The first part of this series discussed the early history of lubricant base oils through the early 1950s. Here, in Part 2, we review modern base oil technologies and describe how modern base oils have opened the door for great improvements in finished lubricants. Part 3 will compare the performance of base oils and cover future trends.
Hydrotreating
Hydrotreating was developed in the 1950s and first used in base oil manufacturing in the 1960s by Amoco and others. Hydrotreating is a process for adding hydrogen to the base oil at temperatures above 600°F and pressures above 500 psi in the presence of a catalyst. This removes impurities, stabilizes the most reactive components in the base oil, improves color and increases the useful life of the base oil. Hydrotreating by itself is not generally sufficient to make base oil.
Hydrocracking
Hydrocracking is a more severe form of hydrotreating. In hydrocracking, the base oil feed flows over a high-activity catalyst bed at temperatures above 650°F and pressures above 1,000 psi. Feed molecules are reshaped and some are cracked into smaller molecules. Almost all of the sulfur and nitrogen are removed, and many aromatic compounds are saturated with hydrogen. Molecular reshaping occurs as isoparaffins and saturated ring compounds are formed.
These compounds have high viscosity indexes (VIs) and low pour points. However, waxy compounds, chiefly normal-paraffins, are largely unaffected by hydrocracking and must be removed in a subsequent process in order to reduce the pour point. Clean fuels (diesel and jet fuel, as well as naphtha for motor gasoline) are byproducts of this process.
A primitive version of the hydrocracking process was attempted for lube oil manufacturing in the 1930s but was soon abandoned for economic reasons after the solvent refining process was commercialized. Hydrocracking catalyst technology, however, continued to improve.1
After World War II, predecessors to modern hydrocracking catalyst technology were imported from Germany. Chevron commercialized this technology for fuel production in the late 1950s.2 In 1969, the first hydrocracker for base oil manufacturing was commercialized in Idemitsu Kosan Company’s Chiba Refinery using technology licensed by Gulf.3 This was followed by Sun Oil Company’s Yabucoa Refinery in Puerto Rico in 1971, also using Gulf technology.1
Catalytic Dewaxing and Wax Hydroisomerization
Catalytic dewaxing is a high-temperature, high-pressure process in which a catalyst selectively cracks the wax molecules present in a base oil to light products, such as gas and naphtha. Although this process is efficient, it is somewhat wasteful, as high-value wax is converted to lower value gas and light fuel. In hydroisomerization, the process is similar, but the wax is selectively converted (isomerized) into very high quality base oil. Both processes remove wax and therefore lower the pour point of the base oil, but hydroisomerization results in higher VI base oil and better yields.
The first catalytic dewaxing and wax hydroisomerization technologies were commercialized in the 1970s. Shell used wax hydroisomerization technology coupled with solvent dewaxing to manufacture extra high VI base oils in Europe. Exxon and others built similar plants in the 1990s. In the United States, Mobil used catalytic dewaxing in place of solvent dewaxing, but still coupled it with solvent extraction to manufacture conventional neutral oils.
Catalytic dewaxing was a desirable improvement to solvent dewaxing especially for conventional neutral oils, because it utilized simplified operations to remove n-paraffins and waxy side chains from other molecules by cracking them into smaller molecules. This lowered the pour point of the base oil so that it flowed at low temperatures, like solvent dewaxed oils.
Chevron was the first to combine catalytic dewaxing with hydrocracking and hydrofinishing in its Richmond, Calif. base oil plant in 19844 (Figure 1).
Figure 1. ChevronTexaco’s Richmond, Calif.
Lube Oil Plant (RLOP)
This was the first commercial demonstration of an all-hydroprocessing route for lube base oil manufacturing.
In 1993, the first modern wax isomerization-dewaxing process was commercialized by Chevron.5 This was a huge improvement over earlier catalytic dewaxing because the pour point of the base oil was lowered by isomerizing (reshaping) the n-paraffins (wax) and other molecules with waxy side chains into desirable branched compounds with superior lubricating qualities rather than cracking them away. This technology breakthrough utilized Chevron’s ISODEWAXING® Catalyst to greatly improve dewaxing yields and base oil performance.
