"We recently noticed a small amount of foam in our turbine oil. Is this common, and what could be causing it?"
Foam may result when air is entrained in the oil and thoroughly mixed with it by agitation and churning. A certain amount of foam is always formed in a turbine circulation system, but with correct oil in service, the foam breaks up readily so that normally there is only a very thin layer spread over the surface of the oil in the reservoir.
When excessive foam accumulates in any part of the system, it may overflow or seep away, causing a loss of oil and an unsightly appearance. In some instances, foam escaping from the bearings adjacent to the generator may be drawn into the windings or onto the collector rings where it may cause breakdown of the insulation, short circuits or sparking. Moreover, the large quantity of air carried by the foam increases oil oxidation.
Turbine circulation systems have, in general, been constructed so as to eliminate conditions that have been found to cause foaming. These include leaky pump suctions, excessive splashing or turbulence of oil returning to the reservoir, and oil return lines of insufficient cross-sectional area. Proper vents on reservoirs, oil tanks and gear cases or other more positive methods of reservoir ventilation are usually provided and greatly aid in the breaking up of any foam that forms.
New, high-quality turbine oils should have good resistance to foaming. However, oxidation and contamination tend to destroy this property. Certain oxidation products, finely divided dirt, rust particles, etc., tend to stabilize foam. Therefore, in addition to guarding against contamination, it is again necessary to use an oil of high oxidation resistance in order to preserve initial oil qualities.
Until the middle or late 1940s, straight mineral (non-additive) oils were used in most turbines. Over many years, pressures and temperatures had been increasing. There was also continual growth in turbine generator capacity without a corresponding increase in physical size. As a result, the turbine oil was subjected to heating at higher and higher temperatures. Eventually, conditions were so severe that straight mineral oils did not have acceptable life. It became necessary to strengthen the characteristics of the oils with chemical additives.
The development of turbine oils containing additives to improve resistance to oxidation and to protect metal surfaces against rusting require the development of base oils that are inherently high grade, stable products that respond readily to the addition of additives. These base oils demand careful selection of crude stocks and correct refining.
Of the fire-resistant fluids available, those based on phosphate esters have proven most practical from an overall performance and cost standpoint. These inorganic esters, formulated with carefully selected additives, provide a group of synthetic fluids to replace mineral oil in applications where mineral oil combustibility is hazardous.
The long life, of which high-quality turbine oils are capable, can be fully realized if contamination can be kept at a low level.
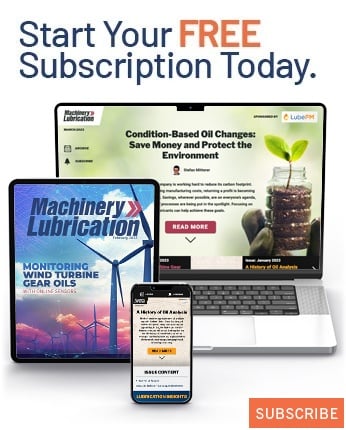