Natural gas engines are unique. They operate in a variety of unusual locations, from the extremely cold climates of arctic Canada to the hot, humid regions of the southern United States and beyond.
Natural gas engines are of various designs, including the Caterpillar vertical in-line and V type four-stroke, the two-cycle Cooper Bessemer V type integral with a horizontally opposed reciprocating compressor and the dual crankshaft, vertically opposed, two-stroke engine built by Fairbanks Morse.
These engines are required to burn a variety of gases including, but not necessarily limited to, sour gas, containing sulfur; sweet gas, containing no sulfur and very little carbon dioxide; wet gas, containing relatively high quantities of component gases such as butane; and finally, landfill or digester gas, composed primarily of methane and carbon dioxide and which frequently contains halogens such as fluorine and chlorine.
In addition, in most jurisdictions where these engines operate, exhaust emissions have become a serious concern. To control or eliminate these emissions, some of the current engine designs require catalytic converters, which limit the additive types and the formulated percentage levels that can be used in the lubricants.
These lubricants vary with engine design and operating conditions and range from simple uninhibited mineral oils, to medium-to-high ash, alkaline and oxidation inhibited detergent oils, to totally ashless, yet highly detergent types.
Uniqueness of Natural Gas Engines
The primary difference between natural gas and other internal combustion engine oils is the necessity to withstand the various levels of oil degradation caused by the gas fuel combustion process, which results in the accumulation of oxides of nitrogen. This condition, commonly called nitration, must be monitored regularly if both lubricant and engine life are to be maintained.
Sulfated ash content is another consideration unique to natural gas engine oils and the significance of sulfated ash will be described in detail during our discussion of the testing techniques.
To properly select the most cost-effective condition-monitoring techniques to achieve maximum efficiency and long life from the engines, engine design, operating conditions and the lubricants must be considered.
Condition-Monitoring Techniques
Several common condition-monitoring techniques are applied to natural gas engines. The analysis of the compression pressure/crank angle or pressure-time (P-T) curve is one common technique.
Natural gas engines have some cycle-to-cycle combustion variations and by measuring the P-T curves, the analyst can determine such conditions as high fuel consumption, uneven internal pressures, high temperatures and unbalance causing detonation, all of which can affect the life of upper cylinder components and the effectiveness of the lubrication and emission control systems.
An analysis of the pressure-volume (P-V) curve can be used to balance cylinders, detect valve train problems and determine frictional losses, by comparing engine horsepower to compressor horsepower.
In addition, analyzing reciprocating vibration patterns can provide the analyst with an understanding of certain mechanical conditions, such as burned valves or gas leaks.
Perhaps the most effective and least expensive natural gas engine condition-monitoring technique available today is the analysis of the engine’s lubricants. Unfortunately, many natural gas engine operators take the lubricant for granted and do not consider the engine oil as another component of the machine, which should be as closely monitored as any other system within the engine.
The oil analysis tests which should be considered part of a regularly scheduled predictive maintenance and condition-monitoring program for natural gas engines include the following:
- Viscosity
- Base number
- Acid number
- Glycol contamination
- Water contamination
- Insolubles
- Spectrochemical analysis
- Nitration/oxidation
Each of these testing recommendations and its significance is described in detail below:
Viscosity
Viscosity should be measured using the standard method ASTM D445 to measure the viscosity at both 40°C and 100°C. The results, reported in centistokes, can then be compared with the viscosity specifications of the new oil. The significance of these results can indicate conditions such as oil thickening (an indicator of oxidation or nitration), increased contamination levels and/or an increase in insolubles.
A reduction in the viscosity can indicate dilution of the oil and in the case of multigrade lubricants may indicate shearing of the viscosity index improvers.
Base Number
Base number (BN) is an indication of the reserve alkalinity contained in an engine oil. It is an indicator of the level of the detergent/dispersant additive package’s ability to counteract acids.
The standard test ASTM D2896 provides an accurate indicator of the BN, the results of which can be compared to the unused oil’s BN. This test is an indicator of additive depletion and the rule-of-thumb is that an oil has reached the end of its useful life when the BN is reduced to one-half that of the new oil specification. Low BNs are usually accompanied by increases in viscosity.
