"If we want to perform lube mapping, what data should we collect? What is the best approach for lube mapping?"
Lube mapping is becoming more prevalent as organizations move from tribal knowledge toward procedure-based maintenance. This is a great practice for ensuring all lube points are properly maintained while minimizing the chances of lubricant cross-contamination. Not only does it help new workers identify and address all lubrication points on a given piece of equipment, but it also serves as a check to make sure even the most experienced technicians are hitting all the points as well.
When starting a lube mapping initiative, first plan to conduct an in-depth lubrication audit of your facility. The machines that will receive the most benefit from lube mapping will be those that are complex and critical with numerous lube points. As equipment is built and installed, sometimes these points become hidden and hard to reach, so a thorough audit of the equipment is a must.
Among the pertinent data that should be collected are the lube recommendations from the original equipment manufacturer’s manuals as well as an analysis of how many points are on the machine and the name or location of the individual points. Review the manufacturer’s recommendations and compare them against what is in use in your facility. This will help to confirm that the lubricant meets the equipment specifications and, in the case of synthetic lubricants, make sure it is compatible with seal materials, etc.
It is also important to obtain the equipment’s bearing sizes and speeds as well as the lubricant volumes. This can either be calculated or provided by the machine’s maintenance manual. In addition to knowing the lubricant volume a given point needs, you must also understand how often it needs to be lubricated or the frequency. When calculating the frequency of lubrication tasks, consider the environment in which the equipment operates. For instance, the hotter the environment, the more often grease should be applied.
You can take lube mapping a step further by using detailed, annotated pictures of the equipment. Each lube point can be photographed with a note about the volume, frequency and lubricant type labeled for each point. It is not uncommon to see these types of pictures laminated and hanging from a piece of equipment to enable technicians to visually see all the lube points and make sure they hit all of them.
Lube mapping is an involved process that requires a lot of upfront time and effort. Once the map is created, it must be reviewed periodically and updated whenever lubricant types change or the equipment is modified. Just remember that the end goal is to make the technician’s life easier. Be diligent and thorough in your audits. The more detailed you can be, the better it will be for the technician and your equipment.
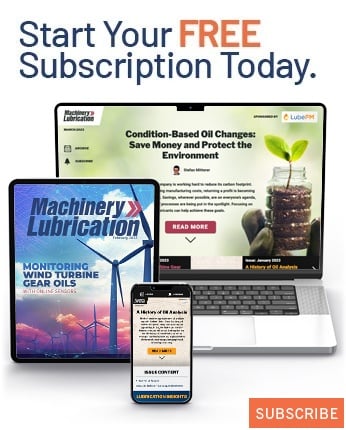