Many organizations aspire to achieve the state of lubrication excellence. This is indeed a lofty goal, but not beyond the reach of a focused and determined team. What defines lubrication excellence has not always been clear until Noria gave rise to the Ascend™ methodology. Its application and purpose go beyond mere definition. It has become a powerful tool and metric to evaluate, design, implement and control the essence of the lubrication excellence transformation. Ascendtm is the North Star that illuminates the guiding path that gets us there.
Identifying the starting point on the journey to lubrication excellence always requires evaluating current practices to contrast with lubrication best practices, which Noria calls the Optimum Reference State (ORS). Once the gap is identified, it is necessary to establish an optimal road map that ensures that resources, effort and time are allocated to targeted initiatives that produce the highest return on investment.
This requires prioritization based on lubricant lifecycle logic and the impact of improvements on machine reliability and other organizational objectives. Once the process is started, it is necessary to measure progress, continue the transformation plan, identify deviations, and ensure that improvements are sustainable.
Ascend™ is a necessary evolutionary advancement over the conventional radar chart (or spider chart) that for years was considered a standard to evaluate the lubrication process. By incorporating this new approach across the lubricant lifecycle, alignment with the requirements of the ISO 55001 and ICML 55.1 standards can also be achieved. Additionally, it responds to business objectives of many users who want to implement a lubrication program that enables superior plant reliability.
The Ascend methodology is backed by years of proven field experience, attention to the needs of industry, alignment with lubrication practices, and international asset management standards. Finally, it is driven to execution by our genome of innovation and continuous improvement.
Lubrication Lifecycle Stages
Ascend uses six lifecycle stages that follow in chronological order: selection, reception, application, management, analysis and disposal. It integrates the importance of each of these stages and the impact they impart on lubrication excellence, machine reliability and asset management.
Following the lubricant life cycle, for the first time, allows users to correlate their day-to-day activities at each stage with fundamental business objectives and how each stage functions individually as a part of the whole in executing correct principles of lubrication.
Ascend underscores the importance of selecting the right lubricant, with performance specific to the requirements of the machine and its operational context. But it doesn’t stop there. It also needs to arrive in the correct condition, be stored in the correct way, be applied to the machinery in the right place and at the correct frequency. Precision lubrication also includes application of the correct amount, with the right tools, by a person with the right knowledge and skills. Lastly, there is a fundamental need for contamination control of lubricants and using lubricant analysis as a metric on the state of lubrication and overall machine health.
The life cycle stages are shown as angular wedges on the Ascend chart:
- Lubricant selection (S)
- Lubricant reception and storage (R)
- Lubricant handling and application (H)
- Contamination control and lubricant reconditioning (C)
- Condition monitoring, lubricant analysis and troubleshooting (A)
- Energy conservation, health and the environment (E)
Factors and Management Levels
In the Ascend methodology™, lubrication activities across the lifecycle of the lubrication process are divided into 40 Factors (see Table 1. Ascend Factors). Each of these factors is interrelated to one or more of the 12 areas of the lubrication plan as specified in clause 5.0 of the standard ICML 55.1 Asset Management Requirements for the Optimized Lubrication of Mechanical Physical Assets.
However, it should be noted that these 40 factors do not all share the same weight in design and implementation of the lubrication strategy. Therefore, to emphasize and clarify these differences, the factors are arranged into three levels (See Figure 1):
- Platform (P)
- Management and Training (M)
- Performance Indicators (K)
Platform factors are considered the foundation of the program and are aimed at controlling risks, ensuring performance and sustaining the program over a long span of time. These factors are tactical and as such need to be implemented first.
Management and Training factors are activities that enable the needed resources, provide planning and scheduling and deliver condition monitoring of lubricants and machines. At this level, staff education and skills development activities are included. These are the day-to-day lubrication activities that are supported by all platform factors. The Key Performance Indicators (KPIs) level is the one that allows measurement of efficiency and effectiveness of the activities in a lubrication program and continuous improvement thereafter.
Each factor has been assigned an alphanumeric code for convenient identification. The code has been developed using three digits: the first refers to the Lubrication Lifecycle Stage, the second is the factor number within the stage and the third denotes the Management level. For example, the S3P element is the third Factor in Lubricant Selection Stage and is located at the Platform level.