BN is not often used as a test for natural gas engine oils unless the application operates under dual fuel conditions (where the engine uses either diesel or natural gas as fuel under various operating conditions).
If the operation requires that diesel fuel is used for up to 50 percent of running time, BN testing should be included as an oil analysis requirement.
Because most natural gas engine oils are formulated as low to medium ash oils, the BNs will generally be in a range of three to seven. These levels may not be sufficient to protect engines using dual fuels.
BN is also an important oil analysis test when the fuel in use contains high levels of sulfur and/or organic halogens, such as chlorine or fluorine. When high sulfur sour gas or landfill gas is in use, the typical natural gas oils available may not sufficiently protect the engine from acid compounds.
In these cases, the engine operator may need to shorten oil drains, or select an oil with a higher BN, which will provide a higher level of alkalinity.
Potential lubrication problems caused by the use of the kinds of fuel described should be discussed with both the engine manufacturer and the lubricant supplier.
Acid Number
Acid number (AN) is an indication of increased acid levels in natural gas engine oils, frequently accompanied by viscosity increases. AN tests are often used to establish optimum oil drain intervals for many types of industrial oils, particularly those used in natural gas engines. High AN is an indicator of nitration, oxidation and contamination.
The standard ASTM D664 is the primary test used and the rule-of-thumb for this test application is that when the AN doubles that of the new oil value, the oil is nearing its condemning limit.
Glycol Contamination
Testing for glycol leaks in accordance with ASTM D2982 must be part of any oil analysis program. Any amount of glycol in the analysis can indicate a coolant leak into the engine and will cause catastrophic failure by promoting corrosive acids, sludge and varnish to form quite rapidly, as well as to cause a reduction in oil film, which can suddenly increase wear. (It is important to remember that some oils may test “glycol positive,” so caution must be applied when interpreting these results).
Water Contamination
Water contamination, which can be a problem in natural gas engine oils, particularly in those engines which exhibit high flow rates and turbulence, should be determined using ASTM D1744 or D93.
Systems can experience foaming problems with as little as 100 ppm to 300 ppm of water. This is of particular importance in engines where the oil temperatures are too low. Evaporation may not occur and low oil operating temperatures create the conditions necessary for nitration to develop. This is the reason “most” natural gas engine manufacturers recommend that engines run with oil temperatures in a range of 180°F to 185°F (82°C to 85°C).
When the engine’s oil operating temperature is unknown, 120°F (49°C) should be added to the ambient temperature to obtain the estimated oil sump temperature. The resulting oil temperature should then be confirmed with the engine manufacturer to determine if it is acceptable.
Insolubles
Insolubles are the solid contaminants which remain in the lubricating oil, such as dust, dirt and carbon particles, in addition to wear metals that have not been removed through filtration. When insolubles are present, particularly in large quantities, they can promote foaming and will generally increase the oil’s viscosity.
In addition, some natural gas engines that operate in an unbalanced condition will generate soot due to incomplete combustion.
It is important that these insoluble contaminants be monitored and controlled and that they be measured using techniques such as precipitation, centrifugation, gravimetric or particle counting methods.
One such technique, which is performed in accordance with ASTM D4055, measures insolubles by filtering a measured quantity of oil diluted with pentane through a 0.8 micron filter and then weighing the remaining deposit after the filter is dry. The deposit can also be viewed under a microscope and an experienced analyst or engine operator can evaluate the particulate for further action.
One result of such testing is the determination that the lubrication system itself (reservoirs, filter housings, piping and settling tanks) may require cleaning and flushing.
Spectrochemical Analysis
Spectrochemical analysis measures the levels of wear metals and the concentration of additive elements. The results, usually reported in parts per million (ppm), provide an indication of the rates of wear of engine components and the depletion of additives.
Three things must be kept in mind when interpreting spectrochemical analysis. First, the wear particles analyzed are generally limited to those in the 5 micron to 6 micron range. (those particles which are the result of wear, but not the cause of it).
Secondly, wear rate trends are best established after the interpretation of at least three oil samples taken at the same sample interval; in other words, at three similar oil change intervals, or if the oil has not been changed, at the same operating interval, such as 500 hours.