Hydrofinishing
The final step in modern base oil plants is hydrofinishing, which utilizes sophisticated catalysts and pressures above 1,000 psi to give a final polishing to the base oil. In essence, the few remaining impurities are converted to stable base oil molecules.
Putting it All Together
Modern hydroprocessing makes products with exceptional purity and stability due to an extremely high degree of hydrogen saturation. These products are distinctive because, unlike other base oils, they typically have no color. By combining hydrocracking, isodewaxing and hydrofinishing, molecules with poor lubricating qualities are transformed and reshaped into higher-quality base oil molecules. Pour point, VI and oxidation stability are controlled independently in the separate catalytic processing steps.
Among the many benefits of this combination of processes is greater crude oil flexibility; that is, less reliance on a narrow range of crude oils from which to make high-quality base oils. In addition, the base oil performance can become substantially independent of crude source, unlike solvent-refined base oil. Figure 2 shows a block flow diagram of a modern base oil plant with two parallel process trains - one for light base oils and one for heavy base oils.
Figure 2. Hydroprocessing Group II
Group II - Modern Conventional Base Oils
Lubricant base oils made by modern hydroprocessing technologies show generally better performance compared to older processing routes. This prompted the American Petroleum Institute (API) to categorize base oils by composition (API Publication 1509) in 1993, as shown in Table 1.
The table shows that Group II base oils are differentiated from Group I base oils because they contain significantly lower levels of impurities (less than 10 percent aromatics, less than 300 ppm sulfur). They also look different. Group II oils made using modern hydroprocessing technology are so pure that they are almost colorless.
From a performance standpoint, improved purity means that the base oil and the additives in the finished product can last much longer. More specifically, the oil is more inert and forms fewer oxidation byproducts that increase base oil viscosity and deplete additives. Table 1 shows graphically the difference between an API Group I and Group II base oil. The very large difference in impurities is the main reason for Group II’s higher performance, discussed in more detail in Part 3 of this series.
Figure 3. Group II Stocks Have Lower Impurities
The modern hydroisomerization process licensed by Chevron under the name ISODEWAXING has gained acceptance rapidly since its introduction in 1993. In fact, more than 40 percent of all base oils manufactured in North America are now made using ChevronTexaco technology. The rest of the world is still dominated by Group I base oils, but Group II is making significant inroads there as well.
In the past few years, Mobil (ExxonMobil) has added to this trend by commercializing Group II base oils in Singapore and in Baytown, Texas. Mobil Selective Dewaxing (MSDWTM) is used in Singapore to make all-hydroprocessed base oils, and Exxon RHC (Raffinate Hydroconversion), an added hydroprocessing step, is used at Baytown to upgrade approximately half of Baytown’s base oil slate to a solvent-dewaxed Group II. The plant improvement at Baytown brings the proportion of Group II base oils in North America to almost 50 percent.
Figure 4. Percent of Group II Base Oils in North America
Group III - Unconventional Base Oils
Table 1 shows that the API defines the difference between Group II and III base oils only in terms of the VI. Base oils with a conventional VI (80 to 119) are Group II and base oils with an unconventional VI (120+) are Group III. Group III oils are also sometimes called unconventional base oils (UCBOs) or very high viscosity index (VHVI) base oils.
Solvent-dewaxed Group III base oils have been produced in Europe for more than 10 years, primarily by Shell and BP6, but some of these first-generation Group III oils do not perform as well as modern Group IIIs. Consequently, many of these older plants are now being upgraded to enable them to make Isodewaxed Group III oils.7
From a processing standpoint, modern Group III base oils are manufactured by essentially the same processing route as modern Group II base oils. Higher VI is achieved by increasing hydrocracker severity or by changing to a higher VI feed.
Group III base oils are now widely available in North America because they can be manufactured in large quantities by most of the companies that currently make Group II oils. Many of these companies have started adding Group IIIs to their synthetic product lines.
Modern Group III base oils have properties which allow them to perform at high levels - in many cases matching or exceeding the performance of traditional synthetic oils.
