Unless bearings come prelubricated and sealed from the factory, they will periodically need a change of lubricant. How often depends on operating conditions and lubricant type. Bearing lubricants are generally divided into synthetic and mineral-based oils and greases. A synthetic grease will be comprised of a synthetic oil lubricant thickened with either a metallic soap or a nonsoap thickening system.
Mineral lubricating oils deteriorate when they oxidize or react chemically with dissolved atmospheric oxygen. This raises oil acidity and encourages varnishlike surface deposits, both of which can shorten bearing life. Lubricant makers add oxidation inhibitors to help break down hydroperoxides that form during the initial oxidation step.
Additives extend oil life by interrupting oxidation chain reactions and by deactivating any catalytic metal surfaces touching the oil. Oxidation-inhibiting additives are slowly consumed during the initial oxidation period. Adding more inhibitor within this time frame lengthens the induction period and delays acceleration of oxidation reactions.
Synthetic lubricants (Figure 1) generally last longer at elevated temperatures than their mineral-oil counterparts.
Figure 1. Life Expectancy of Inhibited
Synthetic Lubricating Oils in Air
Some types have special low-temperature and low-flammability properties. However, hydrolysis or the tendency to absorb water - even from exposure to atmospheric humidity - tends to shorten the life of some phosphate, silicate and ester synthetic oils. Avoiding hydrolysis may require special additives, desiccating air filters and filtration with activated alumina or clay-based fuller’s earth.
Rate of Change
Elevated temperature is probably the biggest contributor to oil oxidation. The Arrhenius principle (equation) applied to lubricant life suggests that the lifecycle of the lubricant is cut in half for every 10°C increase in temperature. This rule is useful but not exact, because the rate of change increases as the temperature increases.
Assuming no contamination effect, a lubricant’s life L (hours) can be calculated if oil operating temperature T (°C) and product type are known:
Log L = kl + 4,750/(T+273)
where kl (Table 1) depends on oil type.
For example, this equation predicts oil in a turbine bearing at 138°C degrades about 180 times faster than the same oil in a turbine oil reservoir at 71°C.
It is not uncommon for lubrication systems to have several temperature zones. Each of the n zones with oil volume Cn has a deterioration rate of 1/Ln. Summing the individual contributions:
C/L=C1/L1+C2/L2+C3/L3+
+Cn/Ln
gives the overall deterioration rate for all oil in a system. This could be useful in projecting the end point of a charge of lubricant in a paper machine application where multiple hot spots could be found.
Unfortunately, the above approach assumes no water or other contamination, no adverse catalytic effects from copper and iron surfaces, and no oxidation-inhibitor evaporation, all of which can cut expected oil life. Adjusting the above oil-life calculations with an equipment-dependent factor accounts for these items. Electric motors and hydraulic systems, for example, use a factor of three. In other words, oil life in these systems is about 66 percent shorter than the oil-life equations predict. A factor of two to five works for steam turbines and compressors while a factor of 10 is good for heavy-duty gas turbines.
When to Change the Oil
In all cases, improved bearing life calls for periodic (typically monthly) laboratory checks of oil samples for oxidation, viscosity change and contaminant accumulation. Oil changes should be considered when its acidity rises by 0.2 to 0.3 mg KOH/gm above that for new oil, or when viscosity changes more than five percent. This is application-dependent.
Confirming the Need for a Change
Fortunately, several methods are available to rapidly evaluate oil condition. These include:
- Electrochemical. Of numerous electrochemical procedures, cyclic voltametric techniques provide the quickest (less than 10 seconds) and easiest evaluation of remaining antioxidant concentration in lubricants through current-voltage relations at two solid electrodes. Ester aircraft engine oils are first dissolved, or hydrocarbon lubricants suspended, in a solvent containing an electrolyte. As the voltage of one electrode is cycled linearly with time, the voltage at which current flow increases and the magnitude of increase identifies and quantifies, respectively, the antioxidant(s) present in the sample.
- Microscale oxidation tests. The rapid Penn State microoxidation test exposes a one-drop sample to a temperature of approximately 250ºC to simulate oil oxidation life in automotive and diesel service.
- High-pressure differential scanning calorimetry. Once the antioxidants in the lubricant are depleted in the 150ºC to 250ºC temperature range, exothermic oxidation increases the sample temperature. Oxygen or air pressure is used to reduce sample evaporation. For 170 and 550 psi oxygen pressure, three to five minutes commonly indicates oil is at or near the end of its useful life.
One test, called Fourier transform infrared spectroscopy, can measure and quantify in less than one minute the extent of oil oxidation by the magnitude, reported in absorbance/mm, of absorption bands in the 1050 to 1250 and 1700 to 1750 cm-1 frequency ranges. The amount of remaining oxidation inhibitors is also estimated from absorption peaks associated with discrete infrared wavelengths for individual additives. An oil change or replenishing of oxidation inhibitor is signaled when oxidation-inhibitor concentration drops by half or more from original values.
Alternatively, turbine and other circulating-system oils may use the ASTM D2272 rotating pressure vessel oxidation test (RPVOT). Here, a value below 50 minutes indicates marginal remaining life.
