Thick, surface-separating films cannot be maintained at all times in the lubricated elements of turbines and associated equipment. For example, during shutdown, the thick oil film in journal bearings is squeezed out of the pressure area, and some metal-to-metal contact is made. Upon starting (unless oil lifts are used), friction is high and some wear occurs. This boundary lubrication condition continues at least momentarily until the speed is high enough to develop a hydrodynamic fluid film. Boundary lubrication may exist in other situations where speeds are low, loads are high or lubricant supply is restricted.
A properly refined petroleum lubricating oil has considerable natural anti-wear value, or film strength, under boundary lubrication conditions. However, the film strength of modern turbine oils is greatly increased by the use of additives. By chemical action, these materials form tenacious, wear-resistant films on exposed metal surfaces.
The oil in turbine lubrication systems is circulated over and over again for long periods. Its temperature is raised by heat conducted along the shaft from the steam and by heat generated in bearings, gears, pumps, etc. The oil is in contact with warm air, and some air is actually dissolved in the oil. In a few areas, air bubbles may also be entrained. Within bearing and gear housings and reservoirs, some oil is broken into small droplets or mist and is further mixed with air.
Under these conditions, oils tend to oxidize or chemically combine with oxygen. Finely divided metal particles such as iron, copper or lead, which may be present as a result of inadequate cleaning or wear, act as catalysts to promote oxidation. The presence of water also encourages oxidation. The rate of oxidation and the extent of its harmful results depend on the ability of the oil to resist this change.
The effect of temperature on oxidation is significant, with the rate tending to double with each increase of 10 degrees C (18degrees F). The doubling of low rates that prevail at lower temperatures, such as 54 degrees C (130 degrees F) or below, is of little consequence. However, the doubling effect of high temperatures, say more than 82 degrees C (180 degrees F), becomes increasingly drastic.
Slight oxidation of oil is harmless, since the small amount of initial oxidation products formed are carried in solution by the oil without noticeable effect. As oxidation continues, some of the soluble products become insoluble and settle out. Excessive oxidation is accompanied by the formation of substantial amounts of both soluble and insoluble products and by a gradual thickening (increase in viscosity) of the oil.
Insoluble products may be carried with the oil in circulation. Some settle out as gum, varnish or sludge on governor parts, in bearing passages and on coolers, strainers and oil reservoirs. When oxidation is excessive, a substantial layer of deposits may settle on the surfaces, forming an insulating layer that reduces the effectiveness of cooling, which only compounds the problem of increasing temperatures.
In view of the importance of viscosity as a factor in bearing performance, the thickening of oil as a result of oxidation is highly undesirable. An excessive increase of viscosity, coupled with the formation of sludge in ring-oiled bearings, may also retard or prevent the rings from turning and therefore result in starved bearings and failures.
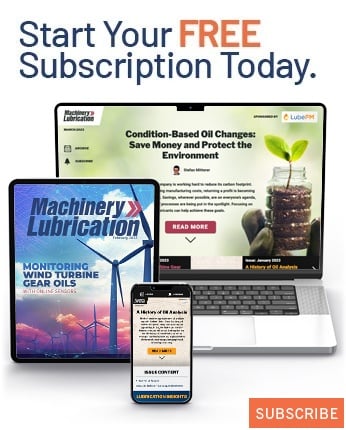