Myopia is a condition in which the eye fails to refract, bend and focus light properly, causing distant objects to be blurry or unclear. The familiar term, short-sightedness, accurately describes a condition that is common in industrial plants across the globe: Misguided Machinery Configuration (H2P). Many industrial facilities remain stubbornly short-sighted about the acquisition, installation, and operation of their machines. So today I want to take a moment to help you look ahead to the future of your machines.
Machines are designed to play a multitude of roles in different operational contexts. Equipment manufacturers can only customize their machines’ configuration options as much as market demand allows. Ultimately, it is the responsibility of equipment owners themselves to re-configure their machines to correlate to the specified operational contexts where they are used. While this step is commonly overlooked in the acquisition process, proper initial machine configuration prior to operation creates opportunities for simpler preventive maintenance tasks, improved inspections, increased equipment longevity and enhanced site profitability. Understanding asset lifecycle cost and ownership, standardizing and optimizing machine configuration through documentation practices and knowing how to deploy these considerations to assets in an accurate and timely way will provide improved site “vision.”
Understanding Asset Lifecycle Costs and Ownership
Cost control measures are a healthy part of physical plant asset acquisition. They help minimize capital spending on projects by ensuring there is a sound business case that maximizes ROI (Return on Investment). Despite this laser-focused efficiency, often a focus on immediate costs supersedes a broader, more strategic view of the situation. The extreme focus on the cost of a project is often based on the initial purchase cost alone - not on the entire lifecycle cost of the asset itself. In turn, this restricted view of asset costs often places plant equipment and productivity in a reactive mindset prior to installation or operation. A reactive approach might seem easier or cheaper in the short term, but it is a more labor-intensive, expensive and failure-prone way to manage the full lifecycle of your assets.
While short-term reduced spending in the form of capital projects looks good in the moment, reliability leaders should be focused not only on investing in themselves and their current situation, but their overall career longevity and the continued success of the plant as well.
Properly understanding the long-term vision of asset ownership prior to acquisition allows for correct enhancement where necessary before operation. Rather than waiting to outfit equipment during associated scheduled downtime, specific machine inspections and Preventive Maintenance (PM) tasks can be carried out ahead of time in a more detailed, less time-intensive manner.
Standardizing and Optimizing Machine Configuration Through Documented Practices
Properly addressing Machinery Configuration (H2P) at your site should begin prior to the acquisition stage. EEM (Early Equipment Maintenance) within the realm of TPM (Total Productive Maintenance), FMEA (Failure Modes and Effects Analysis) strategies and a MOC (Management of Change) process should be implemented to standardize and enhance asset configuration based on reliability, safety and ergonomics. While this level of practice should be the standard, it is rarely the case.
Establishing processes like the ones noted above and creating the correct documentation and standardized practices with the ORS (Optimum Reference State) in a lubrication standards manual can work as a failsafe, improving reliability upon initial operation of the equipment on the plant floor. Some may be unfamiliar with the intricacies of utilizing ORS, but to put it simply: ORS is the prescribed state of Machinery Configuration (H2P), conditions, and maintenance activities required to not only achieve, but also sustain reliability objectives set forth by the site or company. Regarding machine configuration in ORS from a lubrication standpoint, this speaks to the transformation of equipment regarding the specific lubricants, contaminant removal and exclusion options and associated hardware included on the asset to aid in maintaining it while avoiding sub-optimal or excessive states of deviation.
Accurately and Timely Deploying Configuration Consideration to Assets
As already mentioned, due to its level of importance, having a sound comprehension of what is really involved within asset optimization on the front end will pay dividends during production. As such, it is imperative to discuss in some detail the possible, viable options with regards to this pre-implementation transformational process regarding lubrication.
Lubricant selection is a good starting point for lubrication-related Machinery Configuration (H2P) concerns. Ensuring the correct oil or grease is being used can be a first line of defense for preventing friction, heat and wear in the asset. OEM recommendations are generally a great starting point, but consideration must be taken to understand how temperature, contaminant ingression, industry, and your specific application should be addressed as well. Some applications may require an amendment from standard mineral base stocks, additive packages or grease thickeners depending on the nature of the ORS for that specific function. Following this process, a review of the current lubricants on site should take place to see if there is already a functional lubricant available to fulfill the need of the asset that will also aid in lubricant consolidation efforts at the site.
Another machine configuration area to consider is contaminant exclusion and removal options available to help meet the asset’s contamination control objectives. Understanding the asset’s criticality, associated rebuild labor constraints, replacement part costs and lead time will play a pivotal role. Certain oil-lubricated assets in the plant will require dedicated, machine specific supply, return line, and possibly offline kidney loop filtration systems. Others may need dry instrument air purge systems with high end breathers to ensure proper contamination objectives are being met. Other less essential oil - lubricated assets may suffice with any OEM standards already in place. There should be a similar amount of attention to detail regarding grease-lubricated assets, especially when reviewing bearing structure and other grease-related applications.
One final consideration regarding early machine configuration is the lubrication-associated hardware outfitted on the asset. These deliberations need to consider headspace management tools such as desiccant breathers, particle breathers, expansion chambers, dry instrument air purge and vent plug options. Oil level management apparatuses such as bullseyes, level gauges, dipsticks, level plugs and constant-level oilers need to be evaluated. Bottom-drain management options worth considering include BS&W (Bottom Sediment & Water) bowls, magnetic plugs, ball valves and quick disconnects. Expanded metal guards on sheaves and couplings as well as diffuser or baffle plates that mitigate the concern for air entrainment and foaming should be considered as well. The option for oil-sample management and standardized location selection must be considered in advance, especially knowing the ramifications of poor sampling practices, false positives and variability concerns. Finally, grease supply and delivery management in the form of fittings, nipples, grease line extensions and auto lubricators should be considered as well.
All these important lubrication-specific options play a fundamental role in asset lifecycle management and can be directly related to improved inspections, PM task completion and asset uptime. The amount of time, money and attention that is spent on each one should be directly correlated to the ORS of the asset in consideration.
Wrapping Things Up
By now, it should be abundantly clear that there is often a need for the pre-configuration of plant machinery to correlate to the specified operational contexts. This step is commonly overlooked in the acquisition process, and, if delayed, rarely implemented properly. This can lead to a reactive plant with missing or improper inspections and PM tasks resulting in increased machine repair costs and associated downtime. Understanding asset lifecycle cost and ownership, standardizing and optimizing machine configuration through documentation practices and knowing how to accurately and timely deploy these Machinery Configuration (H2P) considerations to assets will provide great insight and even greater results from this improved site “vision.”
References
- Matthew Adams. Juggling Systematic Gap Reduction within Lubricant Handling, Machinery Lubrication Magazine, 2020
- Noria Corporation Machinery Lubrication I Training Manual. Tulsa, OK: Noria Corporation
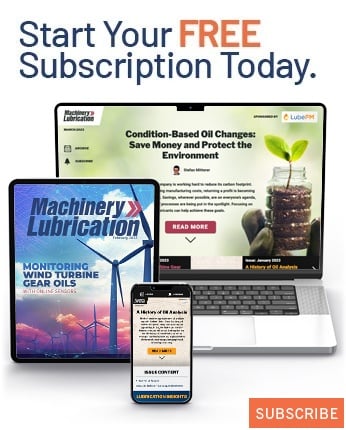