Grease Metrics
As with oil, acidity and antioxidant content are important indicators of the life remaining in grease. But greases contain oil and thickeners, both of which also influence lifespan. Oil content is a measure of remaining life and can be quantified in a grease sample by atomic absorption spectroscopy or by solvent separation and weighing of the remaining oil.
Greases typically fail after losing about half their initial oil content. At this point, bearing friction and noise generally rise along with grease iron content. Further operation can cause severe wear and early bearing failure. Figure 2 indicates that failure is to be expected in 10 percent of greased bearings from this degree of dryness after about 30,000 to 40,000 hours of operation with premium ball bearing greases at moderate speeds, temperatures up to 70ºC, and light loads.
Figure 2. Grease Life at Temperatures up to 70ºC
Diminishes with Bearing Speed Factor kf DN
One-half of the initial oil content corresponds to the percentage of soap (thickener), Sf, contained in a grease at failure:
Sf = 100 x 2S0/(100 + S0)
where S0 = the percent thickener in fresh grease. A fresh grease containing 10 percent soap, for instance, would be expected to fail when it had dried to the extent that Sf = 18 percent.
As a rule, larger bearings and those that run at high speeds shorten grease life. Grease time-to-failure typically halves when bearing rotational speeds reach grease DN (pitch line speed) limits, as measured by:
DN = N x (ID + OD)/2
where ID = bore diameter (mm), OD = outer diameter (mm), N = speed (rpm).
Operation at even higher speeds can trigger early bearing failure, partly because centrifugal force throws grease from cage and raceway surfaces.
Speed reduction factor kf is yet another indicator of grease life. It is directly proportional to how far grease must travel to feed the width of ball or roller tracks. Higher values (for a given bearing type) apply to those with larger cross sections or higher load capacity and vice versa. Larger speed reduction factors shorten grease life. For reference, conventional single-row, deep-groove ball bearings have a kf =1.0 and a DN limit of about 300,000.
Speed effects vary among greases as well. For example, so-called channeling-type greases often used in double-shielded and double-sealed ball bearings probably won’t last as long as some other grease types when operating near limiting kfDN values.
Silicone greases with their low surface tension oils and poorer lubricating properties for steel-on-steel surfaces dictate 35 percent lower DN speed limits. An additional 25 to 50 percent DN reduction is called for when operating bearings on vertical shafts.
Elevated operating temperature is also an enemy of greases. In fact, bearings that operate at temperatures above 70°C cut grease life by a factor of 1.5 for each 10°C rise. Above 150°C, rapid oxidation boosts that factor to 2.0 for each 10°C rise. High temperatures promote oxidation and increase oil evaporation rates and oil loss by creep, all of which accelerate grease drying and shorten life.
Grease life LG, can be estimated for operating temperatures above 70°C with moderate loads and no contamination by:
log LG=-2.60+2,450/(T+273)-1x 10-6kfDN
Here, LG is time-to-grease-failure for 10 percent of applications using fresh industrial greases of Grade 2 consistency with thickeners such as lithium, complex metal soaps and polyureas.
The Arrhenius Equation
Common sense and chemical intuition suggest that the higher the temperature, the faster a given chemical reaction will proceed. Quantitatively, this relationship between the rate at which the reaction proceeds and its temperature is determined by the Arrhenius equation, which relates the log of reaction rate to the reciprocal of absolute temperature. At higher temperatures, the probability increases that two molecules will collide with sufficient kinetic energy to activate a chemical reaction. The activation energy is the amount of energy required to ensure that a reaction happens.
In exponential form, the effect of temperature on reaction rates using the Arrhenius equation becomes:
k=A*exp(-Ea/R*T)
where k is the rate coefficient, A is a constant characteristic of the reaction, Ea is the activation energy, R is the universal gas constant, and T is the temperature (in degrees Kelvin).
R has the value of
8.314 x 10-3 kJ mol-1K-1.
There are several ways that lubricant lifecycles can be estimated. Calculating lifecyles based on operating conditions requires application of factors to account for real life conditions, such as solid contamination, moisture, air, catalytic effect of wear debris, temperature variations in a circulating system, etc. As the temperature increases, the rate of change increases. The Arrhenius rule suggests doubling lubricating oil degradation rate for each 10ºC increase in temperature. Grease lifecycles are influenced by the noted problems with oil lubricants, bearing design, surface speeds and grease dryness.
Reference
Figure 1. Beerbower. STLE Special Publication SP-15, 1982.
Editor’s Note
This article originally appeared in Machine Design, March 2003. For related reading, see authors’ Applied Tribology-Bearing Design and Lubrication, New York: John Wiley & Sons, 2001.
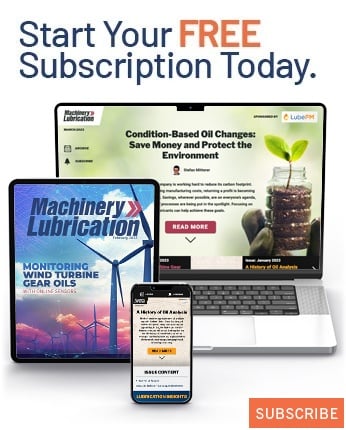