inadequate, you must take the necessary steps to correct them.
Contamination
One final consideration for an increasing oil level is contamination. Moisture ingression, cooler and seal leaks, process chemicals, and even cross-contamination can all lead to an increase in the oil level. Contamination can be difficult to identify exclusively in the field, so good communication between in-field inspectors and those individuals reviewing the oil analysis reports will again be critical.
Know the Correct Oil Level
Understanding the correct oil level and the possible causes for why the level may be too high or low can help you determine the current status of your assets. To gain this knowledge, ensure your plant uses proper inspection hardware, employs effective communication, and is trained to observe and examine the equipment.
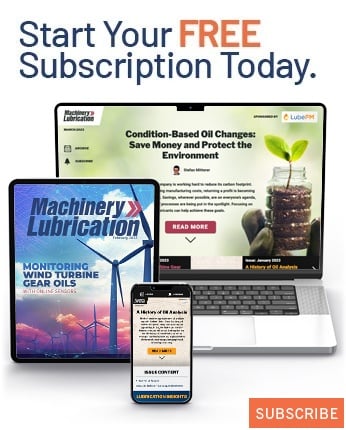