Finally, it is a mistake to assume that every engine of identical make and model will exhibit the same wear rate level or pattern. Each engine will exhibit its own wear rate “finger print” and accurate record keeping is essential if the data collected is to be useful in evaluating engine condition.
Sulfated Ash
Any discussion of the elemental analysis of natural gas engine oils is not complete without a comment concerning the issue of sulfated ash content. Natural gas engine operation tends to form various deposits such as varnish, sludge and an ash residue which remains after the oil is burned during operation.
The varnish and sludge are controlled by the detergent/dispersant additives, however these detergent/dispersant additives tend to leave a grey, fluffy ash residue after the oil has been burned. This ash residue is made up of metal sulfates from such additives as barium, calcium, phosphorus, zinc, magnesium and boron (Table 1).
Therefore, lubricant formulators must ensure that these additive concentrations are high enough to help prevent valve recession, but not so high as to cause unwanted and harmful deposits, or cause catalysts to become ineffective.
Valve recession is the premature wearing of the valve seat into the cylinder head. The sulfated ash residue helps to prevent premature valve recession by “cushioning” the valve seat area (Figure 1).
Figure 1. Typical Valve Recession
in a Natural Gas Engine
Excessively high concentrations of certain additives, such as zinc or phosphorus, can also be harmful to catalyst equipped natural gas engines, because these additives may deactivate the exhaust catalyst by forming glassy-amorphous deposits which prevent the exhaust gas from reaching the active surfaces of the catalyst, which in turn makes control of harmful emissions impossible.
In addition, natural gas engine manufacturers also list the levels of sulfated ash and the additive concentrations that are acceptable for use in their particular engines. For specific recommendations concerning ash content and additive levels, the engine operator should contact both the engine manufacturer and the lubricant supplier.
Nitration and Oxidation
Nitration and oxidation are naturally occurring processes within natural gas engine oils that can be quite severe, depending upon conditions such as air-to-fuel ratios and oil operating temperatures.
Oxidation is caused by the reaction of oil with oxygen in combination with such catalysts as copper wear particles, particularly as oil temperatures increase above 200°F (95°C). Oxidation occurs to some degree in all lubricated systems and results in an increase in the oil’s viscosity.
Nitration on the other hand, occurs most frequently in natural gas engines and if left uncontrolled, can cause serious problems, including the complete solidification of the oil.
Nitration is a chemical reaction within the oil, which causes the carbon chains to react with nitrogen dioxide (NO2) formed during natural gas combustion, causing serious and premature thickening of the oil. This results in the formation of severe varnish and carbon deposits. Once begun, the condition worsens exponentially.
There are two major factors that must be carefully controlled if excessive nitration is to be prevented. The first is the oil’s operating temperature. Nitration becomes significant at oil reservoir temperatures of about 135°F (57°C) and becomes even more dramatic at lower temperatures. (Natural gas engines must be operated with oil temperatures in a range of 180°F to 185°F (82°C to 85°C) in order to control both nitration and oxidation.)
Figure 2. Operators Select the Air-to-Fuel Ratio
for the Application or Conditions Required.
The second major consideration in the prevention of nitration is the air-to-fuel ratio, which has the greatest effect on nitration rates. Nitration peaks at air-to-fuel ratios of 18-to-1 or 19-to-1, depending upon engine type and fuel condition. As Figure 2 illustrates, a rich ratio of 15.5-to-1 is used for best horsepower in a Waukesha gas engine, while a more lean mixture of 17-to-1 is used for greatest economy.
At a ratio of 17-to-1, nitration will occur. In the newer, lean-burn designed engines with ratios of 20-to-1 or leaner, nitrogen oxides are not released, which effectively and dramatically reduces or eliminates nitration.
It is for this reason that the use of either direct infrared spectroscopy, or Fourier Transform infrared (FTIR) oil analysis techniques are highly recommended for natural gas engine oils. The techniques compare samples of the used oil with a reference sample of new oil. The testing instruments chart a curve which represents the difference between the used and new reference samples.
The chart’s curve will immediately point out any contamination, nitration or oxidation conditions. A high concentration of nitration can be used as a indication that a tune up is necessary, because nitration is primarily caused by air-to-fuel ratio, or engine temperature problems (Figure 3).