Figure 2 Three levels of Ascend™
Using Ascend to Track the Transformation
The Ascend™ methodology uses Six Sigma's DMAIC (Define, Measure, Analyze, Improve and Control) tool to assess the maturity of the lubrication program from an established starting point through the transformation plan. The Optimum Reference State is defined based on the requirements of the ICML 55.1 standard. ORS compliance is assessed through inspections, measurement, verification and interviews.
Differences between required ORS performance and current performance are analyzed by the Ascend methodology to prioritize the implementation plan based on impact on business objectives and reliability. In the assessment phase, Ascend not only provides the maturity of each factor based on the degree of compliance (completeness) but also provides a list of specific improvements aimed at complying with the ORS in each of the 40 factors of the lubrication process. It identifies the critical actions needed to ensure that the process is sustainably implemented with suitable controls.
The maturity of the lubrication process factors is assigned by Ascend using the traffic light code, where compliance less than 30% is assigned a red color, compliance between 30 and 90% is assigned a yellow color, and factors that meet the ORS by 90% or more are assigned a green color. (see Table 2. Maturity of the Ascend Factors).
The Global Compliance level of Ascend (ACL) is a holistic indicator of maturity of the lubrication program in general. The ACL is not the average maturity of the 40 factors, but a sophisticated calculation based on a proprietary mathematical algorithm that includes a Balanced Score Card (BSC) of the lubrication process and the maturity of each of the factors. The active ACL value is displayed in the center of the Ascend Chart.
The Ascend Chart
As seen in Figure 3, the Ascend methodology is represented by a Chart consisting of the six stages of the lubrication process life cycle and the three management levels which also shows the degree of maturity and compliance with ICML 55.1
Implementation Priority and Execution Plan
The Ascend™ Chart naturally provides an intuitive way of implementation based on the maturity of the factors at the different levels, but also has a built-in mathematical algorithm based on the Balanced Score Card (BSC) of the lubrication process, the sequence and relative weight of each factor and its degree of maturity identified in the assessment, to calculate the Priority Impact Number (PIN). The PIN is an excellent aid in establishing the transformation road map by determining which factors should be implemented first, based on lifecycle logic, their contribution to business objectives, and plant reliability.
The Business Case for Ascend
The implementation of lubrication excellence is supported by numerous real world case studies that have been published in Machinery Lubrication magazine. However, a successful case study requires that each process step is validated based on the investments made relative to financial returns within a designated timeframe.
The Assessment Phase of Ascend™ explores the costs of the lubrication program and estimates the effect of current lubrication practices on maintenance budgets, operating budgets and overall productivity. This seeks to identify the financial impact represented by current lubrication practices and is part of the cost-benefit analysis that must be made to justify the investments required to implement lubrication excellence. Project financial analysis tools are used and reported such as Internal Rate of Return (IRR), Net Present Value (NPV) and Payback Period (PP). These tools develop the business case to present to management as part of the project approval process.
Such a proactive approach to lubrication excellence implementation makes these improvement projects less risky and easier to justify necessary investments.
Lubrication Excellence Transformation
Each improvement implemented under the guidance of the initial Ascend evaluation report contributes to ORS compliance and a change in Factor maturity. Ascend™ has built-in simulation tools that show the result of individual initiatives to improve the maturity of each Factor in the ACL global compliance indicator.
Whether using the PIN or the simple logic of Ascend, the process of transformation towards excellence in lubrication should be directed to improve those priority factors immediately, concentrating the efforts on the red and yellow elements located in the Platform level. By identifying priorities, improvement projects can be targeted at a few factors at a time, allowing for better distribution of resources and measuring the start and end of each improvement project. In many cases, these mini-projects can bring economic benefits and increased reliability that will serve to give credibility to the project, build trust in the team and support the implementation of the rest of the project.
Some organizations that are aware of the importance of lubrication of excellence may elect to embrace a global lubrication process transformation project and achieve benefits in a shorter timeframe. If this is the case, years of proven experience allow us to support the industry in the process of implementing lubrication excellence through sophisticated tools, software and specific recommendations to execute a project along the shortest path without deviations or distractions.
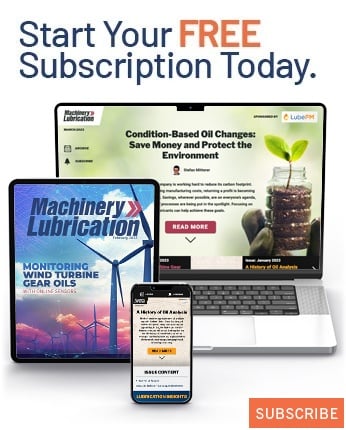