One practice I often see at plants I travel to is the kitting of parts and materials. This might be for a minor repair or a major shutdown where many worn components are replaced. The backbone of the kitting process is to have a list of materials and parts each machine uses.
This data is usually kept in a CMMS system and updated as old machines are mothballed and replaced with new ones. Kitting would be impossible if it weren’t for this “catalog” of parts in the CMMS system.
Along the same lines, something that always baffles me is when I ask what lubricant is being used in a particular machine, and half the time, the answer is, “I’m not sure.” If all the other data for a machine is listed in the CMMS, then why isn’t the Lubricant? Is the lubricant not one of the most important pieces to keep the machine running?
Over the years, I have heard many reasons why, including:
- “They’re on the poster in the lube room.”
- “The lubricant in the CMMS system is old – we don’t even carry that lubricant anymore, so we don’t look there for it.”
- “Our technicians know in their head what lubricant is to be used.”
This is where a Lubrication Management System (LMS) can help.
A critical component of an LMS system would be a list of all lubricants used on-site. I emphasize “all” because I have seen many times a list of lubricants being used that are of a particular brand; if another brand is being used on a “one-off” machine, it will not be included in this list.
Other key components that should be housed in the LMS pertaining to lubricants would be:
- An image of the lubricant tag or label
- Brand name of the lubricant
- Lubricant Identification System (LIS) code for that particular lubricant
- The applications in which the lubricant is being used
- The Safety Data Sheet & Technical Data Sheet (SDS & TDS)
Lubricant Tag
The lubricant tag is a quick way of knowing what lubricant is used in a:
- Bulk storage tank
- Sealable & Refillable (S&R) jug
- Grease gun
- Filter cart
- Maintenance point
When building a lubricant tag, three things should be included: color, shape and text that might be the specific brand and name of the lubricant or the LIS code of the lubricant. Adding some sort of text is important in case there is a technician on site that may be color blind. Having a quick, easy way of making tags is also essential.
Brand Name of the Lubricant
I know this seems like a no-brainer, but you may be surprised how many lubricant lists I find that lack the actual name of the lubricant. I often see things like 68 Hydraulic Oil or Mobil ISO VG 220. While this detail helps break it down a little, neither points to the exact lubricant to use.
We all know thousands of ISO VG 46 hydraulic oils are out there, and Mobil makes several types of ISO VG 220 Oil. With this little information, we still have that lingering question of what oil is truly being used in a machine.
If using the brand name of a lubricant for labeling purposes, you need to remember that if lubricant brands are changed at the plant, your labeling system is now out of date. Sometimes it is best to use a generic code like the one listed below.
A sample of a LIS label
Lubricant Identification System Code
ISO 6743 is the standard for lubricant classification. In short, this standard breaks down the lubricant by make-up (base oil and additives) and by application to assign an ISO Symbol. This system uses great detail without getting too far in the weeds.
One code you might have seen before is HM for use in general Hydraulic Oils. On Noria lube tags, you will also find the ISO VG of the lubricant, the base oil, and for grease, the thickener used, as well as the NLGI grade.
You may ask yourself why this information belongs on a lubricant list, which is a great question. Imagine If you create a lube tag with the brand name of the lubricant being used, then once all your machines are tagged, you have to switch brands for whatever reason, and now you have to re-tag all those machines. However, if you have the LIS on the lube tag, you can find a compatible lubricant in another brand and keep the same lube tag on the machine.
Applications
There are two things I like to see on a lube list when it comes to applications – the types of machines the lubricant is being used in and the volume of lubricant used on the site. Knowing the equipment the lubricant is used in can help arrange colors on the lube tags.
For instance, all gear oils might be orange. Mixing lubricants is never a good idea, but mixing two lubricants in the same class with different viscosities is less dangerous than mixing lubricants in different classes, such as a hydraulic oil and a gear oil. Knowing the amount of lubricant being used on site can help a lube program know how much needs to be stored in the lube room, and it is vital when planning for future maintenance events such as shut-downs or large oil changes.
Safety Data Sheets & Technical Data Sheets
Most industrial plants have a policy stating that there should be an SDS for all lubricants held on-site. During an assessment, if I ask if there are SDSs for all the lubricants on site, I get “yes.” However, when I ask to see them, the squirming begins.
Having all the SDS in the LMS means they are in a central place, and anyone in the lube program can quickly access them. The technical data sheets can assist if there are any questions about where a particular lubricant can and can’t be used. Also, they can tell you the different limits of a grease, such as high and low working temperatures.
Documentation is Key
What it comes down to is detailed documentation. I like to say, “When it comes to a lubrication program, success is found in the details.” Document every little detail, starting with creating a consolidated lubricant list. A legible, color-coded, labeled lube list is the key to ensuring that your lubrication program is starting off on the right foot.
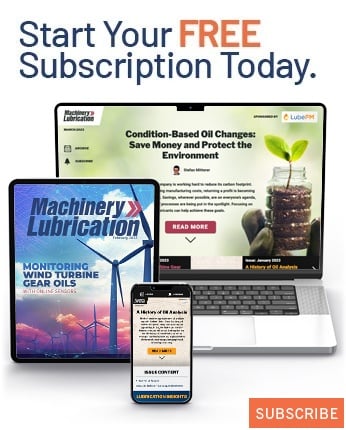