Group IV - Traditional “Synthetic” Base Oils (PAO)
The word “synthetic” in the lubricants industry has historically been synonymous with polymerized base oils such as poly-alpha olefins (PAOs), which are made from small molecules. The first commercially viable process for making PAO was pioneered by Gulf Oil in 1951; this process was improved by Mobil in the 1960s. Mobil first used this new base oil in specialty products such as Mobilgrease 28, which solved a wheel bearing failure problem on aircraft carriers in cold climates.8
PAOs became a major consumer-sought lubricant component when Mobil Oil began marketing its Mobil 1®. In the 15 years following introduction, the PAO market traveled a long and winding road battling a slow, steady growth and criticisms of justification for the higher cost compared to conventional oils.
In the last 10 years, the PAO market significantly increased, first in Europe and then in North America, experiencing periods of double-digit growth. In part, the growth might be attributed to the stricter lubricant specifications in Europe that created a market niche for synthetics and semi-synthetic products.8
As the lucrative PAO market grew, some base oil manufacturers began using higher VI Group III feedstocks (usually byproducts from wax manufacturing) to make mineral oils with VIs that matched the PAOs. These new Group III oils were not manufactured from small molecules like traditional synthetics but they bridged the performance gap for most products at a lower cost.
Therefore, some lubricant manufacturers, primarily in Europe, began replacing PAOs with these newly available Group III base oils in their synthetic engine oils. This created a controversy in the lubricants industry as some synthetic base oil producers and lubricant manufacturers believed that polymerized base oils were the only true synthetics.
The most notable niche in which Group IIIs have difficulty competing with PAOs is in very low temperature applications, such as artic lubricants, which have extremely low pour point requirements.
The trend toward globalized lubricant specifications and worldwide OEM specifications is now creating more demand for Group III base oils. This is particularly true in North America due to the 1999 ruling by the National Advertising Department of the Better Business Bureau that allows Group III base oils to be considered synthetic.
The third and final part of this series will discuss base oil performance and cover future trends.
References
- Sequeira, A., Jr., “Lubricant Base Oil and Wax Processing.” Marcel Dekker, Inc., Chemical Industries Series, August 1994.
- Stormont, D. “New Process Has Big Possibilities.” The Oil and Gas Journal, 57, 44, 1959, p. 48-49.
- Company release by Idemitsu Kosan Co, Imperial Chemical LTD, Shell Development Co, “First Lubricant-Oil Cracker.” Oil and Gas Journal, June 12, 1972.
- Zakarian, J., Robson, R. and Farrell, T. “All-Hydroprocessing Route for High-Viscosity Index Lubes.” Energy Progress, 7, 1, 1987, p. 59-64.
- Wilson, M., Mueller, T. and Kraft, G. “Commercialization of Isodewaxing - A New Technology for Dewaxing to Manufacture High-Quality Lube Base Stocks.” FL-94-112, NPRA, November 1994.
- Min, P. “VHVI Base Oils: Supply and Demand.” 4th Annual Fuels and Lubes Conference, Singapore, January 1998.
- Howell, R. “Hydroprocessing Routes to Improved Base Oil Quality and Refining Economics.” 6th Annual Fuels and Lubes Conference, Singapore, January 2000.
- Bui, K. “Synthetics II.” Lubricants World, November 1999.
- Kramer, D., Lok, B. and Krug, R. “The Evolution of Base Oil Technology.” Turbine Lubrication in the 21st Century, ASTM STP #1407, W. Herguth and T. Warne, Editors. American Society for Testing and Materials, West Conshohocken, PA, 2001.
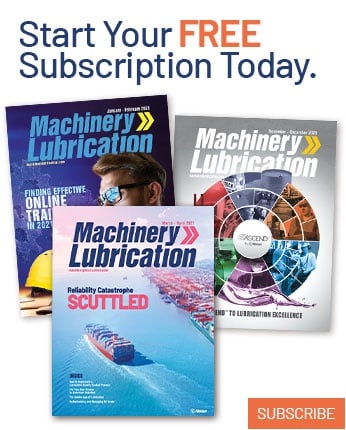