At the Eli Lilly and Company plant site in Indianapolis, Ind., the regreasing of motors and other bearings was a real problem because few people really understood the importance of proper lubrication.
Most bearings were greased based on guesswork. Many were not greased at all. To tackle this problem, a site team was formed consisting of a lubricator, his supervisor, a maintenance coordinator, a vibration technician and myself - a reliability engineer.
Plant Background
My plant is one of the research and administrative facilities of Eli Lilly and Company, a major pharmaceutical manufacturing company. We maintain various utility equipment that supports critical pharmaceutical research activities, such as air handlers, pumps, air compressors and chillers.
The plant has more than 250 mission-critical air handlers, exhaust fans, pumps and chillers that are vital to our operation and are governed by regulatory requirements. They are mission-critical because they affect our research capabilities. In addition, we maintain hundreds of other noncritical pieces of equipment that are essential to plant operations.
I (Wayne Ferguson) have been a reliability engineer at Lilly for three years, and an engineering technician before that. I became interested in lubrication after attending a lubrication class taught by Jim Fitch in New Orleans in 1995. That was when I first realized how important a lubrication program could be to a company’s bottom line.
Figure 1. Wayne Ferguson and
Tom Hiatt of the Lube Team
Job Responsibilities
As a reliability engineer, I’m responsible for the maintenance and reliability of the equipment. My slogan is that in order to perform proper maintenance, we need to have the basics down first. Lubrication of equipment is one of the most, if not the most important routine function within maintenance operations.
We may put a lot of time and money into maintenance, but if we’re not lubricating or performing other tasks correctly, we will never achieve reliability. That was the main reason we wanted to develop a better lubrication program for the company. Most people understand that equipment needs to be lubricated, but we may be doing more harm than good if we are not lubricating properly.
Lubrication Technical Committee
Another one of my job responsibilities is to lead the Corporate Lubrication Technical Committee, or Lube Tech for short. We are a team of individuals from Lilly’s different plant sites with a mission to “provide leadership in support of proactive asset management by establishing and facilitating the implementation of a world-class lubrication program for Eli Lilly.”
Our vision is “increased equipment reliability through the elimination of failures caused by improper lubrication practices.” The average length of service on the team for a member of Lube Tech is eight years. This continuity assists us in gaining deep technical knowledge in lubrication practices.
Figure 2. Dean McClary, a lubricator,
fills an Oil Safe Top-off Container
The group meets monthly to work on lubrication issues that we can roll out company-wide. We have an internal corporate Web site that anyone can use to search for tools and guidelines focused on lubrication. We developed a lubrication audit program at each plant site to assist maintenance areas in measuring and improving their oil programs.
This audit has assisted areas at Lilly in the proper practices for storage, handling, dispensing, safety, oil analysis, waste oil disposal and PMs.
Using the best practices described in the audit, we’ve upgraded our lube room practices. Some of the improvements we have made include: limiting access to lube rooms, installing desiccant vent filters on oil drums and totes, using separate drum pumps for each drum and using separate top-off containers for each type of oil to avoid cross-contamination.
Based on the audit, if a maintenance area can achieve 93 percent or higher for best practices, we present the employees with a plaque certifying their program as world-class.
This award is valid for three years. After the expiration date, a re-audit must be performed to maintain the award. This helps ensure that the lubrication programs are sustained. This award has increased enthusiasm for improving lubrication programs. We have had a significant increase in inquiries about performing lubrication audits at many areas within Lilly.
We also send out “Lube Tech News,” a quarterly newsletter to approximately 400 lubrication/maintenance and operations people (engineers, supervisors, operators and crafts people).
The one-page newsletter features short articles on proper lubrication and other reliability tips. In addition, we have developed site lube teams that report to the Corporate Lube Tech team. These area teams are responsible for implementing the tools developed by the Lube Tech team in their maintenance areas.
Lubrication Initiatives
The Lube Tech team decided that based on its mission and vision statement, its focus would be on equipment reliability. The goal was to develop procedures and guidelines that would become the tools the corporation could use to improve its lubrication programs.
The Lube Tech team has developed more than 45 procedures and guidelines as a result of this goal. These tools range from procedures such as selecting a lubricant category for manufacturing equipment to disposal of used waste oil.
The individual areas of the corporation’s maintenance organizations then implement these procedures and guidelines without having to reinvent the wheel.
Lubricant cleanliness is a major consideration. We developed a lubrication identification loop that starts with the lubricant as a spare part to the equipment, the lubricant is marked on the drum from the vendor, the PM indicates the proper lube type and frequency, the equipment is tagged with the proper lubricant, and the secondary container of lubricant is marked with the lube type.
