Lube oil application flaws and contamination are two of the major causes of bearing failures in small steam turbines. Fortunately, modern bearing protector seals can be used to prevent the influx of water (steam) and other airborne contaminants into the bearings, and the seals are readily available.
These bearing protector seals incorporate either the face-on-face magnetically closed or the less expensive rotating labyrinth principles. Both choices make economic sense and merit consideration in new and existing (retrofit-to-upgrade) installations.
How Bad is Oil Contamination?
When considering costs, one should not overlook the deleterious effects of contaminants, even the smallest amounts. The life of an antifriction bearing with as little as 100 ppm of dissolved water in the lube oil will be only 40 percent of the life of the same bearing with 25 ppm dissolved water present.
New oils are not entirely dry and often contain about 50 ppm of dissolved water. Most major bearing manufacturers have published literature on the effects of lubricant contamination2, and these publications can be used as a reference point when estimating cost effectiveness.
Using illustrations, such as Figure 1, that plot the ratio of the lubricant's operating viscosity over its rated (or required or minimum) viscosity (v/v1) on the abscissa (x-axis) against a rolling bearing life adjustment factor displayed on the ordinate (y-axis), it is possible to glean the relevance of lube contamination by solids.
In Figure 1, Region I is applicable only to situations combining cleanliness in the lubrication gap with moderate bearing loading. This situation is rather unrealistic for process pumps and small steam turbines.
Region II is where a high degree of cleanliness has been achieved, which can occur with modern bearing protector seals (Figures 2 through 4). Finally, Region III might be typical for bearing environments that are exposed to an industrial environment, such as bearing housings without effective protector seals.
Using Figure 1 and assuming (v/v1) = 0.5 (a viscosity below the desired level), one could obtain a23= 0.3 in Region III, and a23=1 in Region II. In essence, using effective bearing protector seals would improve bearing life by a factor of three. The values 0.5, 0.3 and 1 were selected because they represent the middle of a region and therefore provide an example.
This presents powerful analytical evidence in support of industry trends toward better bearing housing protection.
Figure 2. Lip Seal (Top Portion) and Modern Rotating Labyrinth Seal
(Lower Portion, also Enlargement on Right Side) 4
Lip Seals vs. Rotating Labyrinth Seals
Electric motors, automobile transmissions, small pumps and numerous other industrial machines are protected against lubricant loss and contamination by lip seals. Although lip seals have served industry for more than a century, they have been utilized only in applications where the elastomeric component received ample lubrication and the shaft surface velocities were moderate. Even in this case, lip seals are wear-prone, and it is universally accepted that rubbing wear increases as the velocity ratio increases.
Reliability-focused owner-purchasers are, therefore, rarely using lip seals in large pumps and small steam turbines. This also explains why bearing protector seals have recently been used either in the form of rotating labyrinth bearing protectors (Figure 2, lower portion and enlargement), or as magnetic seals (Figure 3).
The magnetic seal incorporates face geometry that is modified to facilitate the "wetting out" of the oil mist. A thin film of liquid oil thus provides separation between the stationary (Items 3 and 9) and rotating seal face(s) (Item 1) of Figure 3.
For small steam turbines, the old style, relatively inexpensive lip seal shown in the upper portion of Figure 2 does not represent state-of-art technology. Since 2003, advanced rotating labyrinth seals, like those shown in the lower and right portions of Figure 2, have been successful.
This configuration is presently used on thousands of pumps and other general-purpose machinery. A variant (Figure 4) allows for considerable axial float. It incorporates special sealing materials and is specifically designed for use on bearing housings of small steam turbines.
Conclusions
Like other rotating machines, small steam turbines require bearing protector seals. While lip seals have their place in disposable appliances and machines that, for unspecified reasons, must frequently be dismantled, engineers should look at the entire picture.
For the reliability-focused steam turbine user, preventing contaminant intrusion is important. It can be achieved with cost-effectiveness using either the magnetic bearing housing seal (Figure 3) or the advanced bearing protector seal (Figure 4).
Acknowledgment
This article is derived from the upcoming (October 2008) 2nd Edition of Heinz Bloch and Murari Singh's Practical Guide to Steam Turbine Technology. The McGraw-Hill Publishing Company's permission to use this excerpt is gratefully acknowledged.
References
-
Heinz P. Bloch. Improving Machinery Reliability, 3rd Edition, 1998. Gulf Publishing Company, Houston, Texas, p. 495.
-
FAG Bearings, Schweinfurt, Germany. Ball and Roller Bearings, 1985.
-
Heinz P. Bloch and A. Budris. Pump User's Handbook: Life Extension, 2nd Edition, 2006. Fairmont Publishing Company, Lilburn, Georgia, p. 121.
-
AESSEAL plc, Rotherham, United Kingdom and Knoxville, Tennessee.
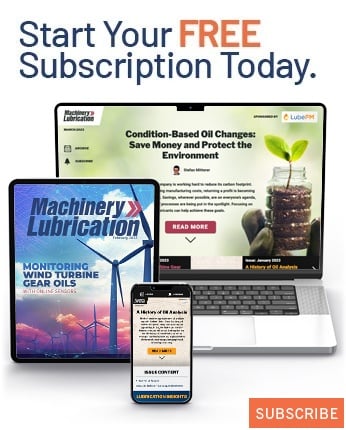