Figure 3. Infrared Analysis Can Immediately
Determine Nitration and Oxidation Levels.
Oil Consumption Rates
It is important to note that unlike diesel or gasoline engines, natural gas engines can burn large quantities of lubricating oil during operation. The typical oil consumption rate for the Waukesha natural gas engine is 0.0002 - 0.002 pounds/horsepower-hour (0.091-0.910 grams/horsepower-hour).
These oil consumption rates can be determined for any natural gas engine using the following formulas, with the results then compared to the engine manufacturer’s typical consumption rates.
It is important to consider a natural gas engine’s oil consumption rate. The oil analysis interpretation results may be misunderstood if consumption is not taken into account because the addition of make-up oil dilutes wear particle concentrations and contaminant levels.
Engine Manufacturers’ Lubricant Recommendations
The engine manufacturer’s lubricant recommendations should be considered seriously when selecting lubricants and applying effective oil analysis programs. A major reference is the Engine Manufacturer’s Association (EMA) Lubricating Oils Data Book published by the EMA, Chicago, Ill.
This publication provides the data on all types of industrial and heavy-duty engines and the corresponding lubricants recommended for them. For example, the Caterpillar 3520 lean burn natural gas engine (Figure 4) requires a low ash oil with SAE 30 or 40 viscosity.
Figure 4. The Caterpillar 3520 Lean Burn Natural Gas Engine
Caterpillar recommends oil drains at 750 hours, or at an appropriate interval based on a regularly scheduled oil analysis program. Caterpillar engine oil specifications call for oils with sulfated ash levels not to exceed 0.45 percent (wt.) with a BN of 4.8.
Manufactured in Beloit, Wis., Fairbanks Morse vertically opposed piston, lean burn, two-cycle engines (Figure 5) typically consume one gallon of oil, per cylinder, per day when operating at their rated full load.
Figure 5. The Fairbanks Morse Vertically Opposed
Piston, Lean Burn, Two-cycle Engine
As a result, oil drains are never required. According to the EMA publication, oil viscosities recommended are SAE 30 or 40 depending upon temperature. These engines call for oils with sulfated ash as low as 0.2 percent to 0.5 percent with a BN in a range of 3 to 7 when burning high quality natural gas. When burning fuels with up to 1.0 percent sulfur content, the manufacturer recommends oils with sulfated ash content of 1.3 percent to 2.0 percent with a BN of 9 to16.
To conclude; it is absolutely critical that natural gas engine operators fully understand the lubrication and maintenance requirements necessary for their particular operating conditions and the types of gas fuel used. It is also important that operators learn to properly interpret oil analysis results and apply the condemning limits which their experience might require.
The oil analysis condemning limit chart (Table 2) may be helpful when establishing an oil analysis program for natural gas engines.
References
- Leugner, L. The Practical Handbook of Machinery Lubrication (2nd ed.). Canada: Maintenance Technology International Inc. p. 29-33, 185 - 205.
- Marshall, E.R. (1993). Used Oil Analysis, A Vital Part of Maintenance (Vol. 79, No. 2), U.S.A. Texaco Inc. p. 9 -10.
- Nadkarni, R.A. Exxon Chemical Co., Ledesma, R.R. and Via, G.H. Exxon Research. Sulfated Ash Test Method: Limitations of Reliability and Reproducibility, (SAE #952548, Engine Lubricants, SP 1121), Society of Automotive Engineers Inc., U.S.A.
- Waukesha Engine Division. (2001, June 15). Service Bulletin 12-1880Y. Dresser Inc., Waukesha, Wis.
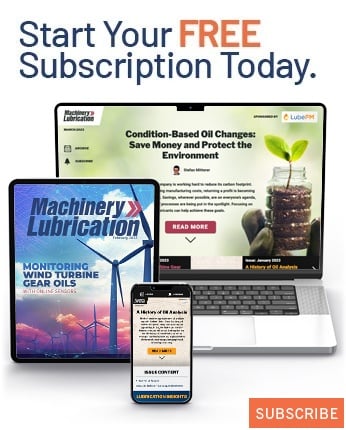