On an ongoing basis within the pages of Machinery Lubrication magazine there are a variety of opinions expressed by a diverse group of authors presenting heartfelt positions, some of which are widely accepted and others which are hotly contested.
As the primary technical editor for these articles, it is an interesting challenge negotiating with authors to present an accurate reflection of their respective positions, while at the same time preserving the “truth of the matter” to the best of my understanding of the technical application of an idea.
Though it may not seem that there could be questions of a philosophical nature for the topics addressed in a trade publication such as this one, the deeper one digs into a matter the more splintered and the greater the number of branches one finds stemming from the core concept. Even the apparently simple topics that we address are sometimes found to create controversy with loyal readers.
Take for instance, the simple matter of grease replacement quantities for element bearings. This could be considered a cut-and-dry discussion based on a few undebatable facts, such as: bearing size and type, shaft orientation (vertical or horizontal plane) and speed, dynamic load, operating temperature, frequency for relubrication, and type of lubricant. Alas, things are never quite so simple.
These facts are required before a complete decision can be made. However, there are a variety of factors one should consider, including: machine criticality (to production), machine and component sensitivity, machine operating stability, preload and peak load, frequency and extent of irregular loading, lubricant raw material selection, lubricant quality and stability, skill level and consistency of the technician involved, and the nature, harshness and consistency of the operating environment. The list could go on …
At some point, one must declare that enough factors have been collected and proceed with the task of making the best guess on replenishment volume. It is possible to record all of the factors that should be considered when setting standards for a given machine, but it is often not practical to do so. Obviously, the cost of data collection increases with the number of factors considered.
I have personally spent as little as two seconds to as much as 16 hours in data collection and analysis prior to arriving at a decision and making a recommendation for an application.
Interestingly enough, regardless of the apparent technical accuracy or “rightness” of the decision, there can be numerous changes in an operation that could render the technically correct recommendation to be completely useless or even disastrous.
At the very minimum, this points to the need for a way to manage maintenance information effectively, especially for maintenance practices either driven by or directly influenced by operating condition.
If even the simple factors, such as volume selection, are subject to debate then what is the point of trying to make a precise decision? The phrase “the devil is in the details” comes to mind. It is better to deal with the devil you know than the devil you don’t.
The quality of the lubrication program is the most important factor to long-term machine reliability, assuming that the machine is properly designed, built and installed. It is therefore worth trying to arrive at a cost-effective and technically defendable decision to support long-term lubrication methods and practices.
Back to the original point - Noria sometimes publishes articles that are somewhat off the beaten path. This is useful because it contributes to the expanding array of considerations one may adopt when making decisions.
Some of these articles are difficult to for me to endorse because they do not line up with my own humble, but accurate, views and experience. If selecting the right volume of grease for a bearing can be controversial, then perhaps it is time to pick at some of these controversies and try to shed some earnest light on the issues.
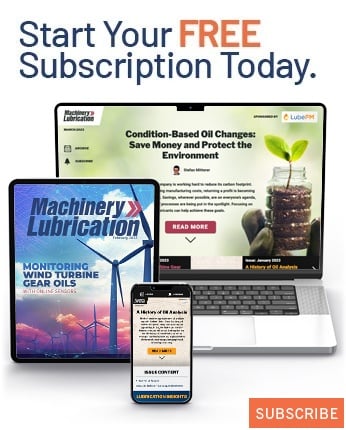