Hydraulic components are unique in that it is often possible to offset or balance hydrostatic forces to reduce loads on lubricated surfaces. By reducing surface loading, the maintenance of fullfilm lubrication is improved and boundary lubrication conditions are less likely to occur.
Hydrostatic force is the product of pressure and area. Expressed mathematically, the equation is F = P x a. The balancing or offsetting of hydrostatic force is achieved by exposing opposing areas to the same pressure. The double-acting cylinder in Figure 1 illustrates this concept.
Figure 1. Hydrostatically balanced cylinder
loading two lubricated surfaces.
The rod-side area of the piston, Area B, is 80 percent of Area A. This means that the force exerted on the lubricated surfaces at the end of the cylinder rod is 20 percent of the force developed by the pressure acting on Area A. This is due to the balancing or offsetting force developed by the same pressure acting on Area B. Assuming the speed of the rotating surface (Area C) and fluid viscosity are adequate, full-film lubrication of the sliding surfaces is achieved.
The same principle applied to a typical axial design piston is illustrated in Figure 2.
Figure 2. Cross-section of an axial design piston.
Area A is exposed to system pressure during outlet (pump) or inlet (motor) and the force developed is transmitted to the lubricated surfaces of the slipper and swash plate. System pressure also acts on Area B, the balancing area of the slipper, via drilling through the center of the piston. Area C is the sliding (lubricated) area of the slipper. While the ratio of these three areas varies, in this particular piston, Area B is 50 percent of Area A and Area C is 140 percent of Area A. This means that the force transmitted to Area C is half of the force developed by Area A and is spread over 1.4 times the area, further reducing the load on the lubricated surfaces.
Figure 3. Loss of hydrostatic balance
increases load on the lubricated surfaces.
If the hydrostatic balancing force is lost, for example, no pressuring acting on Area B (Figure 3), the force exerted on the lubricated surfaces at the end of the cylinder rod will be 100 percent of the force developed by the pressure acting on Area A. If full-film lubrication is dependent on the hydrostatic balance of the cylinder, boundary lubrication conditions will eventuate and two-body abrasion is likely.
Figure 4. Cross-section of axial piston
showing blocked balance drilling.
Applied to an axial piston, this is equivalent to blocking the balance drilling by particle contamination (Figure 4). As a consequence, 100 percent of the force developed by the pressure acting on Area A is transferred to Area C, most likely resulting in boundary lubrication and twobody abrasion between slipper and swash plate.
Because hydrostatic force is a product of pressure and area (F = P x a), hydrostatic balance is affected by changes in either pressure or area. As illustrated in Figures 3 and 4, blockage of balance drillings by contamination results in loss of hydrostatic balance. Wear caused by two-body and three-body abrasion can affect hydrostatic balance by altering the areas where balancing pressure acts or by reducing the effective balancing pressure.
To illustrate this, consider the sliding surface of an axial piston slipper. The inner edge of the slipper’s sliding surface is a load concentration point. Deformation of this area can result in localized contact (two-body abrasion) between slipper and swash plate.
Figure 5. Mushrooming of
slipper surface reduces
effective balancing area.
This causes the slipper’s surface to mushroom (Figure 5), creating an area that acts to increase the hydrostatic force, and therefore load, on the lubricated surfaces of the slipper and swash plate. Once the slipper begins to mushroom, a cycle of increased load and wear follows (Figure 6), leading to loss of hydrostatic balance and slipper failure.
Figure 6. Advanced mushrooming
and wear of piston slipper.
The slipper’s sliding surface acts as a seal for hydrostatic balancing pressure.
Figure 7. Heavy scoring
of piston slipper.
If this surface becomes severely scored as a result of threebody abrasion (Figure 7), leakage can increase to the point where a pressure drop develops between the piston area and the slipper’s balancing area. This reduces the hydrostatic balancing force and increases the load on the lubricated surfaces of the slipper and swash plate. The resulting cycle of increased load and wear leads to loss of hydrostatic balance and slipper failure (Figure 8).
Figure 8. Failure of piston
slipper caused by loss of
hydrostatic balance.
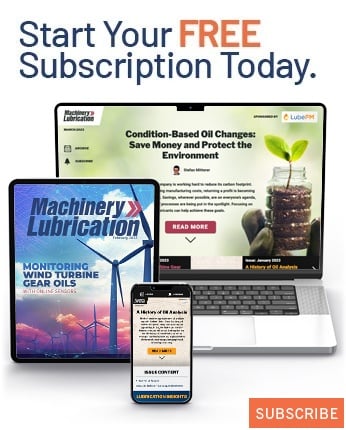