We have upgraded PMs to reflect the proper frequency based on the speed, type of bearing and operating conditions of the equipment. We state the type and the specific amount of grease to add. We also make sure everyone working with lubricants has had lubrication training. At one time, the role of lubricator was more of an entry-level position with no real training.
We have raised awareness of the importance of the lubrication technicians’ jobs by proving that lubrication has a direct effect on equipment reliability. A benefit of reliable equipment is cost savings and cost avoidance.
Elimination of the routine oil changes has saved more than 50,000 gallons of oil and hundreds of labor hours. Other labor hours have been saved by changes in the frequency of lubrication PMs. In addition, we avoid thousands of dollars in failure costs by using oil analysis. Implementing the Corporate Lube Tech procedures and guidelines has saved us an estimated $1.5 million over the last five years.
Motor Bearing Lubrication Program Revamped
Starting with the most critical machines, we collected the bearing sizes and used the formula G=[(0.114)X(D)X(B)] to determine the relube amount needed in ounces of grease. We then determined the speed of the bearing and the bearing type (ball, roller, etc.) and used an SKF bearing chart to determine the interval for the relube. This enabled us to determine how much grease we needed and how often. We set up PMs with the proper frequency and listed the amount to add for each machine.
Many of the bearings were overgreased, lubricated with four to 10 times too much grease. For this relube program to work, the lubricator needed to know how much grease his grease gun was putting out. We measured the amount in two ways: First, we determined the weight per stroke (.062 ounce per stroke for one of the grease guns).
Secondly, we made up a grease block to determine how many strokes per cubic inch. Many times the motor manufacturer will specify an amount to add, such as two cubic inches of grease every six months. Now we know the number of strokes needed for the lubricator’s grease gun (11 pumps per cubic inch).
We noted in the PM that only the lubricator’s grease gun may be used. All grease guns must be checked in this way and marked with this information.
After setting up the PMs, the vibration analyst closely monitored the bearings for problems. If he noticed that a bearing consistently needed grease, we updated the PM amount. The formula is accurate; we had to update only three PMs and then only by one extra pump. We did this in 1997 on more than 100 pieces of equipment.
As far as we’ve been able to determine, we’ve not had another lubricant-related failure. We also noted that this is for normal operations. Vertically mounted motors or motors subjected to dirty environments or other adverse conditions must be determined separately.
Note: We understand that the proper way to grease a bearing would be to shutdown the machine, remove the bearing, clean and repack. However, this is not possible in our business, so we must lubricate the unit while it is running.
In-house Training
The Lube Tech team and our lubricant vendor, G&G Oil Company of Indiana, developed three lubrication training classes. These three-hour classes are required based on job responsibilities. These training classes are split into three categories: field lubrication specialist, area lubrication specialist and oil analysis technician.
There is also a requirement for continuing education. According to the written practices and the lubrication audit we developed, all lubrication personnel must have initial certification training as a field lubrication specialist within six months of employment or when transferring into maintenance and operations, and then they must attend refresher training every two years.
This training and certification covers the basics of lubrication, sampling requirements and best lubrication practices. To be certified as a field lubrication specialist, the lubrication personnel must pass a 25-question test, based on the course content.
Only trained personnel should lubricate equipment. Training for an area lubrication specialist includes the field lubrication specialist training as well as advanced training that focuses on contamination control, lubricant filtering, lubricant selection and analyzing oil sample reports. The training for an oil analysis technician is the specific training required to operate the testing equipment as well as the previous two classes.
Documenting Machine Life Extensions
I kept track of the actual number of bearings changed out by the machine shop, both before and after the lubrication program improvements. That number of bearing failures has dropped significantly. An average of 10 per month decreased to around two or less per month.
It is interesting to note that many of these bearings were replaced not because they had failed, but were changed due to failure history (many were lasting less than a year). These bearings were changed once per year during an annual shutdown, the goal being to last until the next annual shutdown.
Some of the bearings that were being changed each year have now lasted five to six years. A conservative calculation at my plant site is that we save approximately $100,000 per year from our improved lubrication program.
Oil Analysis Saves Equipment
The plant’s air handlers use chilled water for cooling. We use several large chillers to generate this water. One of the program’s biggest saves was on a steam-driven turbine, a 4,000-ton (48 million BTU per hour) chiller.
We found water in the turbine oil. If we had not been performing oil analysis, the first indication of water would probably have been vibration analysis picking up some type of bearing fault. Luckily it was caught early and we found a seal leak that was allowing steam condensate to enter the oil. This was repaired with no damage to turbine components.
If we had not found this problem early, it could have led to serious turbine damage. A rebuild of the turbine alone would have cost more than $35,000. The loss of capacity from this turbine could have been a real problem, and in addition, there would have been additional costs to us in electricity (approximately $10,000) to run an electric chiller. This one save has paid for our oil analysis program for many years to come.
