As college football fans around the country gear up for the excitement of Bowl Season, I’d like to take a moment to think about a different kind of bowl that could be the next game-winner to your machines. Of course, I’m talking about the competitive showdown of the Bottom Sediment and Water (BS&W) Bowls.
What is a BS&W Bowl? While it might not get the same attention as the Rose Bowl or the Sugar Bowl, their impact on machinery reliability and condition monitoring can’t be overstated.
What Is a BS&W Bowl?
BS&W Bowls are critical sight glasses often attached to lubrication systems that allow equipment to be inspected and quickly drained of damaging contaminants such as water and sediment. Why?
Unfortunately, solid debris and water are the most frequent reasons why bearings and gears experience failure. Maybe it’s just a coincidence, but both contaminant types often collect at the bottom of the sumps due to gravity. These bowls are a daily visual check and a practical method of managing fluid contamination.
The Importance of Contaminant Monitoring and Contamination Control
Water and solid debris (sediment) in your lubrication are the top opponents to your equipment. Unfortunately, nearly all oil-lubricated gearboxes, compressors, pumps, and hydraulic systems do not come from the Original Equipment Manufacturer (OEM) with effective contamination inspection devices.
Water, in particular, promotes corrosion, depletes additives in lubricants, and compromises film strength. Conversely, sediment will accelerate wear and blitz filters, reducing efficiency and increasing downtime.
BS&W Bowls act as the first line of defense. Before other predictive maintenance technologies detect a problem, the typical root cause, solid debris, and moisture is detectable shortly after ingression. When equipment operators use these inspection devices, they can perform proactive maintenance to monitor the cleanliness of the oil.
Postgame Takeaways from the BS&W Bowl
- Real-Time Monitoring: These bowls provide a clear, visual indication of contamination levels, allowing operators to take immediate corrective actions.
- Simplified Maintenance: By enabling the quick removal of water and sediment (by using the purge valve), BS&W Bowls remove the bulk of these contaminants and reduce the frequency and complexity of more invasive maintenance procedures.
- Improved Equipment Reliability: Reducing contaminants enhances machinery's performance and lifespan, thereby reducing unplanned downtime.
- Cost Savings: This proactive contamination control strategy prevents expensive repairs and replacements, ultimately lowering the total cost of ownership.
The Current Gap in OEM Equipment
Despite the BS&W Bowl winning records, especially with detecting issues quickly and maintaining machinery health, this hardware device has yet to become standard in most machines as they come from the OEM. Instead, they are often added as a post-purchase modification.
Call it a "mid-seasons trade acquisition" if you’d like; this investment represents a proactive step taken by equipment owners to provide both fundamental condition monitoring through inspections and the purge of visible debris.
It’s essential to recognize that these BS&W Bowls are just one of several possible gaps left by the OEM designs and, when installed, are a vital reliability enhancement to maintain equipment efficiency. Other considerations include desiccant breathers, quick-connects, 3D sight glasses, and more.
Wear on the Front Line
The magnet in the middle of the BS&W Bowl is like the safety to detect wear debris. When machine wear occurs, these magnets can capture the ferromagnetic particles (mainly iron) generated by component wear. This bowl serves as an early warning system, signaling issues before they escalate into significant failures. By regularly inspecting this bowl, maintenance teams can identify wear patterns and take preventative action.
High Humidity, Rain, and Snow in the Forecast
When water gets into the arena, it can induce problems in both the functions of the lubricant and the tribological zones between relative moving surfaces. The BS&W Bowl helps isolate and provide removal of water from lubricants. When it recurs, taking action to find the source is necessary to prevent corrosion, additive depletion, and compromised film strength, ensuring optimal system performance.
Debris on the Field
Most debris and other insolubles in the oil will find their way downward onto the field of view within the BS&W Bowl, including sludge and hard deposits on internal machine surfaces. These bowls become an early inspection opportunity before they begin to clog systems and reduce efficiency.
Uniform Color (and Clarity)
As oil experiences early stages of chemical effects, such as oxidation, thermal degradation, and hydrolysis, the oil will lose its clean and clear appearance. This change might be visible from other vantage points, such as at the oil level gauge, but when light can pass through the BS&W Bowl, the color and clarity will be much more evident.
The Rundown on Returns
The ultimate goal of any reliability initiative is to understand what leads to production losses and improve equipment efficiencies. Holistically, calculations such as RONA (Return on Net Assets) help indicate the return physical assets had, including maintenance costs, total availability, and efficiencies to produce quality products.
Across the playing field, contamination is one of the top contributors to increased maintenance costs and premature machine failure. When contaminants are detected early and proactively controlled, this leads to more dependable assets and quality production. Reliability Engineers and Reliability Managers with more than 10 years of experience often note that addressing contamination has the most significant impact on RONA.
Likewise, contamination awareness and the importance placed on lubrication is a common challenge reliability experts must overcome. When machines are not able to be inspected, staff on the plant floor can’t easily recognize this connection for themselves. The bottom sediment and water bowl is ideal for providing this visual evidence and helping achieve higher reliability.
Making This Bowl Season Count
As you plan during the off-season (scheduled shutdowns), there’s no better time to evaluate your contamination control strategies and modify your machines with the right hardware. You may even consider thoroughly assessing your current systems to identify areas where other proactive hardware solutions for inspection, contamination control, oil analysis, or lubricant application could make the biggest difference. Here are some steps to get started:
- Inspect Your Fluids: Use oil analysis to identify current contamination levels and trends. Note: This can be a good starting place if you don't currently do oil analysis or are not yet taking good oil samples.
- Evaluate High-Risk Areas: Focus on systems that are particularly susceptible to water ingress or sediment accumulation, such as larger lubricating oil reservoirs and outdoor equipment.
- Select the Right Equipment: Choose BS&W Bowls that are sized appropriately for your systems and can detect specific contaminants or wear concerns.
- Train Your Team: Ensure that operators understand how to monitor and maintain these bowls effectively to maximize their benefits.
- Pro-tip: If leak risks associated with breaks are a point of contention, make sure you select the BS&W Bowls that are durable even in brutal collisions at the line of scrimmage.
A Winning Strategy
Just as coaches develop game plans to win on the field, maintenance teams need strategies to keep their equipment running without surprises. By integrating BS&W Bowls and contamination control into your reliability program, you’ll set your team up for success in the long run.
After all, you don’t want to deal with a surprise machine failure and unscheduled downtime while trying to enjoy the big game at home. It’s time to make Bottom Sediment and Water Bowls the MVP of your maintenance playbook.
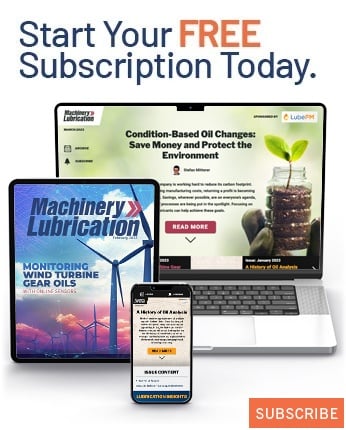