Are you one of those people who checks your car’s oil level before departing on a long road trip? Have you ever asked yourself why it is so critical to maintain the oil level within the hash marks on that dipstick? Of course, the primary reason is to prevent engine failure, but what happens when the engine is low one or two quarts of oil? Can the engine continue to operate in this state without damaging the components and the oil?
This principle of maintaining precise oil levels applies to all types of equipment. I’ve seen instances where the correct oil level was critical. For example, I was once responsible for maintaining two 1,100-horsepower gearboxes. When these gearboxes arrived onsite, I noticed immediately that the upper and lower oil level limits were within one-half inch of each other on the dipstick.
Both gearboxes were on a circulating system. This was a simple system that contained a pump, filter, oil cooler and oil piping to the gears inside the box. At first I didn’t understand why the oil level had to be so precise on a force-fed system. Later, when looking at the blueprint of the gearbox, I discovered why it was so important. These gearboxes had input bearings that didn’t receive oil from the circulating system.
The only oil introduced to these bearings was the oil that was maintained in the sump. Letting the oil level drop below the specified mark on the dipstick would allow the oil to fall below the input bearing housing and cause the bearings to run dry.
Automobiles
Most people jump into their cars every day and commute to work, school or other locations. It has become a convenience to schedule an appointment to have a local dealership, mechanic or service station maintain your vehicle for you. They tell you when your next oil change should be, make necessary repairs and even keep service records for you.
Why are these inspections so important for lubricated components? In addition to changing your automobile’s fluids at specified mileage intervals, technicians are also looking for leaks that could cause different components to fail due to a lack of lubrication. A car has many components that require some sort of lubricant. The expensive ones are the drivetrain, engine, transmission and differential. If one of these fails, you’re looking at major repair bills.
Take the engine, for example. The manufacturer specifies how much oil the engine should hold. For instance, my car takes 6.5 quarts. While this may seem like a lot, the engine oil performs different functions besides just lubricating the crank, cam and other components. One of its jobs is to cool the frictional surfaces and give the oil time to cool down before being reintroduced to the delivery system. Another is dispersing contaminants within the sump.
A high oil level in the crankcase can lead to oil churning. Depending on the severity, this increased agitation can result in foaming problems. Churned motor oil produces increased oil temperatures, which causes oil oxidation and lower oil pressures. Aerated oils become spongy and harder to pump, which can lead to starvation within the engine.
A low oil level in the crankcase can also result in lubricant starvation if it is low enough. However, just being one quart of oil low can make a difference in the life of the engine and the oil. With less oil in the sump, the same oil must now make more passes through the system without a cooldown and release period.
The frictional zones within the engine that generate heat are exposed to higher temperature oil, which will start to oxidize faster. Also, being low a quart of oil changes the amount of additives in the system and how they are depleted. While being one quart low won’t lead to an immediate failure, it has a huge impact on engine longevity.
Gearboxes
When discussing gearbox oil delivery systems, there are two primary types: circulating systems and splash- or bath-lubricated systems. Circulating systems deliver oil to the bearings and gears inside the housing by use of a pump. These systems usually consist of a pump, filter, oil cooler and piping to supply fresh oil to internal components.
With splash- or bath-lubricated systems, the internal components of the gearbox are partially submerged, allowing the lubricant to be picked up to create a lubricating film. Although each of these systems operates using different principles, they have the same goal: supply lubricant to the internal components to reduce friction.
When maintaining circulating systems, being low on oil generally isn’t as devastating to the internal components as it is to the lubricant. You just don’t want too high or too low of an oil level. I have found that when running an oil cooler in line with the flow of fluid, you can get away with a lower oil level without damaging the equipment and the oil. However, if the oil level gets too low in the system, the pump may start to suck air and decrease the amount of oil delivered to the internal components.
In splash- and bath-lubricated systems, a precise oil level is very important. If the level is too high, the oil can aerate and may not deliver a substantial oil film. Frequently, foaming issues result if the oil level is too high in a splash-/bath-lubricated gearbox. If the oil level is too low, lubricant is starved from component surfaces and rapid wear is generated, causing machine failure.
This is probably one of the costliest failures due to metal-on-metal friction, which can lead to shaft, housing and other machine damage. It’s crucial when installing or maintaining splash- or bath-lubricated gearboxes to set the oil level correctly. Failure to do so can be the difference between getting one hour or 10 years of operation.
Pumps
Maintaining a correct oil level is also critical to the operation of oil-lubricated pumps. I’ve been in many plants that employ constant-level oilers. When asked why they use this type of device, the response is usually because it came with the pump or to check the oil level. However, constant-level oilers should not be used to determine the oil level.
