We are all too aware that starting in 2008, hundreds of thousands of baby boomers began to retire, initiating the largest single exodus out of the workforce by a single generation.
A study by the U.S. Bureau of Labor Statistics reports that more than 17 percent of baby boomers holding executive positions are predicted to depart from their careers by 2008.
In the same year, the ratio of workers to retired employees will drop from 3:1 to 2:1. Individual sectors may be hit even harder. According to the Oil and Gas Journal, by the year 2010 as many as 60 percent of experienced managers will retire from the oil and gas industry.
As these baby boomers begin to leave, they will likely take with them a wealth of knowledge not captured by those replacing them. Known as “corporate amnesia,” the companies these baby boomers are retiring from will eventually feel the crunch of heuristics (discovery achieved by trial and error) gone missing.
The Bottom Line
We can all imagine how corporate amnesia may affect the bottom line of an individual company. In the April 2003 Harvard Management Communication Letter, Anne Field describes how in 1994, a large consumer products company was forced to delay the introduction of a major new product because of technical design problems.
During the delay, a rival consumer products company launched a similar offering. When the issue was finally resolved, the company wasn’t able to make up for lost time and failed to procure market share from the already established competitive product, resulting in an estimated loss of a staggering $1 billion. An internal review turned up a painful revelation: the company actually had developed the solution – 15 years before.
The information had simply been buried and forgotten, the victim of turnover and retirements. Unfortunately, this is the painful reality of corporate amnesia at its worst.
The Boom
Consider how this exodus will evolve. In 2008, the first of the baby boomers will retire from every conceivable position in every industry, individually taking with them decades of heuristics, most of which have never been adequately or accurately captured, evaluated or improved upon.
At best, corporations will attempt to capture some of this information by a mere job shadow for a few weeks. Needless to say, those individuals replacing our retired executives, managers, supervisors, trades people and operators will begin a new generation of building their own trial-and-error library of information.
Of course, this library will be a virtual one, undocumented and not very large in scope, demonstrating a severe unconscious incompetence.
The book Learning to Fly by British Petroleum employees Collison and Parcell describes unconscious incompetence as the state at which companies operate when they are unaware there is a better way to perform.
The authors suggest that a predictable pattern is available in which a company can achieve and sustain a change in culture as a function of time and effort. The end result would be employees who can execute their roles with an unconscious competence that encompasses the most accurate and efficient way to complete the task at hand.
Obviously, the gap between unconscious incompetence and unconscious competence can be enormous. Without ideal knowledge management tools in place, the new employees replacing our retirees fall right into this gap, approaching their new roles without the knowledge of past heuristics to guide them. And without a strategic plan to escape the cycle of trial and error, the productivity of a company will be jeopardized.
As productivity drops, companies will be forced to pass the cost of an unreliable operation to the consumer. Eventually, every consumer good will pass its inflated cost on to us.
A Way Out
It is inevitable that in the coming years, all industries will suffer the blow from corporate amnesia in one way or another. Some companies will do whatever it takes to deviate from this dilemma.
Knowledge management software, comprehensive exit interviews, job shadowing and documented desk procedures will help ease the daunting task. But as maintainers and reliability professionals, how can we ensure the reliability of our production equipment is as streamlined and effective as possible?
Procedure-based maintenance is more than just a buzz word in production and maintenance offices around the world. Procedure-based maintenance is a strategic and tangible method of collecting data on current maintenance, production and operating methods, analyzing the information and improving on it through technology, heuristics and proven techniques, then documenting the information in a user database.
I realize this may sound like a difficult task, but I also know that virtually every production company already has a similar, if at times crude, system in place, where employees and visitors can access information either in hard copy or by intranet. I can walk into any company and before completing the site orientation, I know where to locate or how to access the material safety data sheets (MSDS).
If the same approach can be taken for maintenance tasks and a database of procedures is developed, we can battle the corporate amnesia already taking place.
Knowledge Management
Knowledge management is more than just collecting information and regurgitating it into an accessible format; it has to be a dynamic, evolving enterprise. For example, if the MSDS in production facilities remained static, or in other words, was never regularly updated to reflect the current inventory of materials, it would be useless.
The same holds true for maintenance procedures. If we do not periodically update maintenance procedures to reflect changes in technology - machine configuration, equipment age, and changes in economic penalty of failure or machine criticality - they too will become useless over time.
Knowledge management has always been an issue for the majority of companies that rely on the expertise of its employees. In the coming years, as our industries correct themselves to satisfy the aging workforce, corporate amnesia will be a daily topic of discussion.
The shift of knowledge from employee to dynamic database must begin immediately and we have to manage that dynamic database just like any other corporate asset.
References
- Field, Anne. “When Employees Leave the Company, How Can You Make Sure Their Expertise Doesn’t?” Harvard Management Communication Letter, April 2003.
- Troyer, Drew. “Year 2008 - A Staff Oddity.” Machinery Lubrication magazine, March-April 2003.
- Troyer, Drew. “Change Your Lubrication Culture, Not Your Oil.” Machinery Lubrication magazine, May-June 2003.
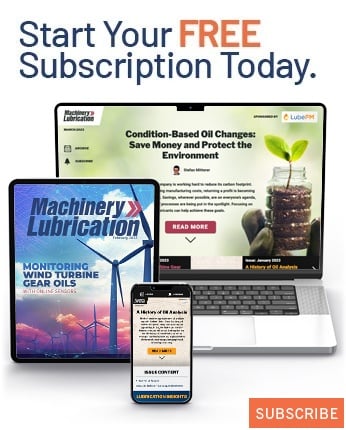