“Can you explain how solid-film lubrication works and the different types?”
Under preferred lubrication conditions, the viscometric properties of a lubricant, which are provided primarily by the base oil, create a film thickness to fully separate machine surfaces in relative motion. Of course, in most mechanical interactions, some degree of boundary conditions will exist. In other words, surfaces with too much load and not enough relative speed will not allow a sufficient film thickness to develop, and the machine surfaces will abrasively interact. In these circumstances, friction and wear-control additives are used to impart a film strength for a different type of protection at the surface level. These include chemical additives such as anti-wear and anti-scuff (extreme-pressure) additives.
When loads are high and/or the relative motion of sliding surfaces is very low, solid additives can offer an advantage by providing an advanced type of extreme condition protection. These solid additives often are selected when there are low start-up friction requirements for precision mechanical movements.
Each type of solid additive works somewhat differently. Additives such as graphic or molybdenum disulfide are comprised of inorganic compounds with molecular structures that adhere to machine surfaces. These structures form layered lattices which allow sliding to occur more easily between each other. These layers are devised of strong molecular bonds within each layer but weaker van der Waals forces between the layers, which result in slip planes.
Other factors, such as water vapor content and temperature, may play a role as well. Ultimately, solid additives eliminate the potential frictional interactions of machines surfaces and encourage relative motion to take place at the slip plane of the additive structures.
Other types of solid additives include polytetrafluoroethylene (PTFE) and borate. PTFE, which is commonly known as Teflon, is a white, long-chain fluorocarbon. It is extremely resistant to wetting with a very low coefficient of friction. Borate is comprised of tiny solid spheres that roll easily and adhere readily to machine surfaces from electrical forces.
While these solid additives are potential components in the formulation of a liquid lubricant, many can be effective independently as a dry powder lubricant. If formulated within a liquid lubricant, the concentration of the solid additive and base oil must be carefully selected to maintain a homogenous dispersion.
Solid additives can offer a unique advantage when extreme pressure and low hydrodynamic load-carrying conditions exist. For example, gear drives with high loads and low speeds are some of the most common applications for solid additives.
However, the benefits of solid additives are not limited to high pressure. They also can be used to counteract the effects of high-temperature applications or environmental contaminants, such as those that lead to chemical attacks and three-body abrasion. Remember, in the right conditions, solid additives can help minimize the impact of boundary conditions and support longer machine life.
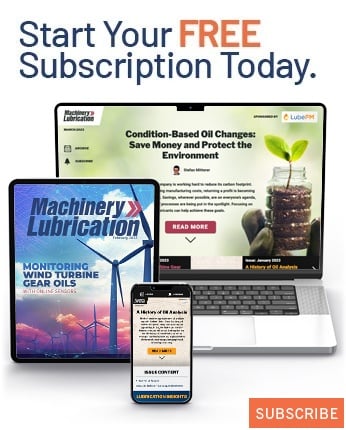