Think of it like a dog’s water bowl with a 2-liter bottle for a reserve. The constant-level oiler supplies oil when the level decreases in the sump, just like the reserve of water refills the bowl when your dog takes a drink. While the water level in the dog’s bowl doesn’t matter as long as there’s some water in the bowl, the oil level in your pump does matter.
The majority of pumps set the oil level halfway up the lowest roller on the bearing. This supplies adequate lubricant film to the bearings while reducing energy consumption and oil churning.
Damages
Not only does the machine suffer if there is an inaccurate oil level, but so does the lubricant. When oil levels are too low, rapid machine damage occurs. There may be an increase in friction due to boundary conditions from a shortage of lubricant film or viscosity changes created by increased oil temperatures. This metal-to-metal contact is adhesive wear that leads to smearing (material transfer), spalling, pitting and seizing. If oil levels are low for long periods of time, higher equipment rebuild costs may result.
High oil levels usually affect the lubricant properties. Some machine damage may also take place if the level is not corrected. When the oil level is high for long periods of time, the equipment can aerate the oil, which changes the viscosity, speeds up oxidation and uses up additives. If the machine is run in these conditions, the lubricant film strength weakens, boundary conditions form and machine damage may occur.
Causes of Incorrect Oil Levels
Leakage is probably the No. 1 cause of a low oil level. Many points on equipment can suddenly or gradually fail. Seals may pressurize and allow oil to leak. Gaskets can fail due to age or excessive heat. Remember, everyone has leaks of some sort with their equipment. It’s how you deal with these leaks and move forward that will determine if machine damage will occur.
When leaks are discovered, they should be categorized by priority, tagged and entered into the maintenance system for repair or monitoring. Typically, employees will notice a small leak and ignore it or top off the oil to the correct level and go about their day. Of course, small leaks turn into bigger leaks that can be more difficult to remedy. Even if a leak remains small, over time there will be increased lubricant consumption, disposal and labor.
Another cause of an incorrect oil level is misunderstanding the recommendations from the original equipment manufacturer (OEM). Sometimes it’s not clear where the level should be and may depend on how you look at it from different positions and angles. The OEM manual should have diagrams and instructions on where to set the oil level in your equipment.
If you are still confused as to where the level should be, call the manufacturer and ask. It is crucial to get it right. If you fail to maintain the correct oil level from implementation, internal damage can happen immediately and shorten the life of the equipment.
The oil level should also be clearly marked for field inspection. I’ve often seen oil level indicators with no markings to specify where the level should be maintained. This is especially important with column-level indicators where the oil level can range 6 to 15 inches depending on the length of the indicator.
Remedies
A number of things can be done to ensure the right oil level is maintained in your equipment. As mentioned previously, the oil level should be determined before the equipment is turned on for the first time. The best time to decide on the appropriate oil level is when the equipment first arrives at your facility. This is when all the decisions are made on how to retrofit the equipment for your reliability goals.
Once the correct oil level is identified, it must be clearly marked in the field. This can be achieved with upper and lower limits on the column indicator. Use a material that is durable enough for the environment. Also, record the lubricant volume and other relevant notes in a database.
Develop procedures for everyone to follow, including what to do if a low or high oil level is discovered. Reporting a problem at this phase can help with troubleshooting later for a root cause analysis. Not all problems show up right away within your equipment. It may take months or years before a small defect becomes a big issue.
In addition, address when the oil level should be read. When machinery is operational, the oil level usually reads less. This can lead to false readings and added work. I’ve seen situations when an oil level was topped up to the upper limit while the machine was running. When the equipment was shut down, the oil level was past the upper limit.
Don’t forget to record all top-up volumes. What might be a small leak today could turn into a large leak tomorrow. All leaks should be reported and prioritized.
Finally, train your personnel. Checking a level indicator might seem like a small task, but it is critically important for the reliability of your machinery.
While not every piece of equipment will self-destruct because the oil level is higher or lower than it should be, there are machines that can be expected to fail based on the oil level. In my view, every machine should be treated with the same expectations of controlling the oil level and making sure it is well-maintained.
39% | of lubrication professionals do not maintain precise oil levels in the sumps and reservoirs at their plant, according to a recent survey at MachineryLubrication.com |
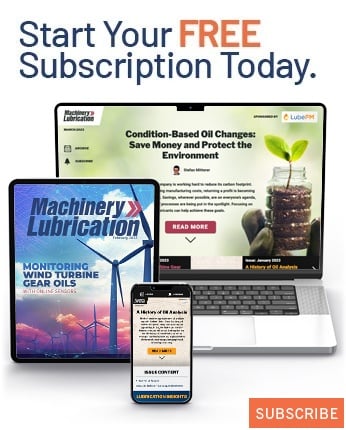