What We're Looking For
1. Organization: Eliminate clutter and store oil drums horizontally or use a bulk storage system. Clearly label all lubricants to avoid mix-ups.
2. Cleanliness: Keep your lube room free of spills, dirt, and dust. Ensure clean transfer containers, pumps, and hoses.
3. Best Practices: Show what best practices you've incorporated to bulid a world-class lube room, including:
- Horizontal storage of oil drums indoors or utilization of a bulk storage system.
- Implementation of a clear lubricant labeling system.
- Use of clean transfer containers, pumps, and hoses.
- Storage of grease guns horizontally, preferably within a clean, fireproof cabinet.
- Sanitary conditions free from oil spills, dirt, and excessive dust.
5. Your Journey: Tell us how you've incorporated best practices and what results you've seen from doing so!
How to Enter
- Snap a few photos of your lube room
- Prepare a short summary of your lube room (3-5 sentences)
- Sumbit your entry by March 21, 2025.
Prizes
Winners receive:
-
Gift from OilSafe
-
VIP passes to the 2025 Reliable Plant Conference & Exhibition in Chicago, June 2-5
-
Cover Story in Machinery Lubrication Magazine
-
Lube Room Challenge Engraved Trophy
Enter the Lube Room Challenge
Need Further Inspiration?
To inspire and guide you in your lube room makeover journey, let's delve into examples of successful transformations from previous participants and winners:
Anheuser-Busch InBev: Recognizing the need for efficiency and organization, this brewery revamped its lube room by relocating it to a larger space and implementing standardized procedures. By consolidating lubricant varieties and instituting color-coded systems, they achieved significant reductions in lubricant usage and waste. (2018)
Calumet: By embracing change and investing in training, this refinery transformed its lube room into a well-oiled machine. From color-coded dispensers to vigilant maintenance, they bid adieu to errors and welcomed a new era of reliability. (2013)
Aleris: This foil and light-gauge aluminum sheet mill in Clayton, N.J., used the Lube Room Challenge to streamline lubricant storage, introduce color-coding, and enhance filtration methods, along with initiating a corporate reliability program which focused on lubrication to evaluate all company plants and led to the development of a technical advisory group (TAG), as well as a training manual with the assistance of Noria technical consultants. (2017)
Mosaic: In 2015, the Mosaic Four Corners phosphate mine in Florida initiated a journey towards world-class lubricant storage, prompted by a companywide push for improved practices. They transformed a storage shed into a centralized, safety-conscious area, implementing measures such as floor sealing, color-coded identification, and strict safety protocols. (2017)
Burckhardt Compression: This leading manufacturer and service provider of reciprocating compressor systems in Pune, India, identified pinpointed various areas for improvement, including focusing on standardizing lubricants, reducing inventory, and upgrading storage practices. The new lube room, with enhanced safety features and contamination prevention measures, has significantly improved equipment performance and led to a reduction in inventory by 30%. (2016)
Visy Paper: Down under in Australia, Visy Paper rolled out a blueprint for lube room perfection. With climate-controlled storage and meticulous organization, they raised the bar for cleanliness and efficiency. (2013)
AGCO Brazil: This Canoas maintenance department in Brazil revamped its lube room in response to high lubrication-related downtime. Unmarked drums and cross-contamination prompted a transformation, and a new lube room was built with filtered storage tanks and color-coded systems, significantly reducing contamination and saving $30,000 in 2013. Following an analysis of the maintenance group and an audit of the lubricants in use, an action plan was developed to implement best practices and training of the lubrication staff — leading AGCO Brazil to become a model of world-class lubrication. (2014)
Cameco: This Saskatchewan mine transformed its lubrication practices by establishing dedicated underground and surface lube rooms with a color-coding system for oil categorization. Kidney-loop filtration and sealed containers were adopted, reducing hydraulic and compressor oil varieties. Technicians are now MLT certified, ensuring sustained improvements in lubrication efficiency and equipment longevity. (2016)
Shoco Oil: Embracing industry best practices, this bulk lube facility in Colorado implemented stringent storage and handling protocols to ensure product integrity and cleanliness. Modern filtration systems and sealed containers enhanced lubricant quality and reliability. (2015)
Camso Loadstar: From Sri Lanka's shores, Camso Loadstar emerged victorious with a lube room makeover fit for royalty. With sealable containers and meticulous spill containment, they bid adieu to contamination and embraced a future of reliability. (2018)
Yanbu Cement Co.: In the heart of Saudi Arabia, Yanbu Cement Co. embarked on a journey of transformation. With closed cabinets and color-coded systems, they bid farewell to chaos and embraced a future of order and efficiency. (2018)
Ingredion: Ingredion’s Canada's Cardinal plant made an impressive transformation in lubrication management, winning Noria’s 2019 Lube Room Challenge. Their vast improvements also included a new lubrication building, new, color-coded storage units and transfer containers, as well as a lab area solely for lubrication technicians to conduct viscosity tests and manage their daily work. (2019)
What Are You Waiting For?
Ready to showcase your lube room? Submit your entry by March 21, 2025 for a chance to win Noria’s Lube Room Challenge and attend the Reliable Plant & Machinery Lubrication Conference in Chicago, June 2-5. Don’t miss this opportunity—upgrade your lube room and put your best practices in the spotlight!
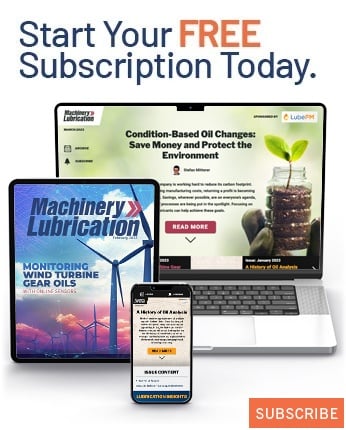