Figure 3. Lube Tech Team.
Sitting L to R, Doug Elam, Tom Hiatt, Russ Boehm,
and Rick Rice (in-house oil analysis technician).
Standing L to R, Jim Jackson, Wayne Ferguson
(team leader), Terry Turchi (in-house oil analysis
technician), Nathan Haehl, and Scott Arrington
(G & G Oil). Not pictured: Rendela
Wenzel, Alan Neutzman, Mark Shafer
and Dan Nooe (quality control).
Lab Work
The majority of our oil analysis is performed in-house. The in-house lab processes an average of 150 samples per month from all of the Indiana plant sites. We use a variety of instruments, including the CSI 5200 system with particle counter, Oilview model 52DV digital viscometer, Oilview model 51FW ferrous wear monitor and a microscope 51SM.
Because of the number of oil samples generated by Lilly’s Indiana plant sites, it was more cost-effective to have our own equipment and screen the samples for any problems. If a problem is found in the in-house lab and we need more information, we request a second sample be taken and sent to our outside lab - Polaris Laboratories of Indianapolis - for a detailed report.
Due to the number of samples we have (approximately 1,800 per year), screening our samples rather than sending all of them to the outside lab saves us approximately $36,000 per year in outside lab costs.
The in-house oil lab technician performs all tests that the CSI 5200 can give us. These include contaminant index, viscosity, ferromagnetic index, chemistry index and oil life index. Again, if we see a problem in any of the 5200 results, we recommend a new sample be sent to Polaris for a full lab analysis. We’ve developed individual profiles by equipment type that dictates the tests required.
We don’t do any additional lubricant testing outside of regular sampling, which includes particle counting. Even though we don’t do any online or additional particle testing, oil cleanliness is an important consideration in our lubrication program. Lubricant cleanliness guidelines were developed to establish targets for the ISO cleanliness levels of different types of equipment.
Our lubricant vendor, G&G Oil Company, has an established relationship with Polaris Laboratories and receives the oil sample reports at the same time that the reliability engineer for the area receives them.
If the reliability engineer requires assistance analyzing the oil sample report, the Lube Tech team and G&G Oil Company will provide consultation. Polaris is located close to the Lilly plants and we can rush samples to them within a couple of hours if needed.
Inspecting New Oil Deliveries
We recommend that all areas sample new oil upon delivery and confirm that the oil ordered is correct by verifying the information on the drum. The sample is sent to our in-house lab for testing. We request that the oil not be used until the results are back.
This process will generally take about three days. We also follow this procedure for oil that has been in storage for two years or longer. We have set up PMs for lubrication personnel to check the dates on oil drums in storage each year. If any are more than two years old, they send a sample to the in-house lab to confirm that it has not become contaminated. If the oil is acceptable, a new date is written on the drum.
Spec Sheets
G & G Oil Company has worked with Lilly for the last 15 years to develop specification sheets for our equipment and has assisted in consolidating our lubricants. At one time, there were more than 480 different lubricants in use, which have since been reduced to around 95. These lubricants include H1 and H2 food-grade products.
The Lube Tech team maintains the list of specifications and the approved lubricants that can be used at Lilly. When a new piece of equipment is brought into the plant, it is the responsibility of the Lube Tech members to assign a lubricant. If we don’t have a specification for the lube recommended by the manufacturer, a new specification is written based on the requirements of the equipment.
If our vendor does not carry a product that meets our specifications, they will recommend where to obtain a lubricant that does.
Leading the Way
We’ve tailored our program based on the best practices we’ve learned from Noria, through its magazines and training courses.
Management support has been the key to lubrication improvements. Without stakeholders who understand the effects of a poor lubrication program, we would still be operating with failures as a result of lubrication practices.
We have built a lubrication program based on the Noria and CSI training we’ve received, as well as information gleaned from Noria’s magazines, and the electronic Lube-Tips newsletter and lubrication conferences.
If we see a new product or technique, we discuss it at the monthly meetings to determine how to apply it at the plant sites. In addition, the involvement of the lubricant vendor and the enthusiasm of team members have been some of the main reasons for success. Having the right attitude will go a long way when trying to improve one’s oil program.
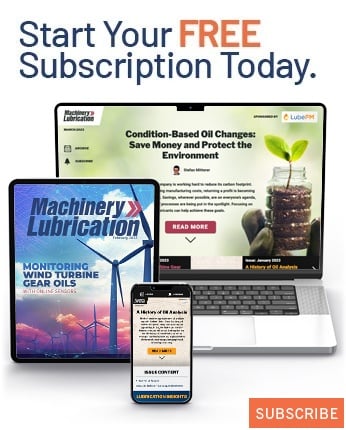